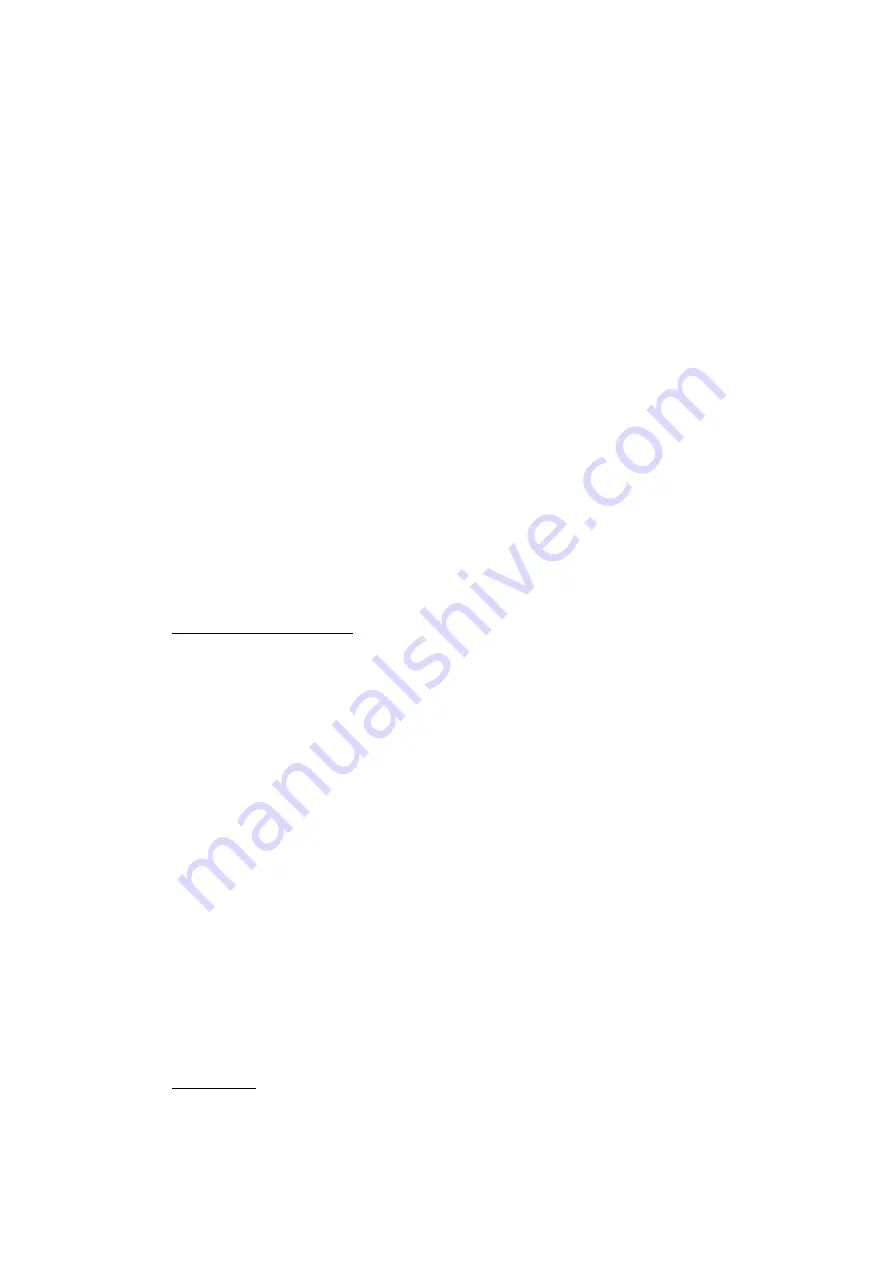
m. When high pressure grease guns are used, protective gloves should always
be worn and care taken to avoid injecting grease under the skin.
n. Hoses used for steam cleaning should be of the type made for steam service.
The metal nozzle should always be securely clamped to the hose and
maintained in serviceable condition.
o. A flammable liquid within the classification of Class ‘A’ or Class ‘B’ petroleum
should not be used for cleaning purposes, except in very special
circumstances, and then by written permission only.
p. Loose boards and materials not in use should be removed from the derrick
floor.
q. Steps and guard rails, where applicable, should be maintained in good
condition. If it is necessary to remove them temporarily during installation of
the machinery, they should be replaced without delay when finished.
r. To eliminate slipping hazards, drilling rig floors, etc. should be kept as free of
mud and oil as practicable. Better footing is provided if the floor is washed
while the next stand of pipe is being picked up. Non-skid materials are useful
in some areas to prevent slipping.
1.5.9 SITE ABANDONMENT
a. Every uncompleted borehole should be fenced or temporarily capped in a
safe manner when the rig has moved off and until the hole is finally capped.
b. Unless a borehole is required to be kept open for some specific purpose, it
should be infilled, consolidated and capped in such a manner that there will
be no subsequent depression at ground surface due to settlement of the infill
material.
c. Surface standpipe should be withdrawn or cut at least one metre below
ground level prior to infilling the borehole.
d. Capping pads should be placed at least one metre below ground level.
e. Mud and slurry pits should remain adequately fenced and signposted until
emptied, backfilled and consolidated. Any impervious membrane should be
removed prior to restoration.
f. The site should be left in a safe, clean and tidy state, with all gates and
fences left as found.
1.5.10 TRAINING
a. The most important factor of all on site safety is the full education and
practical technical training of all drill crew members in all aspects of drilling
and associated operations.
Summary of Contents for TERRIER Mk 1
Page 2: ......
Page 3: ...SECTION 1 GENERAL...
Page 4: ......
Page 24: ...FIGURE 1 1 SAFETY WEDGE LOCATION...
Page 28: ......
Page 29: ...SECTION 2 TECHNICAL DATA...
Page 30: ......
Page 33: ...SECTION 3 OPERATING INSTRUCTIONS...
Page 34: ......
Page 37: ...FIGURE 3 2 VALVE CONTROLS A B C...
Page 44: ......
Page 45: ...SECTION 4 GUIDANCE FOR DRILLING APPLICATIONS...
Page 46: ......
Page 52: ......
Page 53: ...SECTION 5 RIG MAINTENANCE AND SERVICE...
Page 54: ......
Page 70: ......
Page 71: ...SECTION 6 SPARE PARTS ILLUSTRATIONS AND LISTINGS...
Page 72: ...23...
Page 74: ...25...
Page 76: ...27...
Page 78: ...29...
Page 80: ...31...
Page 82: ...33...
Page 84: ...35...
Page 86: ...37...
Page 88: ...39...
Page 90: ......
Page 91: ...SPARE PARTS ILLUSTRATIONS AND LISTINGS FOR UNDER CARRIAGE ENGINE...
Page 92: ......
Page 93: ......
Page 94: ......
Page 95: ......
Page 96: ......
Page 97: ......
Page 98: ......
Page 99: ......
Page 100: ......
Page 101: ......
Page 102: ......
Page 103: ......
Page 104: ......
Page 105: ......
Page 106: ......
Page 107: ......
Page 108: ......
Page 109: ......
Page 110: ......
Page 111: ......
Page 112: ......
Page 113: ......
Page 114: ......
Page 115: ......
Page 116: ......
Page 117: ......
Page 118: ......
Page 119: ......
Page 120: ......
Page 121: ......
Page 122: ......
Page 123: ......
Page 124: ......
Page 125: ......
Page 126: ......
Page 127: ......
Page 128: ......
Page 129: ......
Page 130: ......
Page 131: ......
Page 132: ......
Page 133: ......
Page 134: ......
Page 135: ......
Page 136: ......
Page 137: ......
Page 138: ......
Page 139: ......
Page 140: ......
Page 141: ......
Page 142: ......
Page 143: ......
Page 144: ......
Page 145: ......
Page 146: ......
Page 147: ......
Page 148: ......
Page 149: ......
Page 150: ......
Page 151: ......
Page 152: ......
Page 153: ......
Page 154: ......
Page 155: ......
Page 156: ......
Page 157: ......
Page 158: ......
Page 159: ......
Page 160: ......
Page 161: ......
Page 162: ......
Page 163: ......
Page 164: ......
Page 165: ......
Page 166: ......
Page 167: ......
Page 168: ......
Page 169: ......
Page 170: ......
Page 171: ......
Page 172: ......
Page 173: ......
Page 174: ......
Page 175: ......
Page 176: ......
Page 177: ......
Page 178: ......
Page 179: ......
Page 180: ......
Page 181: ......
Page 182: ......
Page 183: ...SPARE PARTS ILLUSTRATIONS AND LISTINGS FOR 7 1 HYDRAULIC ROTARY ATTACHMENT OPTIONAL EXTRA...
Page 192: ......
Page 193: ...APPENDIX A KUBOTA DIESEL ENGINE...
Page 194: ......
Page 195: ......
Page 196: ......
Page 197: ......
Page 198: ......
Page 199: ......
Page 200: ......
Page 201: ......
Page 202: ......
Page 203: ......
Page 204: ......
Page 205: ......
Page 206: ......
Page 207: ......
Page 208: ......
Page 209: ......
Page 210: ......
Page 211: ......
Page 212: ......
Page 213: ......
Page 214: ......
Page 215: ......
Page 216: ......
Page 217: ......
Page 218: ......
Page 219: ......
Page 220: ......
Page 221: ......
Page 222: ......
Page 223: ......
Page 224: ......
Page 225: ......
Page 226: ......
Page 227: ......
Page 228: ......
Page 229: ......
Page 230: ......
Page 231: ......
Page 232: ......
Page 233: ...APPENDIX B MESSERSI MINI TRANSPORTER...
Page 234: ......
Page 235: ...USE MAINTENANCE 03672872 MINITRANSPORTER TCH K722 N ______________...
Page 236: ...2...
Page 273: ...39 10 10 NOTES ON MAINTENANCE DATE WORK PERFORMED HOURS WORK PARTS INVOLVED...
Page 274: ......
Page 275: ...APPENDIX C TEST REPORTS...
Page 276: ......