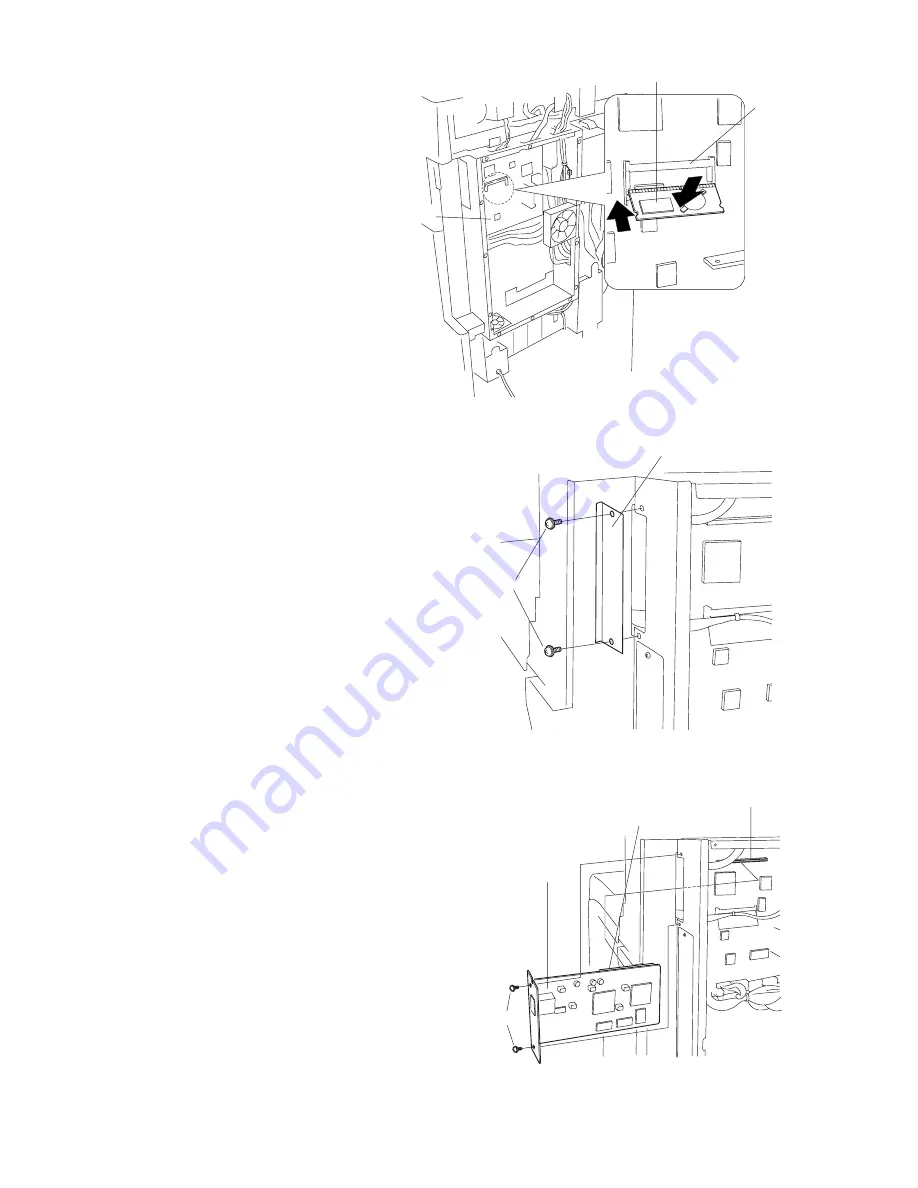
2DF
1-3-46
4. Insert the RTC board at an angle into the
RTC board slot on the main PCB.
5. Push the free end of the RTC board down
toward the fax board.
6. Remove 2 screws, and take off the cover.
7. Firmly push connector CN1 on the scanner
board all the way into connector CN50 on the
main PCB.
8. Fasten the scanner board with 2 screws.
Figure 1-3-98
Figure 1-3-96
Figure 1-3-97
RTC board slot
RTC board
Main PCB
Cover
Screws
Connector CN1
Connector CN50
Screws
Scanner board
Summary of Contents for Ri 2530
Page 59: ...2DF 1 3 39 This page is intentionally left blank...
Page 124: ...1 4 37 2DF This page is intentionally left blank...
Page 130: ...1 4 41 2DF This page is intentionally left blank...
Page 138: ...1 4 47 2DF This page is intentionally left blank...
Page 151: ...1 4 56 2DF This page is intentionally left blank...
Page 326: ...AD 63...
Page 329: ...3CX 1 1 2 1 1 2 Part names Figure 1 1 1 Duplex unit...
Page 330: ...3CX 1 1 3 1 1 3 Machine cross section Figure 1 1 2 Paper path Duplex unit...
Page 346: ...DF 78...
Page 349: ...3B5 1 1 2 1 1 2 Part names Figure 1 1 1 1 Intermediate tray 2 JAM release lever 3 Eject tray...
Page 383: ...J 1402...
Page 386: ...3B6 1 1 2 1 1 2 Part names Figure 1 1 1 1 Job separator tray 2 LED...
Page 387: ...3B6 1 1 3 1 1 3 Machine cross section Figure 1 1 2 Paper path...
Page 388: ...3B6 1 1 4 1 1 4 Drive system Figure 1 1 3 1 Gear 20 2 Gear 28 3 Gear 28 4 Eject roller gear...
Page 399: ...PF 70...
Page 401: ...1 1 2 3CC 2 4 Appendixes Timing chart No 1 2 4 1 Timing chart No 2 2 4 2 Wiring diagram 2 4 3...
Page 403: ...3CC 1 1 2 1 1 2 Parts names 1 Upper drawer 2 Lower drawer 3 Desk left cover Figure 1 1 1 3 1 2...
Page 404: ...3CC 1 1 3 1 1 3 Machine cross section Paper path Figure 1 1 2 Machine cross section...
Page 436: ...RA 1...
Page 438: ...3CP 1 1 1 1 1 1 Part names Figure 1 1 1 Switchback unit Switchback unit open close lever...
Page 439: ...3CP 1 1 2 1 1 2 Machine cross section Figure 1 1 2 Paper path Switchback unit...
Page 456: ...PF 75...
Page 458: ...1 1 2 5FF 2 4 Appendixes Timing chart No 1 2 4 1 Timing chart No 2 2 4 2 Wiring diagram 2 4 3...
Page 461: ...5FF 1 1 3 1 1 3 Machine cross section Paper path Figure 1 1 3 Machine cross section...
Page 499: ...Fax System C...
Page 501: ...1 1 2 3CM...
Page 509: ...3CM 1 1 8...
Page 553: ...3CM 1 3 40...
Page 565: ...3CM 1 5 2...
Page 570: ...3CM 2 1 2...
Page 581: ...Fax System F...