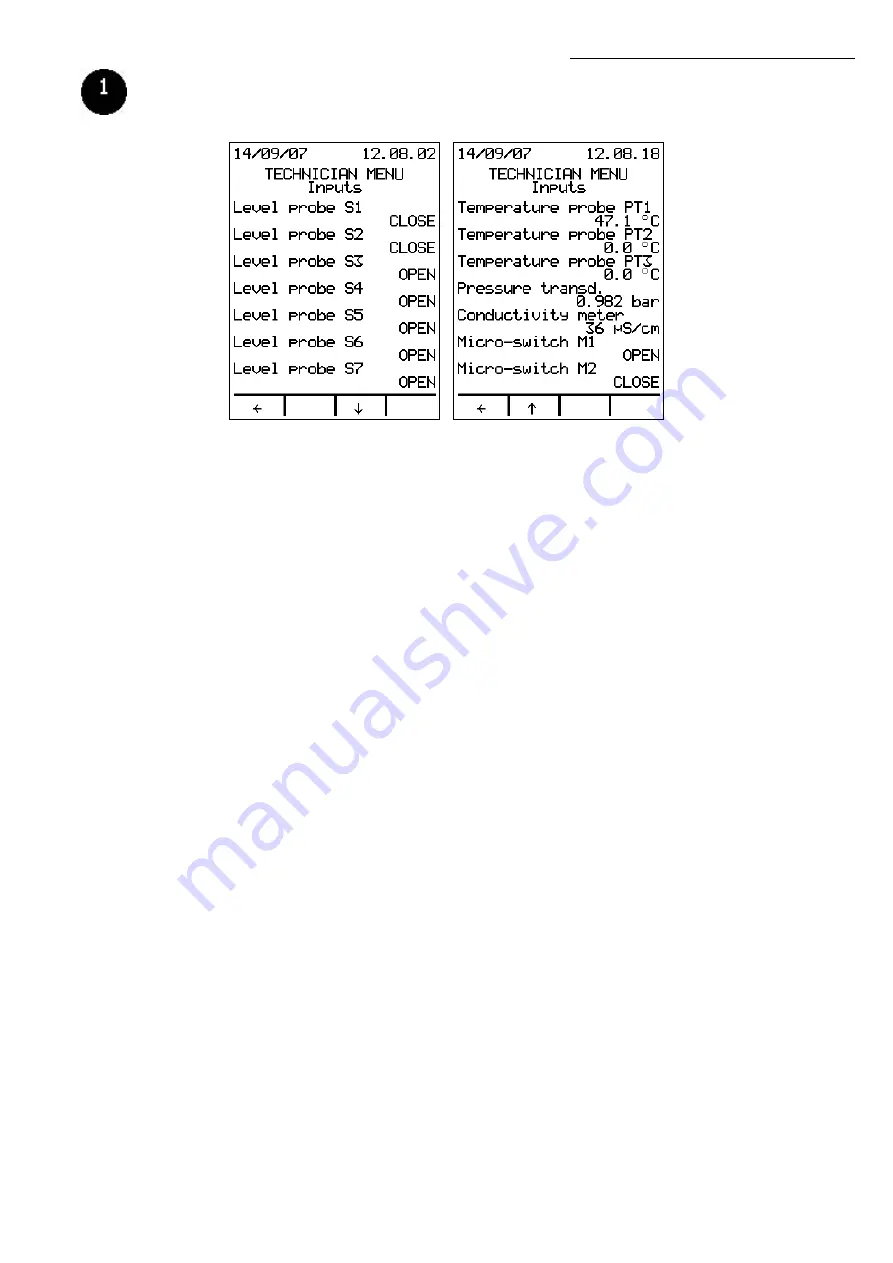
13
Inputs
The status of the steriliser inputs can be displayed:
•
S1 is the
clean water tank
10
safety probe
•
S2 is the
clean water tank
10
minimum level probe
•
S3 is the
clean water tank
10
maximum level probe
•
S4 is the
waste water recovery tank
11
maximum level probe
(not used in
6/18 S Dynamica models)
•
S5 is the
chamber
09
level probe for models 18/24 S Dynamica - S - B – BHD
(not used in 6 S Dynamica model)
•
S6 is not used
•
S7 is not used
•
PT1 is the
temperature probe
39
in
chamber
09
•
PT2 is not used
•
PT3 is not used
•
Pressure transducer
38
•
Conductivity meter (optional; standard on BHD models)
•
Micro-switch M1
36A
: door locked
•
Micro-switch M2
36B:
door pre-lock
Use the
↑↓
arrows to scroll the list and press to go back to the Technician Menu.
Technician Menu
Technician Menu
Summary of Contents for STERILCLAVE 18 B
Page 2: ...2...
Page 6: ...6 Graphical reference representation Model 6 S Dynamica Contents...
Page 7: ...7 Graphical reference representation Model 18 Contents...
Page 8: ...8 Graphical reference representation Model 24 Contents...
Page 9: ...9 Graphical reference representation of common components 40 Contents...
Page 10: ...10...
Page 63: ...63 Diagrams and wirings...
Page 75: ...75...