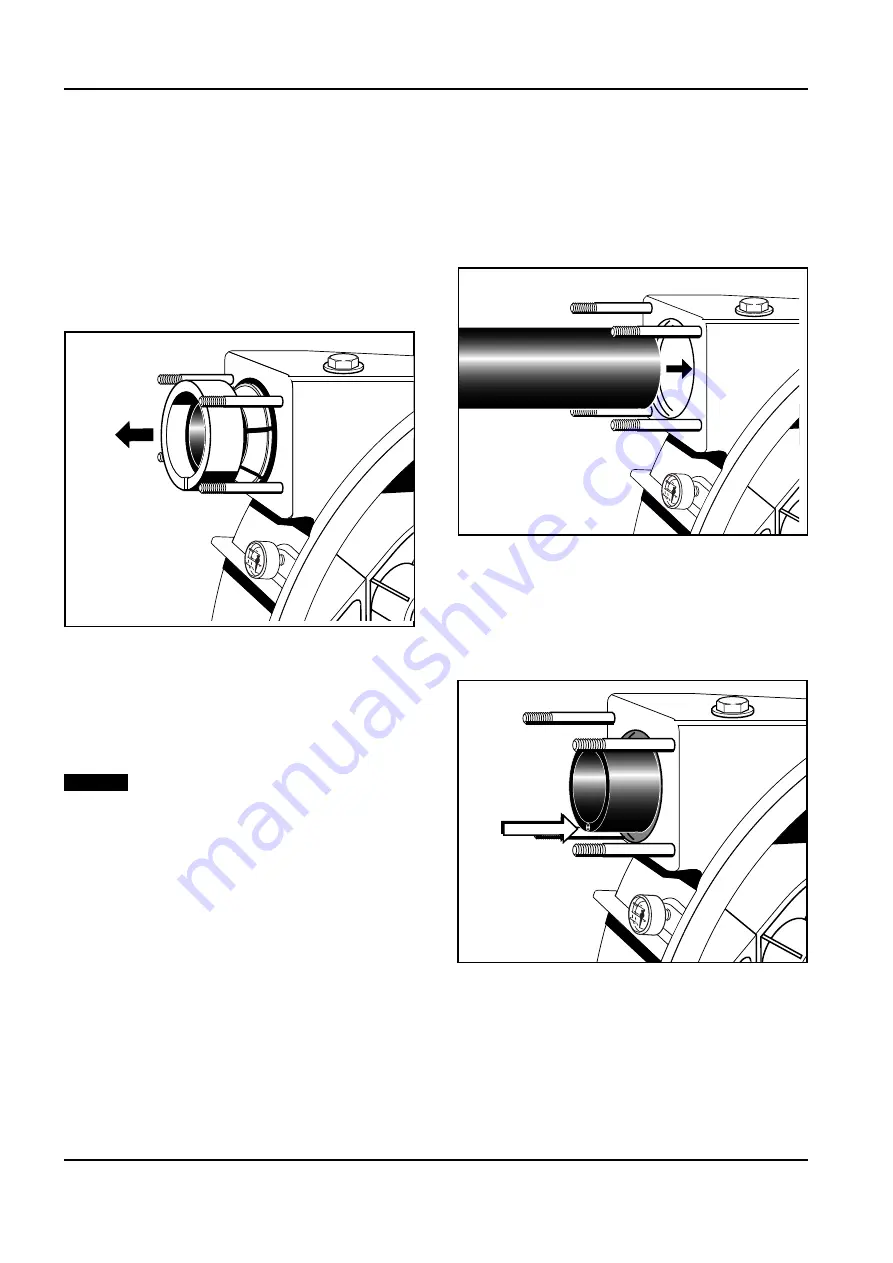
32
Peristaltic Pumps Series IP 100-800
8. Switch the pump on for a moment, so that
the pumping hose is pushed out of the pump
housing (keep on pulling the pumping house
out of the housing).
Perform this process with utmost
attention. In case of a failure switch
off the pump immediately.
9. Remove pump cover and O-ring again and
inspect the inside of the housing.
5.8.2 Inspecting the inside of the pump
Before installing a new pumping hose clean the
inside of the pump housing and check for
damage.
Replace damaged parts.
6. Then remove the ventilation pipes from
suction and pressure side (Fig. 35). Remove
retaining ring, segment ring, step ring and O-
ring from the pumping hose (Fig. 36).
7. Attach pump cover with O-ring and tighten
slightly with nuts.
Fig. 36
5.8.3 Installing the new pumping hose
1. Attach the pump cover with a new O-ring
and tighten the nuts.
Fig. 37
Slightly lubricate one end of the pumping hose
with lubricating fluid and push it into the suction
port of the pump (Fig. 37), until the hose stops.
Fig. 39
Make sure that the small hose bore is at the
inside, near the rotor (Fig. 39).
3. Switch the pump on for a short moment, so
that the rotor can pull the pumping hose step
by step into the pump housing, keep pushing
to assist.
Attention!
Summary of Contents for ELRO IP 100
Page 4: ...4 ...