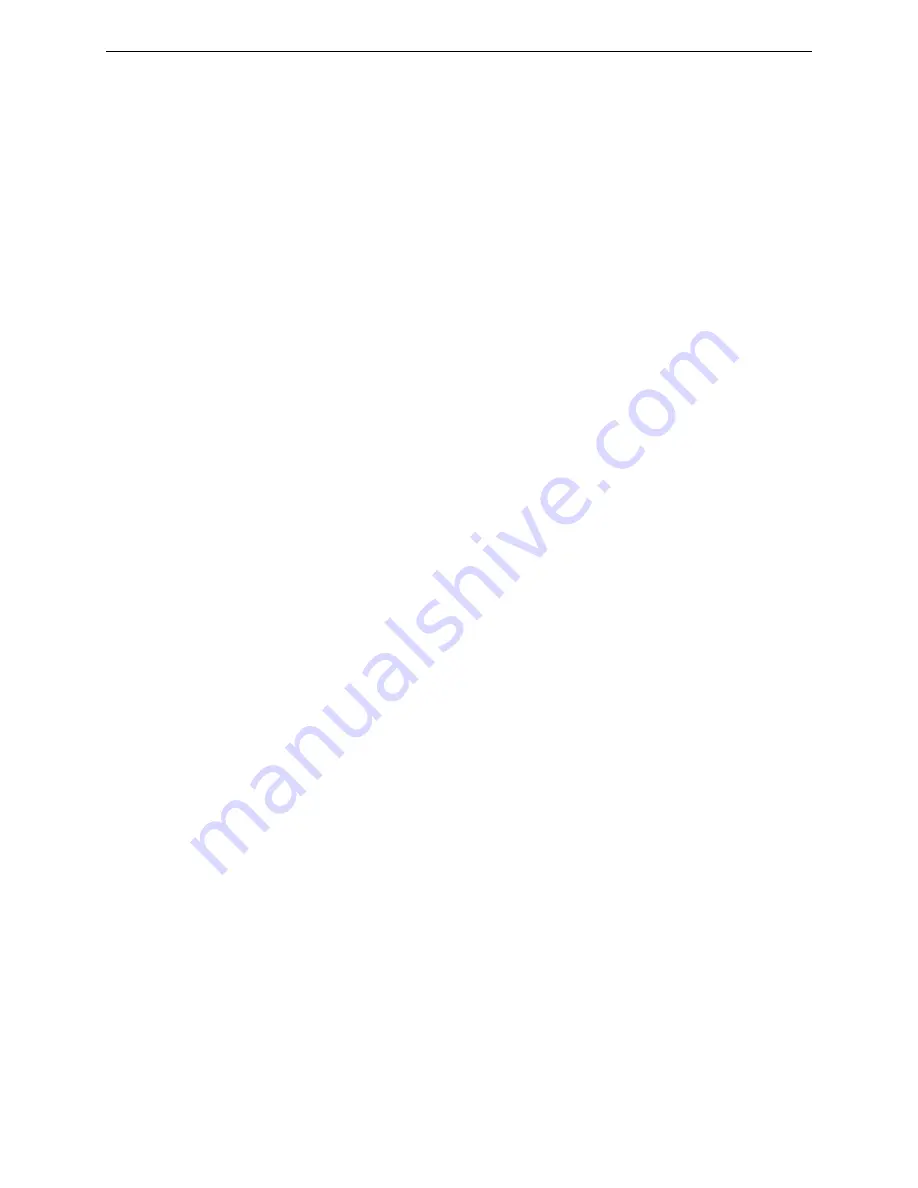
Chapter 10: Preventive Maintenance
91
99-05-31
Battery Maintenance
Background
The absolute encoders of the F3 robot rely on battery power to maintain
multi-turn data when it is not connected to a live controller - i.e. the
controller is turned off or the umbilical cable is disconnected at one or both
ends. This backup supply consists of a pack of three (3) nickel metal hydride
batteries.
The batteries are continuously charged as long as the robot is connected to a
live controller. They can retain sufficient charge for the encoders for at least
six (6) weeks when all power to the robot is down, provided the system has
been connected to a live controller for at least 72 hours prior to the
shutdown.
•
Typical charging voltage is 4.5 VDC.
•
Resting voltage is around 3.6 VDC.
•
The encoders issue an alarm when their power is lower than 3.4 VDC.
•
At lower than 3.0 VDC, the encoders cease to function properly and enter
into a reset state.
Shutting Down the System for Less Than 6 Weeks
Check the battery voltage if you plan to shut down the robot system under
the following conditions:
•
The shutdown will be longer than five (5) days but less than six (6)
weeks.
•
The robot system has not been connected to a live controller for at least
72 hours prior to the shutdown.
Verifying battery voltage of systems shipped in mid-1998 or later
•
With the controller turned off, remove the umbilical cable from the robot
base.
•
Allow the batteries to drain for at least 4 hours from the charging voltage
level to the resting level.
•
Use a voltmeter or digital multi-meter to measure the voltage across pins
A1 and A5 in the umbilical connector at the robot base.
Verifying battery voltage of systems shipped in 1997 to early 1998
These robots may not have the battery pins installed. In this case, the
following procedure is necessary to measure the battery voltage.
•
With the controller turned off, remove the umbilical cable from the robot
base.
•
Allow the batteries to drain for at least 4 hours from the charging voltage
level to the resting level.
•
Use a 2.5 mm hex key to remove the seven (7) M3 socket head screws
securing the fibre drawer to the base of the robot.
•
Allow the fibre drawer to withdraw on its own from its cavity in the base.
It will recede roughly 1 cm (0.4”).
Summary of Contents for F3
Page 1: ...F3 Robot Arm for C500C Controller User Guide UMI F3 310 ...
Page 3: ...99 05 31 iii ...
Page 4: ...iv 99 05 31 ...
Page 8: ...viii 99 05 31 ...
Page 18: ...4 F3 Robot Arm User Guide 99 05 31 ...
Page 44: ...30 F3 Robot Arm User Guide 99 05 31 ...
Page 52: ...38 F3 Robot Arm User Guide 99 05 31 Reach of F3 with servo gripper dimensions in inches mm ...
Page 70: ...56 F3 Robot Arm User Guide 99 05 31 ...
Page 92: ...78 F3 Robot Arm User Guide 99 05 31 ...
Page 98: ...84 F3 Robot Arm User Guide 99 05 31 ...
Page 112: ...98 F3 Robot Arm User Guide 99 05 31 ...
Page 114: ...100 F3 Robot Arm User Guide 99 05 31 ...
Page 116: ...102 F3 Robot Arm User Guide 99 05 31 ...
Page 126: ...112 99 05 31 ...