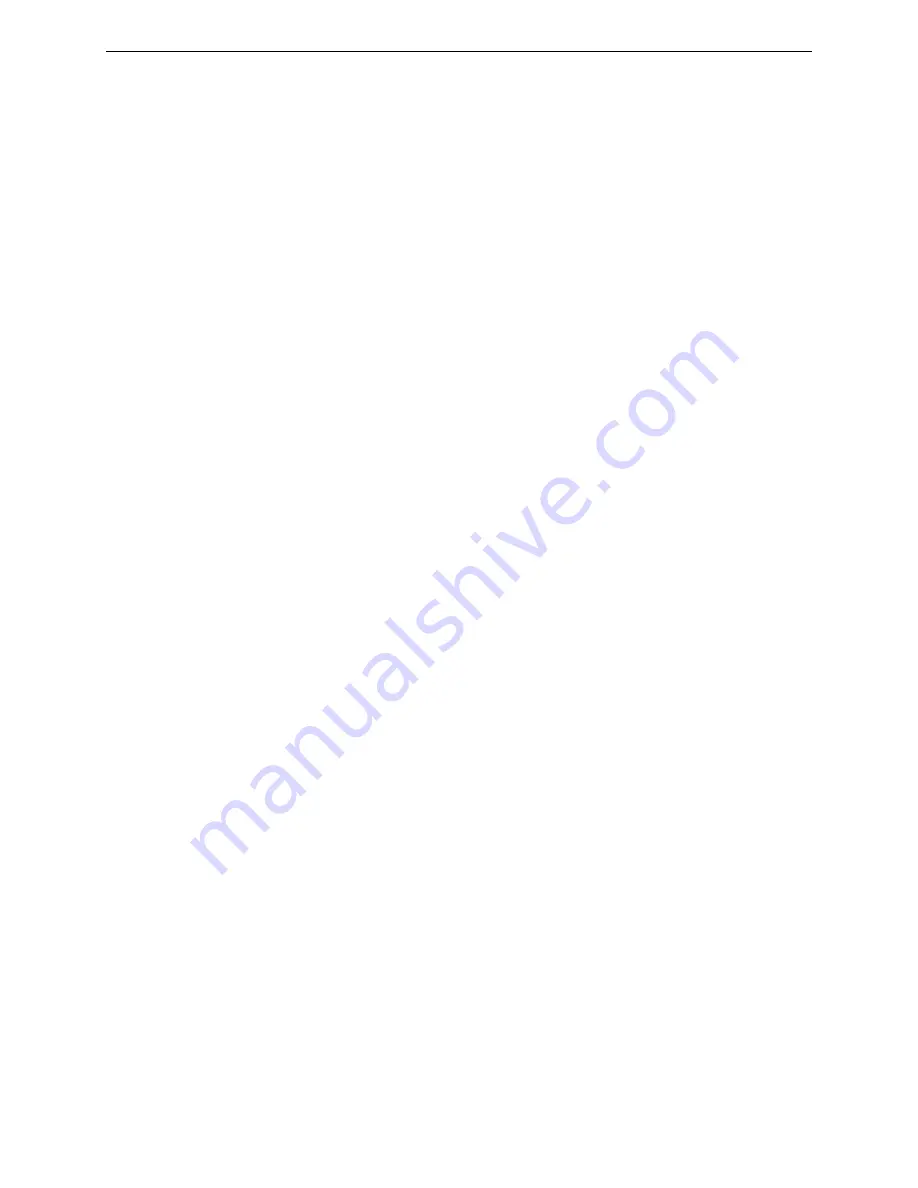
99-05-31
xiii
Important Tips
Work Safely
Follow all safety information.
Work Safely in the Workspace
Always stay within reach of an e-stop button when you are in the arm’s
workspace. There is an e-stop on the teach pendant.
Back-up Calibration
Keep the calibration file that was delivered on the calibration diskette. Do
not lose it.
If you re-calibrate the robot, update the backup file.
Maintain the Robot
Keep to the recommended inspection and maintenance schedule. Keep a log
of all maintenance and service activities as well as the number of working
hours.
For maintenance, use the same chain lubricant that was applied at CRS
during initial assembly.
Replace the encoder backup batteries 12 months after receiving your robot.
Use only nickel-metal-hydride batteries. Contact CRS Customer Support for
more detailed specifications or purchase of replacement units.
Lift the Robot Carefully
Do not lift the robot without assistance of a crane or other persons.
Design the Workcell
Always design your workcell to be serviceable.
1.
Teach at least one robot location where it is easy to access the arm and
the drawer at the base of the arm. Teach at least one robot location that
gives ample room for mounting and dismounting the robot.
2.
Install the controller so that it can be easily relocated to an open area for
service.
3.
Provide adequate clearance at the base of the robot and at the rear of the
controller for the umbilical cable.
Get Trained
Attend an F3 training course.
Use Correct Tool Frame of Reference
The tool frame of reference on the F3 is defined according to the ISO
convention. This is different from earlier models of CRS robots.
Summary of Contents for F3
Page 1: ...F3 Robot Arm for C500C Controller User Guide UMI F3 310 ...
Page 3: ...99 05 31 iii ...
Page 4: ...iv 99 05 31 ...
Page 8: ...viii 99 05 31 ...
Page 18: ...4 F3 Robot Arm User Guide 99 05 31 ...
Page 44: ...30 F3 Robot Arm User Guide 99 05 31 ...
Page 52: ...38 F3 Robot Arm User Guide 99 05 31 Reach of F3 with servo gripper dimensions in inches mm ...
Page 70: ...56 F3 Robot Arm User Guide 99 05 31 ...
Page 92: ...78 F3 Robot Arm User Guide 99 05 31 ...
Page 98: ...84 F3 Robot Arm User Guide 99 05 31 ...
Page 112: ...98 F3 Robot Arm User Guide 99 05 31 ...
Page 114: ...100 F3 Robot Arm User Guide 99 05 31 ...
Page 116: ...102 F3 Robot Arm User Guide 99 05 31 ...
Page 126: ...112 99 05 31 ...