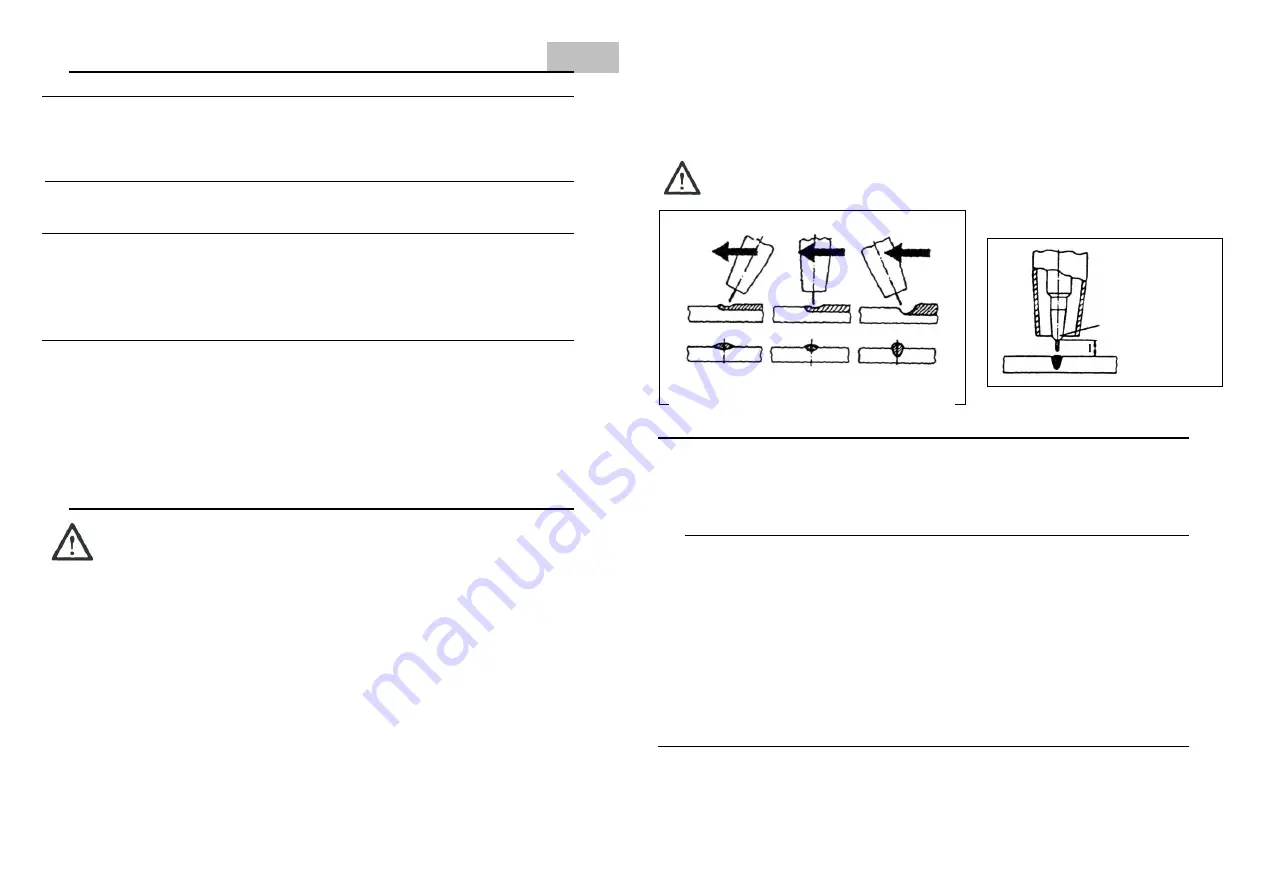
GB
6.
PREPARING FOR WELDING
6.1. Mains connection
Varmig 191 Supermig welding machines are equipped with connection for 1 x 400V/50Hz and
230V/50Hz. At connection to 230 V mains supply use the appropriate adapter enclosed.
Please assure, that the main switch is in position
0
before connecting the cable to the plug
socket.
6.2 Mounting the wire spool
Mount the wire-spool (low alloyed steel) onto the spool holder. Please pay attention to the correct
direction of unwinding the wire by mounting the spool.
6.3 Leading-trough the wire
The wire has to be bend before leading it trough the feeding rollers and infeed tube of welding torch to
avoid sticking. With turning the screw to the left release the spring and shift up the clamping handle with
the braking-roller. Assure, that the groove on the feeding-roller is equal to the welding wire diameter.
Insert the wire trough the infeed tube of the roller drive and a few cm into the infeed tube of the welding
torch. Adjust the appropriate pressure of the feeding roller with turning the screw to the right (the feeding
roller may not slide on the wire).
6.4 Gas cylinder
place the gas-cylinder onto the backside of the machine (max 20 kgs) or floor
fix the gas-cylinder in place with safety chain
N.B.! The cylinder will only be optimally fixed in the upper part of the cylinder (not at the neck)
remove the protective cap from the gas cylinder
give the gas-cylinder valve a brief turn to the left (anticlockwise) to blow off any dirt around the valve
check the seal on the pressure regulator
screw the pressure regulator onto the gas cylinder and tighten it
assure, that no gas deserts
attach the protective-gas hose to the gas-pipe on the machine and fix it with enclosed embrace
7.
MIG/MAG WELDING
CAUTION!
Before starting up for the first time read the safety rules.
place the machine onto the working place so, that the best cooling possibility is achieved
plug the machine into the mains
set the protective-gas rate
fix the welding cable onto the central connector on the front of the machine
connect the earth (mass) cable to the work piece
adjust the wire speed with a knob approximately into the middle of the scale
check out if the wire is leaded-trough correctly
remove the protective gas-nozzle and the contact nozzle from the torch
assure, that the chosen contact nozzle is equal to the wire diameter
press the button on the torch and check the wire feed and the gas outflow. If everything is OK, the
wirefeeder is pushing-out the wire and the gas valve is open, so the das is coming out
fix the protective gas-nozzle and the contact nozzle back to the torch
the perfect length of the welding wire outside the nozzle is 5-10 mm (cut off the rest)
depending materials you are intended to weld, choose the suitable parameters with a welding
current-switch and wirespeed-knob
try to weld by pressing the button on the torch. If the chosen parameters are correct the sound of
welding is equable and the seam is well.
The stable arc is very important for quality welding-seam. Please pay attention to the constant distance
between nozzle and work piece and try to guide the torch as constantly as possible. The appropriate
distance between torch and work piece is around 5-10 mm (stainless steel) and 20 mm (aluminium).
The machine is equipped with an over temperature thermostat. If this is active, the orange indicator is lit
up. At that moment the machine is out of order. The cooling system operates only. The machine will fail to
weld until temperature indicator is lit up.
Caution! DON'T SHUT OFF THE MACHINE IF TEMPERATURE INDICATOR IS LIT UP!
CONTACT
NOZZLE
PUSH RECTANGULAR PULL
POSITION POSITION POSITION
7.1. Aluminium welding
For welding of Aluminium as protective gas only pure Argon can be used. For welding of Aluminium the
wirefeeding rollers with »V« groove are to be changed with rollers with »U« groove. Also the spiral infeed
tube on the wirefeeding mechanism is to be changed with a Teflon infeed tube
2/4, l-90 mm long. We
also suggest to replace the usually welding cable with a short welding cable (1,5 m) with a teflon infeed
tube to avoid sticking and bending of wire.
8.
CARE AND MAINTENANCE
Warning!
Before opening the machine, switch it off, unplug it from the mains and put up the warning sign
to stop anybody inadvertently switching it back on again. If necessary, discharge the electrolytic
capacitors.
In order to keep your welding machine operational for years to come, you should observe the following:
carry out safety inspections at the stipulated intervals
depending on the machine location, but no less often than twice a year, remove the side panels from
the machine and blow the inside of the machine clean with dry, reduced blow compressed air. Do not
aim air-jets at electronic components from to close a range.
If a lot of dust has accumulated, clean the cooling-air ducts.
daily check out the nozzles, wirefeeder and rollers, hose, torch, pressure regulator and clean or
replace it if necessary
weekly check out the cables, plugs and replace it if necessary
9. AFTER-SALES SERVICES AND WARRANTY
Please refer to the Warranty (Indemnity) bond!