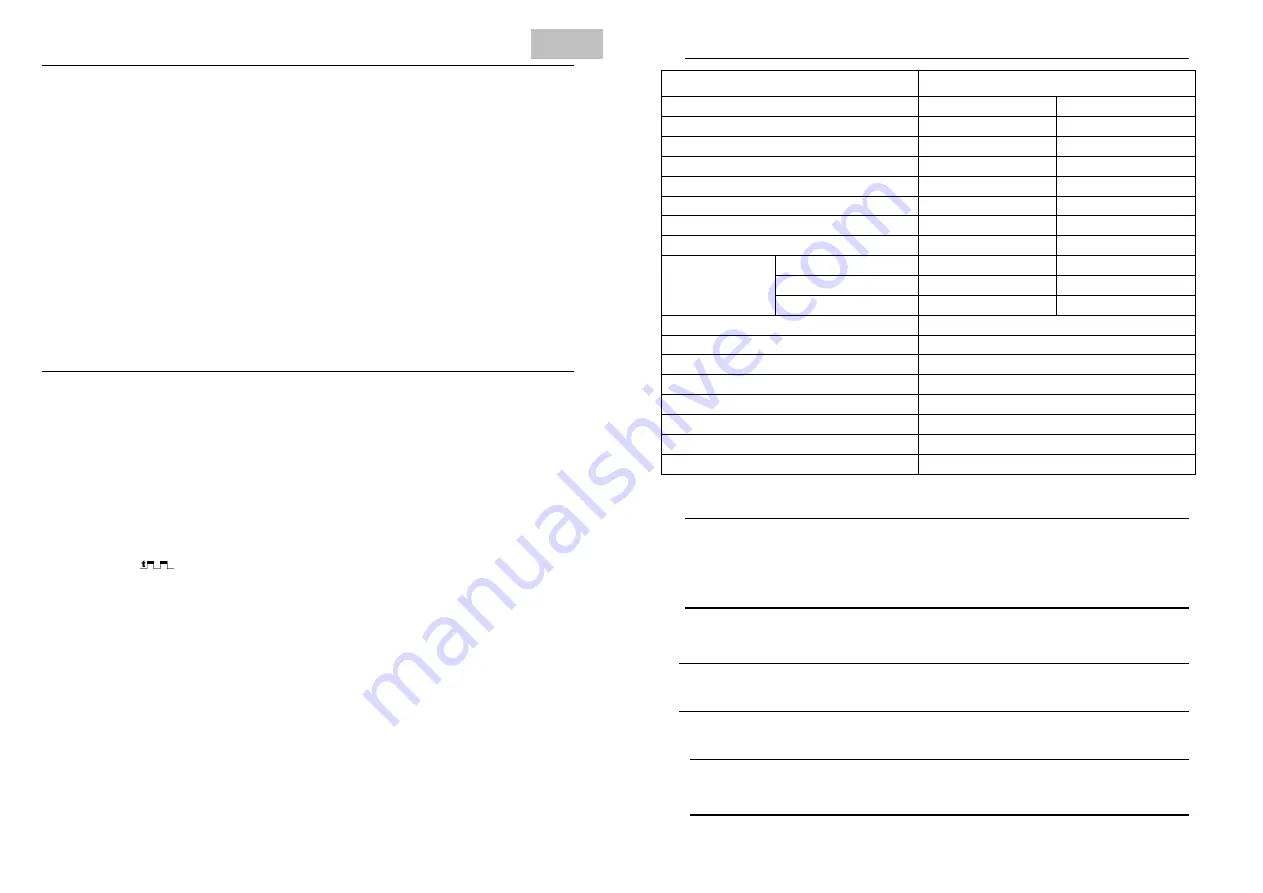
GB
1.6. Transporting the power source
The machine is easy to lift, transport and handle, though the following procedures must
always be observed:
1. The machine may be carried by the power source handle or a nylon strap.
2. Always disconnect the power source and accessories from mains supply before any lifting or handling
operations.
3. Do not drag, pull or lift equipment by the cables.
INSTALLATION ENVIRONMENT
The equipment is not suitable for use in washrooms, shower cubicles, pool areas or similar
environments. If you are obliged to use the unit in such areas, turn off all water supplies and check
the area has been evacuated.
The Welder was not designed for installation or use in areas where it could be subject to blows or
vibration, such as road-vehicles, railway carriages, cable-cars, aircraft, ships or boats or similar
environments (including cranes, conveyor-carriers or any other mobile equipment prone to vibration)
The Welder should never be used or stored in the rain or in snow.
Never use the Welder in an explosive, corrosive, abrasive or saline environment
2. DESCRIPTION OF THE MACHINE
VARMIG Supermig semi-automatic welding machines in this manual are intended for electric-arc welding
in a protective gas atmosphere. As protective gas the following may be used CO
2
,
Argon and gas
mixtures (Ar82% - CO2 18%), depending on the welding material (alloyed or non alloyed steels, bright
metals and their alloys). The machines are particularly suitable for welding thin sheet. They are ideal for
vehicle accident repair shops and industrial use, where smaller welding intensity is required. The machine
construction meet all safety, reliability and design standards of modern welding technique.
Features:
appropriate for welding of steel (thickness 0,5
– 5,0 mm) and stainless steel (thickness 0,5 – 4 mm)
in a gas protection atmosphere Ar/CO
2
mixtures);
high quality of weld-seam;
high working velocity and wide field of use;
simple and easy maintenance and use;
spot welding
UTILISATION FOR INTENDED PURPOSE ONLY
VARMIG Supermig welding machines are intended to be used SOLELY for MIG/MAG welding. Any other
use, or any use going beyond the above, is deemed
to be »not for the intended purpose« and the
manufacturer shall not be liable for any damage resulting there from!
»Utilisation for intended purpose« shall also be deemed to encompass:
the observance of all instructions in the operating manual
The carrying out of all prescribed inspection and maintenance work.
3.
TECHNICAL DATA
VARMIG 191
Supermig
Mains connection
230V/50Hz
400V/50Hz
Max. power consumption
4,6 kVA
6,8 kVA
Fuse / slow
16 A
16 A
No/load voltage
27,6-44,6 V
38,0
–52,8 V
Idle state comsumption
21 W
21 W
Efficiency
56,3 %
58,5 %
Welding current
35
–120 A
90
–165 A
Welding voltage
15,8
– 20,0 V
18,5
– 22,3 V
Duty cycle
(40
ºC)
10%
120 A
165 A
60%
60 A
60 A
100%
47 A
47 A
cos
0,83 (85 A)
Welding current regulat.
2 x 6 stopenj
Spot welding time
0,5
– 2 sek
Welding wire diameter Ø
0,6
– 0,8 mm
Insulation class
IP21S
Cooling
ventilator
Weight
40 kg
Dimensions LxWxH (mm)
733x430x640
4.
CONSTRUCTION
These semi-automatic welding machines have compact design, small dimensions and therefore they are
very mobile and suitable for work in smaller rooms, hard conditions, where frequently movement is
required. The extended bottom above the wheels is intended to carry the gas cylinder (max 20l). The
wire-spool holder and the wire feeder are installed inside the housing.
4.1 The housing of the machines
The housing is made of high-quality material and it is modern-designed. The cover on the top is easy to
open, so the wire-spool can be changed easily.
4.2 Power transformer
The transformers for VARMIG 191 Supermig are combined, for connection to the 230 and 400 V mains
supply. H-insulation class, the primary and secondary coil is galvanicaly separated.
4.3 Silicon rectifier stack
It is made of cooling ribs with pressed-in diodes, which are connected to bridge. This rectifier stack is
used for rectifiing of welding current.
4.4
Choke
It has a great influence on the quality and dynamics of welding process. It's construction enables the
highest possible choking of frequency oscillation by welding-arc's short-circuit.
4.5
Electronic board
It serves for regulation of wire feeding motor and wire speed and for spot and intermittent welding as well.