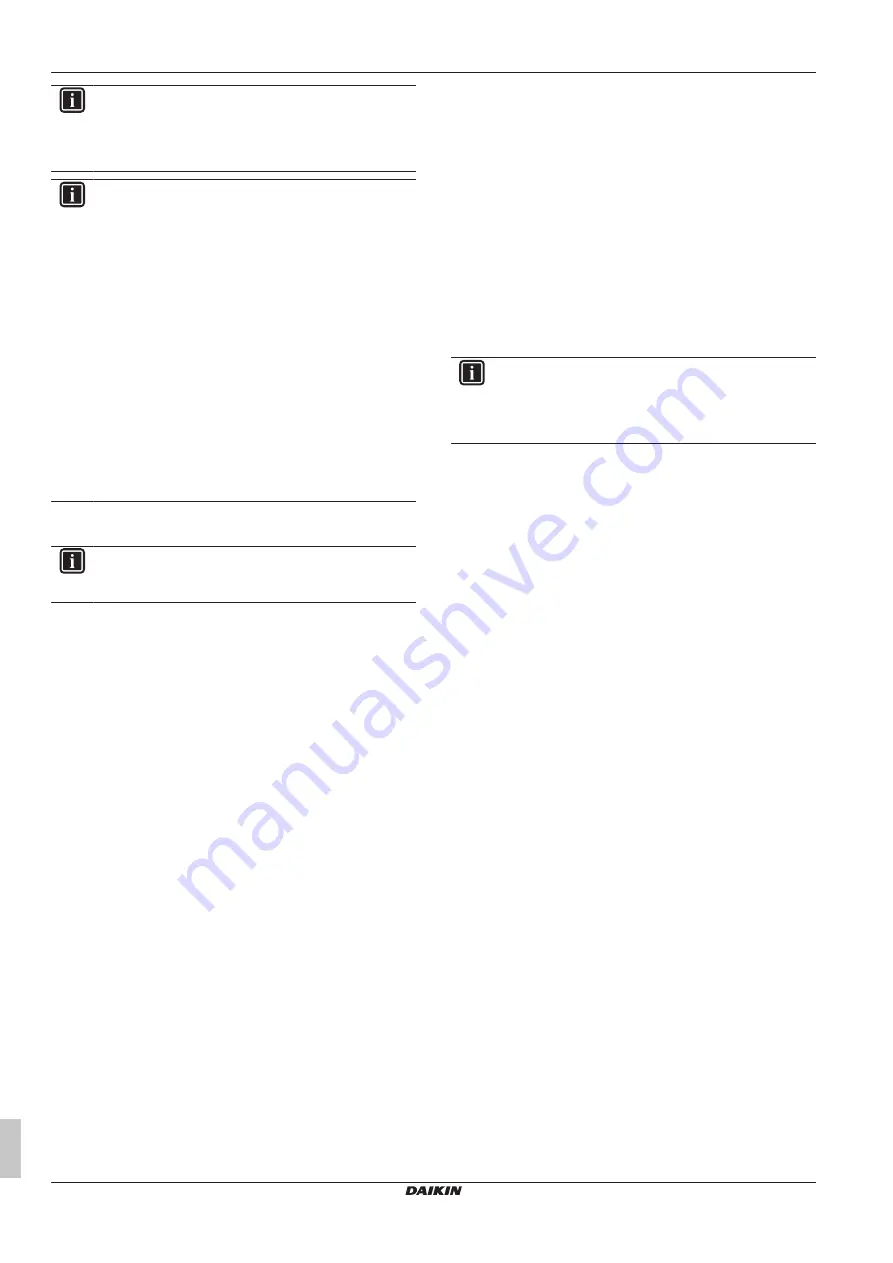
4
Set-up and installation
Installation and operating instructions
18
Gas Combi Unit
Floor-standing gas condensing boiler with integrated heat storage
008.1543899_02 – 04/2019 – EN
INFORMATION
In some cases, the resonance in the flue gas system can
amplify the noise at the mouth of the flue gas duct. The
noise level can be effectively reduced by using a silencer
(
DN 80: E8
MSD
or
DN 110:
E11 MSD
).
INFORMATION
We recommend using the GCU compact in ambient air-in-
dependent operation with a concentric flue gas/air supply
line. If possible, choose this installation variant.
In partial ambient air-independent operation (separate flue
gas/air supply lines with a single-walled connecting pipe)
and ambient air-dependent operation, the installation room
must have a ventilation opening of at least
150 cm
2
to the
outside.
This reduces the overall energy efficiency of the building
according to European Directive 2010/31/EU: EPBD.
The following descriptions of the different set-ups include
information regarding the possible classification of the
devices based on the type of flue gas routing (device type)
in accordance with CEN/TR 1749.
must also be observed in this regard.
) mentioned below are recom-
mendations for the appropriate combination of the required
individual components for the typical installation variants.
4.2.1
Room-air independent operation
INFORMATION
When devices are installed in residential rooms only one of
the installation variants 1 to 4 is permissible.
Installation variant 1
The GCU compact with the
SET GCU1
and the concentric LAS con-
nection line
SET H
or
SET K
is connected to the chimney or an in-
stallation shaft.
▪ The combustible air supply from the outside runs through the
chimney or through an installation shaft.
▪ The flue gas discharge to the outside runs through the same shaft
as the air supply.
▪ Minimum vertical distance between the flue gas exit and roof
ridge:
40 cm
.
▪ Device type C
93
Installation variant 2
The GCU compact is placed directly below the roof. Connection with
SET GCU1
and
SET L
.
▪ The combustible air supply and flue gas discharge run through a
concentric dual pipe.
▪ The combustible air supply from the outside runs through the
outer ring-shaped gap of the dual pipe, and the flue gas discharge
to the outside runs through the inner tube.
▪ Minimum vertical distance between the flue gas exit and roof sur-
face:
40 cm
.
▪ Minimum height of the flue gas pipe:
2 m
.
▪ Device type C
33
Installation variant 3
The GCU compact is not placed directly below the roof. The dual
pipe for the combustible air supply and flue gas duct runs through
the roof truss.
▪ The combustible air supply and the flue gas discharge run through
a concentric dual pipe (as in Installation variant 2).
▪ In the area of the roof truss, the dual pipe for the combustible air
supply and the flue gas duct must be laid through a protective pipe
with sufficient fire resistance or be structurally separated from the
roof truss.
▪ Device type C
33
Installation variant 4
The GCU compact with the
SET GCU1
and the LAS connection line
SET H
or
SET K
is connected to the exterior wall system
SET G
.
▪ The combustible air supply from the outside runs through the ring-
shaped gap in the dual pipe through the outer wall (suction from
below).
▪ The flue gas discharge to the outside runs through a concentric
pipe, through the outer wall and then up to at least
40 cm
over the
roof surface. In the external area, the outer air gap serves as heat
insulation for the flue gas pipe.
▪ Device type C
53
INFORMATION
If the wall feed through is at a height of less than one
meter above the ground, we recommend routing the com-
bustion air through a separate air supply pipe (mounting
height: approx. 2 m).
W8 ZR
or
W11 ZR
Installation variant 5
If, for constructional or legal/regulatory reasons, the shaft used for
the flue gas routing is not suited for also routing the combustion air
at the same time, the combustion air must be routed through a sep-
arate line.
If the flue gas connection line to the shaft is double-walled and is
surrounded by the combustion air, there are no additional ventilation
requirements on the installation room.
▪ The combustion air supply is routed from the outside via the ad-
equately sealed supply line that is connected directly to the con-
centric exterior pipe of the connection line. The supply line should
be dimensioned so that the
suction resistance at nominal out-
put is less than 50 Pa
.
▪ The connection line between the GCU compact and the installa-
tion shaft is completely concentric and surrounded by combustion
air.
▪ Device type C
53
, C
83
Installation variant 7 (not shown)
If permitted by local regulations, the GCU compact can be connec-
ted to
SET W2
to the horizontal flue gas outlet.
▪ The combustible air supply and flue gas discharge run through a
concentric dual pipe.
▪ The combustible air supply runs from the outside through the
outer ring-shaped gap of the dual pipe (supply air inlet via the in-
take grille of the wall feedthrough) and the flue gas discharge to
the outside runs through the inner tube.
▪ Minimum height of the flue gas pipe: 2 m
▪ Observe the local regulations regarding minimum distances of
windows or other building openings.
▪ Device type C
13
4.2.2
Partial ambient air-independent mode
Alternative to installation variant 5
The GCU compact is operated with separately routed supply air/flue
gas lines (2-pipe system).
▪ The combustion air supply from the outside runs through an ad-
equately sealed air supply line through the external wall. The sup-
ply line should be dimensioned so that the
suction resistance
at
nominal output is less than
50 Pa
.
Summary of Contents for GCU compact Series
Page 2: ......