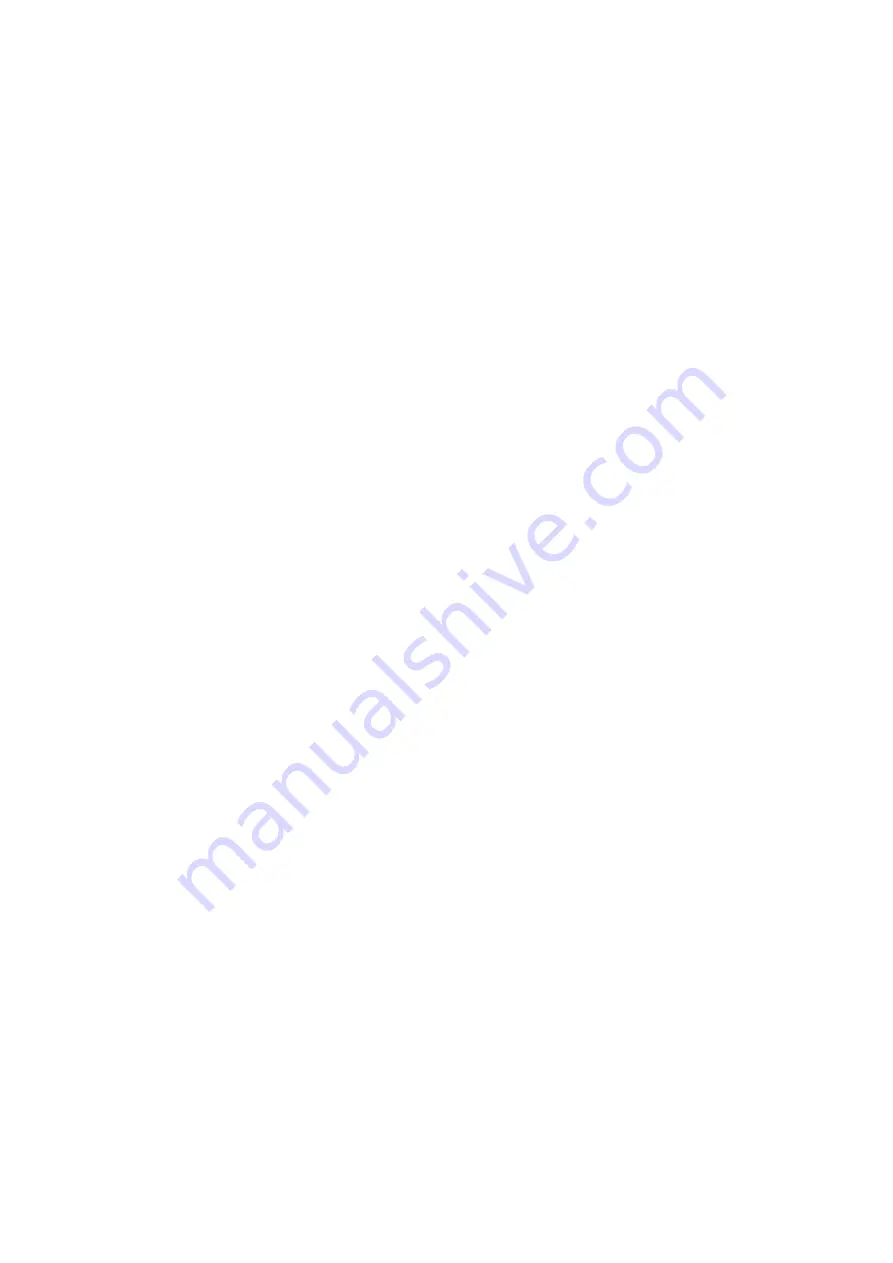
i. Both the compressor and drilling rig should be equipped with air pressure
gauges. Before commencing operations, a check should be made that these
are operative, the readings should be noted, and the main air valve checked
that it is in proper working order and can be used easily and quickly. This
valve should be of the plug cock type.
j. Hoses and fittings designed for different working pressures should be clearly
distinguished, preferably by colour coding, and should not be used at higher
pressures than that designated.
k. Hoses used for pressures in excess of 18 Bar (250p.s.i.) should be secured
to restraining anchors at each end and at suitable intervals.
l. When working above ground level air hoses should be anchored to prevent
them falling.
m. Air receivers should be marked with the safe working FA.1961 Pressure, and
be fitted with a pressure gauge and a safety valve designated to operate if
that pressure is exceeded.
n. Air receivers should be fitted with suitable drainage facilities and should be
drained off daily or more frequently if there is a high humidity level.
o. Air receivers should be thoroughly cleaned and examined at least once in
every period of twenty-six months by a competent person and a report on the
results of every such examination and test should be recorded.
p. In freezing conditions, all air exhausts and air lines being blown out should be
directed well away from workmen.
q. When air-flush drilling an extractor or hood should preferably be used at the
top of the borehole to direct air and dust away from the operators. Where
this is not practicable consideration should be given to the introduction of
foam into the air line and where this is not possible the drilling crew should
wear suitable masks and goggles.
r. Compressed air should not be used for odd jobs such as removing liquid
from, or cleaning out storage drums, nor for blowing dust from the rig unless
the air line is fitted with the correct end fitments and valves.
s. Compressed air should not be used to blow dust from wearing apparel whilst
being worn since this can cause serious injury or death by embolism in the
blood system.
t. The compressed air supply should never be cut off by kinking or bending
hoses.
Summary of Contents for TERRIER Mk 1
Page 2: ......
Page 3: ...SECTION 1 GENERAL...
Page 4: ......
Page 24: ...FIGURE 1 1 SAFETY WEDGE LOCATION...
Page 28: ......
Page 29: ...SECTION 2 TECHNICAL DATA...
Page 30: ......
Page 33: ...SECTION 3 OPERATING INSTRUCTIONS...
Page 34: ......
Page 37: ...FIGURE 3 2 VALVE CONTROLS A B C...
Page 44: ......
Page 45: ...SECTION 4 GUIDANCE FOR DRILLING APPLICATIONS...
Page 46: ......
Page 52: ......
Page 53: ...SECTION 5 RIG MAINTENANCE AND SERVICE...
Page 54: ......
Page 70: ......
Page 71: ...SECTION 6 SPARE PARTS ILLUSTRATIONS AND LISTINGS...
Page 72: ...23...
Page 74: ...25...
Page 76: ...27...
Page 78: ...29...
Page 80: ...31...
Page 82: ...33...
Page 84: ...35...
Page 86: ...37...
Page 88: ...39...
Page 90: ......
Page 91: ...SPARE PARTS ILLUSTRATIONS AND LISTINGS FOR UNDER CARRIAGE ENGINE...
Page 92: ......
Page 93: ......
Page 94: ......
Page 95: ......
Page 96: ......
Page 97: ......
Page 98: ......
Page 99: ......
Page 100: ......
Page 101: ......
Page 102: ......
Page 103: ......
Page 104: ......
Page 105: ......
Page 106: ......
Page 107: ......
Page 108: ......
Page 109: ......
Page 110: ......
Page 111: ......
Page 112: ......
Page 113: ......
Page 114: ......
Page 115: ......
Page 116: ......
Page 117: ......
Page 118: ......
Page 119: ......
Page 120: ......
Page 121: ......
Page 122: ......
Page 123: ......
Page 124: ......
Page 125: ......
Page 126: ......
Page 127: ......
Page 128: ......
Page 129: ......
Page 130: ......
Page 131: ......
Page 132: ......
Page 133: ......
Page 134: ......
Page 135: ......
Page 136: ......
Page 137: ......
Page 138: ......
Page 139: ......
Page 140: ......
Page 141: ......
Page 142: ......
Page 143: ......
Page 144: ......
Page 145: ......
Page 146: ......
Page 147: ......
Page 148: ......
Page 149: ......
Page 150: ......
Page 151: ......
Page 152: ......
Page 153: ......
Page 154: ......
Page 155: ......
Page 156: ......
Page 157: ......
Page 158: ......
Page 159: ......
Page 160: ......
Page 161: ......
Page 162: ......
Page 163: ......
Page 164: ......
Page 165: ......
Page 166: ......
Page 167: ......
Page 168: ......
Page 169: ......
Page 170: ......
Page 171: ......
Page 172: ......
Page 173: ......
Page 174: ......
Page 175: ......
Page 176: ......
Page 177: ......
Page 178: ......
Page 179: ......
Page 180: ......
Page 181: ......
Page 182: ......
Page 183: ...SPARE PARTS ILLUSTRATIONS AND LISTINGS FOR 7 1 HYDRAULIC ROTARY ATTACHMENT OPTIONAL EXTRA...
Page 192: ......
Page 193: ...APPENDIX A KUBOTA DIESEL ENGINE...
Page 194: ......
Page 195: ......
Page 196: ......
Page 197: ......
Page 198: ......
Page 199: ......
Page 200: ......
Page 201: ......
Page 202: ......
Page 203: ......
Page 204: ......
Page 205: ......
Page 206: ......
Page 207: ......
Page 208: ......
Page 209: ......
Page 210: ......
Page 211: ......
Page 212: ......
Page 213: ......
Page 214: ......
Page 215: ......
Page 216: ......
Page 217: ......
Page 218: ......
Page 219: ......
Page 220: ......
Page 221: ......
Page 222: ......
Page 223: ......
Page 224: ......
Page 225: ......
Page 226: ......
Page 227: ......
Page 228: ......
Page 229: ......
Page 230: ......
Page 231: ......
Page 232: ......
Page 233: ...APPENDIX B MESSERSI MINI TRANSPORTER...
Page 234: ......
Page 235: ...USE MAINTENANCE 03672872 MINITRANSPORTER TCH K722 N ______________...
Page 236: ...2...
Page 273: ...39 10 10 NOTES ON MAINTENANCE DATE WORK PERFORMED HOURS WORK PARTS INVOLVED...
Page 274: ......
Page 275: ...APPENDIX C TEST REPORTS...
Page 276: ......