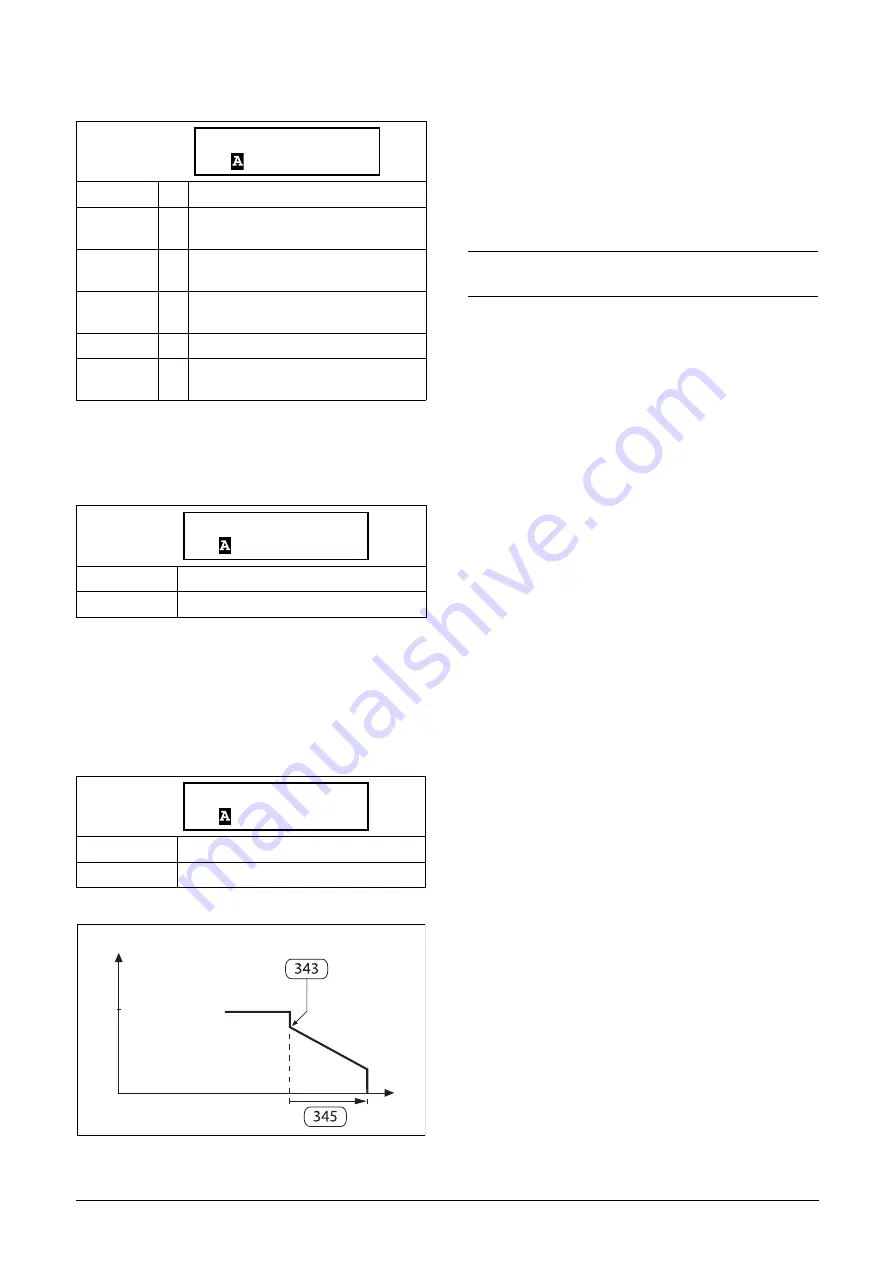
CG Drives & Automation, 01-5980-01r2
Functionality
95
End Torque at Stop [342]
This menu sets the end torque value when one of the torque
control functions is chosen in menu [341].
Step Down Voltage at Stop [343]
This setting is available when “voltage control” is chosen in
[341]. The switch-on period will step down to an
intermediate value, from where it will follow a linear voltage
ramp down to the minimum allowed switch-on period. The
duration of the ramp is set in “Stop Time” [345].
Fig. 58 Step down voltage at stop.
Braking Method [344]
This menu is available when “Brake” is chosen in [341].
However, before applying a high braking torque it should be
checked whether the motor, the gear or belt drive, and the
load can withstand the high mechanical forces. To avoid
harmful vibrations, it is generally recommended to select the
lowest braking torque possible that still fulfils the demands
for a short braking time.
Dynamic Vector Brake
With dynamic vector brake, the braking torque applied to
the motor will increase with decreasing speed. Dynamic
vector brake can be used for all loads not rotating too close to
synchronous speed when the motor voltage is switched off.
This is valid for most applications, as the load speed usually
decreases because of frictional losses in gears or belt drives
when the voltage is switched off. However, this method is less
suitable for loads with very high inertia, in which case the
reverse current brake is more efficient.
When the dynamic vector brake is used, no additional
connections or contactors are needed.
The actual speed is detected, and when this is above the limit
set in menu [349]the dynamic vector brake is executed. For
lower speeds the DC brake is activated.
Reverse Current Brake
This braking method is especially suitable for quickly
stopping heavy loads with high inertia. A very high braking
torque can be applied to the motor even close to synchronous
speed. The braking is accomplished by phase-reversal of the
current. To enable this, two external mains contactors are
needed which are controlled by the relay outputs of the
softstarter The connection is showed in Fig. 24, page 28.
During start and full voltage operation the first contactor
(K1) will be activated. For braking, K1 will be opened and
the second contactor (K2) will be activated to change the
phase sequence. For safety reasons it is possible to set a delay
time between these two signals in menu [346].
To activate the braking method, “Reverse Current Brake”
must also be selected in menu [344]. The actual speed is
detected, and the reverse current brake is active until the
speed is below the limit set in menu [349]. For lower speeds
the DC brake is activated.
DC brake (at low speed)
At low speed the DC brake mode is activated until the stop
time in [345] has elapsed. In DC-brake mode only two
phases (L2 and L3) are active.
The DC brake will automatically be deactivated when the
motor has stopped or when the stop time has expired.
Optionally an external rotation sensor can be connected via
Default:
4
Coast
Lin Torq Ctr
1
The motor torque is controlled according
to a linear ramp.
Sqr Torq Ctr 2
The motor torque is controlled according
to a square ramp.
Voltage Ctr
3
The motor voltage is controlled according
to a linear voltage ramp.
Coast
4
The motor coasts to a stop.
Brake
5
Braking method as activated in menu
[344].
Default:
0%
Range:
0 - 100% of T
n
Default:
100%
Range:
0 - 100% of U
n_mot
[221]
341 Stop Method
Stp
Coast
342 EndTorqueStp
Stp
0%
343 StepDwnVolt
Stp
100%
Voltage
Time
U
n_mot
Stop time
Note: It is the high braking torque that results in short
stop time, not the stop time set in menu [345].
Summary of Contents for emotron TSA Series
Page 1: ...Emotron TSA Softstarter Instruction manual English Valid from Software version 1 27...
Page 2: ......
Page 4: ......
Page 6: ...2 CG Drives Automation 01 5980 01r2...
Page 12: ...8 Introduction CG Drives Automation 01 5980 01r2...
Page 18: ...14 Mounting CG Drives Automation 01 5980 01r2...
Page 42: ...38 Application guidelines CG Drives Automation 01 5980 01r2...
Page 46: ...42 Getting started CG Drives Automation 01 5980 01r2...
Page 70: ...66 Main features CG Drives Automation 01 5980 01r2...
Page 142: ...138 Functionality CG Drives Automation 01 5980 01r2...
Page 158: ...154 Troubleshooting Diagnoses and Maintenance CG Drives Automation 01 5980 01r2...
Page 160: ...156 Options CG Drives Automation 01 5980 01r2...
Page 168: ...164 Technical data CG Drives Automation 01 5980 01r2...
Page 202: ...CG Drives Automation 01 5980 01r2 198...
Page 203: ......