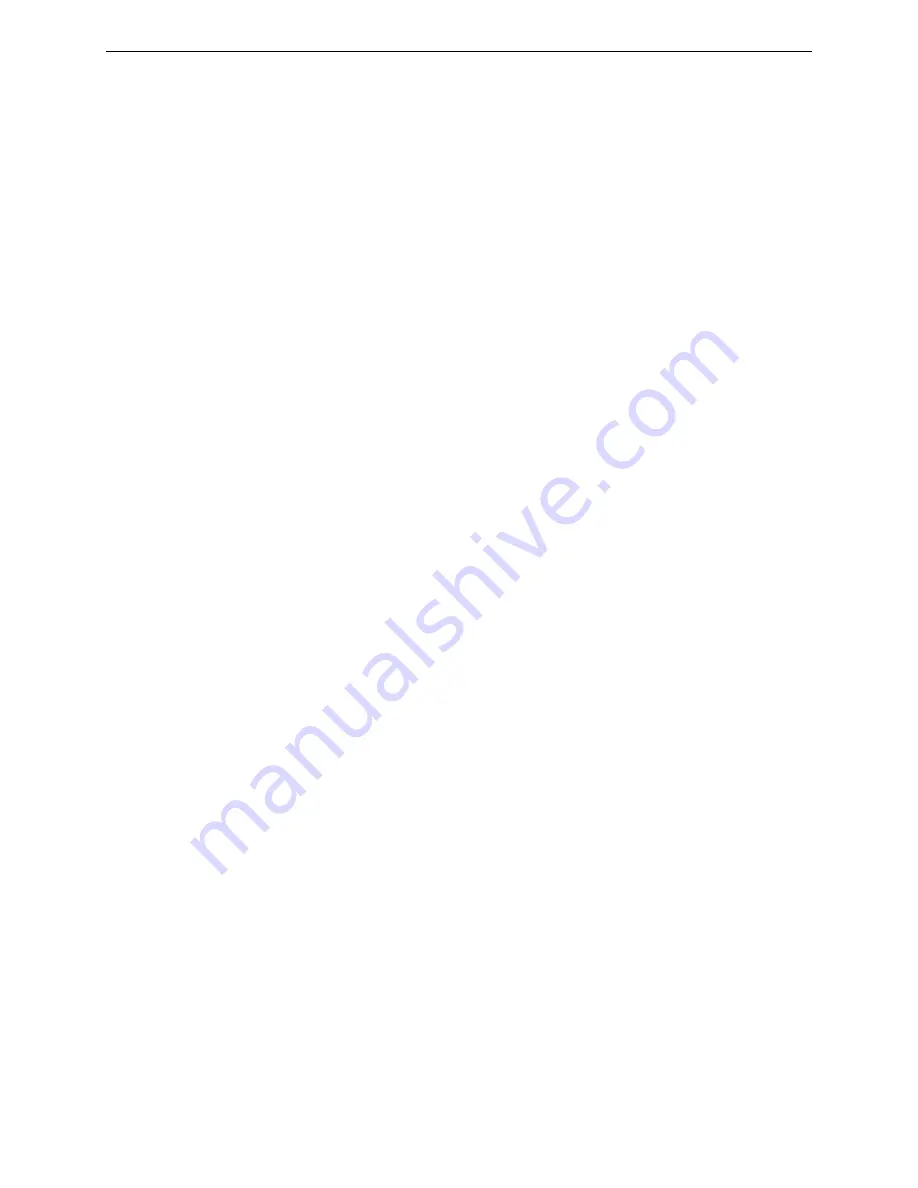
Chapter 10: Preventive Maintenance
83
99-05-31
Procedure for Re-Homing
1.
Verify that the proper calibration file robot.cal is in the /conf directory. If
it is not there, restore it.
2.
Verify that arm power is off. If not, hit an E-Stop.
3.
Verify that there is no application process running on the controller by
using the ps command. CTRL-E terminates application processes started
from ash, the system shell, or the teach pendant.
4.
Manually back-drive the robot to align the calibration markers. (In some
F3 robots, the marker is a pair of triangles on either side of a joint. The
user should line up the opposing vertices of the triangles. Other robots
have markers with a triangle on one side and a small alignment band on
the other.)
5.
Reset the wrist encoders by entering the command
/diag/encres
When prompted, enter module address
8
(decimal) or 0x08 (hexadecimal). If there is an error message, it indicates
encoder error for one or more of the wrist axes.
6.
Reset the lower arm encoders by entering the command
/diag/encres
When prompted, enter module address
16
(decimal) or 0x10 (hexadecimal) for the lower three joints. If there is an
error message, it indicates encoder error for one or more of the lower arm
axes.
7.
For a track system, reset the track encoder by entering the command
/diag/encres
When prompted, enter module address
80
(decimal) or 0x50 (hexadecimal).
8.
Turn off the controller and keep it off for at least 10 seconds.
9.
Turn on the controller.
10.
Test whether the robot has been correctly re-homed as follows:
a.
Turn on arm power.
b.
Start the application shell by entering
ash test.
c.
E
nter the command
calrdy
. This brings the robot into the vertical
configuration.
d.
Inspect the calibration markers to ensure they are properly aligned. If
any joint is mis-aligned (if a pair of markers is not exactly aligned),
the markers were not properly lined up in step 4. If so, turn off arm
power. Back-drive the joint to align the markers. Align the markers
near to where you aligned them in step 4, but slightly on the opposite
side from where they ended up when you tested them. Reset only the
encoders of the mis-aligned joints. Repeat the test.
Summary of Contents for F3
Page 1: ...F3 Robot Arm for C500C Controller User Guide UMI F3 310 ...
Page 3: ...99 05 31 iii ...
Page 4: ...iv 99 05 31 ...
Page 8: ...viii 99 05 31 ...
Page 18: ...4 F3 Robot Arm User Guide 99 05 31 ...
Page 44: ...30 F3 Robot Arm User Guide 99 05 31 ...
Page 52: ...38 F3 Robot Arm User Guide 99 05 31 Reach of F3 with servo gripper dimensions in inches mm ...
Page 70: ...56 F3 Robot Arm User Guide 99 05 31 ...
Page 92: ...78 F3 Robot Arm User Guide 99 05 31 ...
Page 98: ...84 F3 Robot Arm User Guide 99 05 31 ...
Page 112: ...98 F3 Robot Arm User Guide 99 05 31 ...
Page 114: ...100 F3 Robot Arm User Guide 99 05 31 ...
Page 116: ...102 F3 Robot Arm User Guide 99 05 31 ...
Page 126: ...112 99 05 31 ...