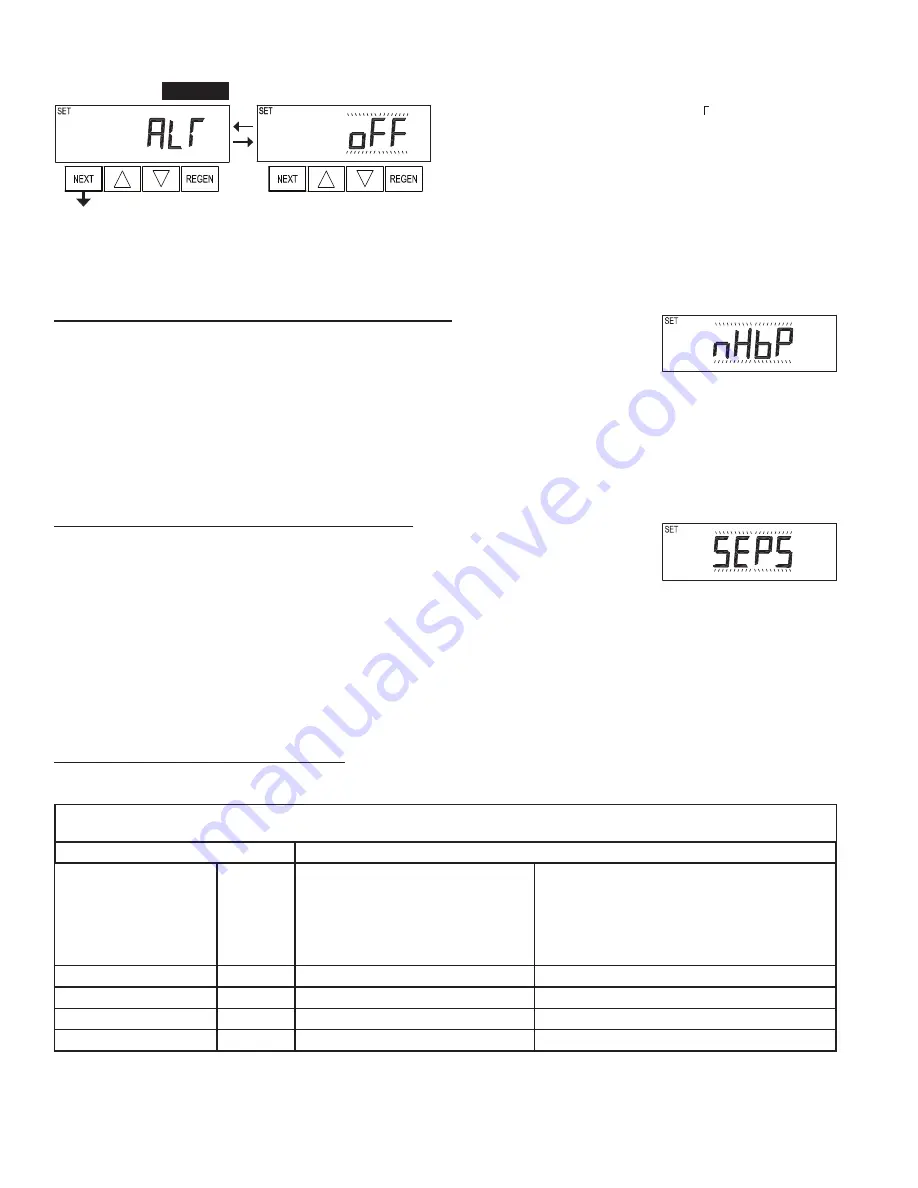
Page 8
EI
Man
u al
Step 5CS –
This display will not appear if 1.0
was selected in Step
2CS. Allows selection of one of the following using
▲
or
▼
:
• the Control Valve to have no hard water bypass;
• the Control Valve to act as an alternator;
• the Control Valve to have a separate source during the regeneration
cycle; or
• the Control Valve to operate with the System Controller.
Select OFF when none of these features are used.
Only use Clack No Hard Water Bypass Valves or Clack Motorized Alternating Valves (MAV) with these selections. Clack No Hard Water
Bypass Valves (1” or 1.25” V3070FF or V3070FM) are not designed to be used with the alternator or separate source functions.
Selecting the Control Valve to act as an alternator:
618.3 and higher = Use 3-wire Interconnect Cables for all communication between units.
616.6 and lower = Use 2-wire Interconnect Cables for twin alternators with independent
fl
ow meters.
Con
fi
guring the Control Valve for No Hard Water Bypass Operation:
Select nHbP for control operation. For no hard water bypass operation the three wire communication cable
is not used.
Selection requires that a connection to MAV or a Clack No Hard Water Bypass Valve is made to the two
pin connector labeled MAV located on the printed circuit board. If using a MAV, the A port of the MAV
must be plugged and the valve outlet connected to the B port. When set to nHbP the MAV will be driven
closed before the
fi
rst regeneration cycle that is not FILL or SOFTENING or FILTERING, and be driven
open after the last regeneration cycle that is not FILL.
NOTE: If the control valve enters into an error state during regeneration mode, the no hard water bypass
valve will return to the open Position, if not already there.
Con
fi
guring the Control Valve for Separate Source Operation:
Select SEPS for control operation. For separate source operation the three wire communication cable is not
used.
Selection requires that a connection to a Clack Motorized Alternator Valve (MAV) is made to the two pin
connector labeled MAV located on the printed circuit board. The C port of the MAV must be connected to
the valve inlet and the A port connected to the separate source used during regeneration. The B port must
be connected to the feed water supply.
When set to SEPS the MAV will be driven closed before the
fi
rst regeneration cycle, and be driven open
after the last regeneration cycle.
NOTE: If the control valve enters into an error state during regeneration mode, the MAV will return to the
open position, if not already there.
NOTE: If the control valve is in an error state during regeneration mode the MAV will close the B port and keep open the A port until the error is
corrected and reset.
Step 5CS
Prior to starting the programming steps, connect the communication cable to each control valve board’s three pin connector labeled
‘COMM CABLE’. Also connect the meter cord to either control valve to the three pin connector labeled ‘METER’.
Softener Valve Programming Steps
Con
fi
guration Settings
Step 5CS
Set to ALT A
Connect the outlet plumbing of ALT A
valve to the MAV’s A port and connect
the MAV’s two pin wire connector to the
two pin connector labeled “DRIVE” on
the ALT A valve
Set to ALT b
Connect the outlet plumbing of ALT b valve to the
MAV’s B port. No electrical connections are required
between the ALT b valve and the MAV.
Softener System Setup
Step 10S
Set System Capacity
Set System Capacity
Softener System Setup
Step 11S
Set to ‘AUTO’
Set to ‘AUTO’
Softener System Setup
Step 12S
Set regeneration time option to ‘on 0’.
Set regeneration time option to ‘on 0’.
Installer Display Settings
Step 4I
Set Day Override to “oFF”
Set Day Override to “oFF”
If set up for a
fi
lter, in Step 5F set Volume Capacity in M
3
; in Step 6F select Regeneration Time Option “on 0”; and in Step 4I select Day
Override “oFF”.
Summary of Contents for Water Specialist EI
Page 1: ...Water Specialist EI Control Valve Programming and Cover Drawing Manual...
Page 2: ...Page 2 EI Manual...
Page 20: ...Page 20 EI Manual...
Page 21: ...EI Manual Page 21...
Page 22: ...Page 22 EI Manual...
Page 24: ...Page 24 EI Manual Form No V3435EI 8 24 2017 U S Patents 6 402 944 6 444 127 6 776 901...