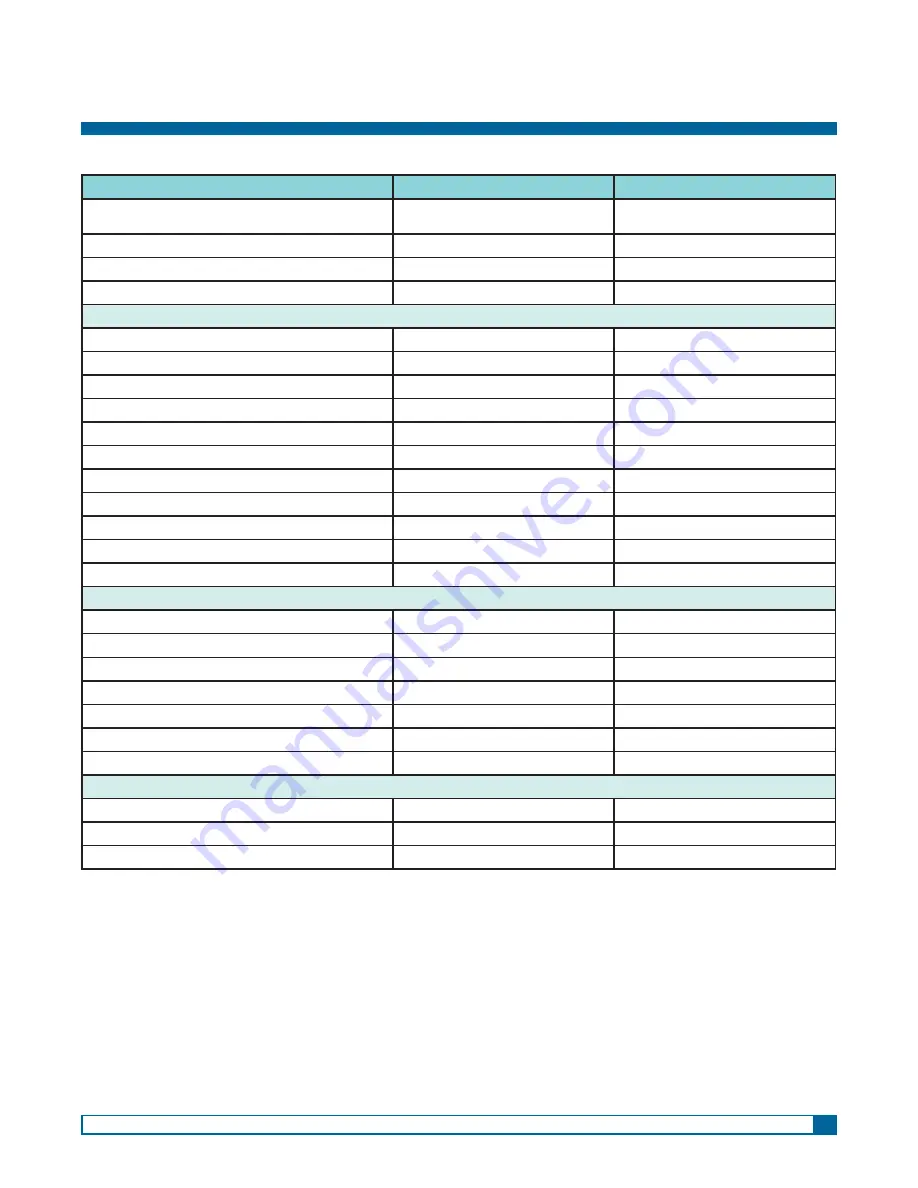
Culligan Aquasential Select Plus & Select Series Iron-OX5 & Sulfur-OX3 Water Filters 01040683
Specifications
6
Specifications
Culligan Aquasential Select Plus Iron-OX5 & Sulfur-OX3 Filters
10ʺ Iron-OX5 Outdoor
10ʺ Sulfur-OX3 Outdoor
Control Valve
1" reinforced thermoplastic with
Accusoft electronics
1" reinforced thermoplastic with
Accusoft electronics
Overall Conditioner Height
67"
67"
Media Tank Dimensions (D x H)
10" x 54"
10" x 54"
Filter Media Type
1.0 ft³ Birm
1.0 ft³ Cullar S
Underbedding
G-50
35 lb
—
Cullsan U
25 lb
—
Cullsan
—
20 lbs.
Capacity¹
500 gallons
500 gallons
Freeboard²
21"
29"
Max. Clear Water (Soluble) Iron
5 ppm
not rated
Rated Hydrogen Sulfide
not rated
1 ppm
Max. Hydrogen Sulfide⁵
not rated
3 ppm
Minimum Alkalinity
100 ppm
100 ppm
pH for Iron Removal³
7.0 - 8.5
—
pH for Hydrogen Sulfide Removal⁶
—
7.0 - 8.5
Service Flow @ Pressure Drop (Clean Bed)
Normal
4 gpm @ 5 psi
4 gpm @ 2.9 psi
Maximum⁴
6 gpm @ 9 psi
6 gpm @ 9 psi
Operating Pressure
20-60 psi
20-60 psi
Operating Temperature
33-120° F (1-48° C)
33-120° F (1-48° C)
Electrical Requirements
24 Volts/60 Hz
24 Volts/50-60 Hz
Power Consumption, Continuous/Maximum
3 Watts/10 Watts
3 Watts/10 Watts
Drain Flow
5.5 gpm
5.5 gpm
Reconditioning Time
Backwash
15 minutes
15 minutes
Air Draw
40 minutes
40 minutes
Fast Rinse
5 minutes
5 minutes
¹ Capacity based on 4 gpm and 5 mg/L of dissolved iron for Iron-OX5 and 4 gpm and 3 mg/l of hydrogen sulfide for Sulfur-OX3.
² Measure from top of media bed to top of inlet fitting.
³ Not recommended for Hydrogen Sulfide removal.
⁴ Max flow rates and pressure drop characteristics have not been validated by the Water Quality Association. The maximum
specified flow rate as validated by the Water Quality Association is defined as normal service flow.
⁵ Not validated by Water Quality Association - based on Culligan International lab testing
⁶ Not recommended for iron removal.