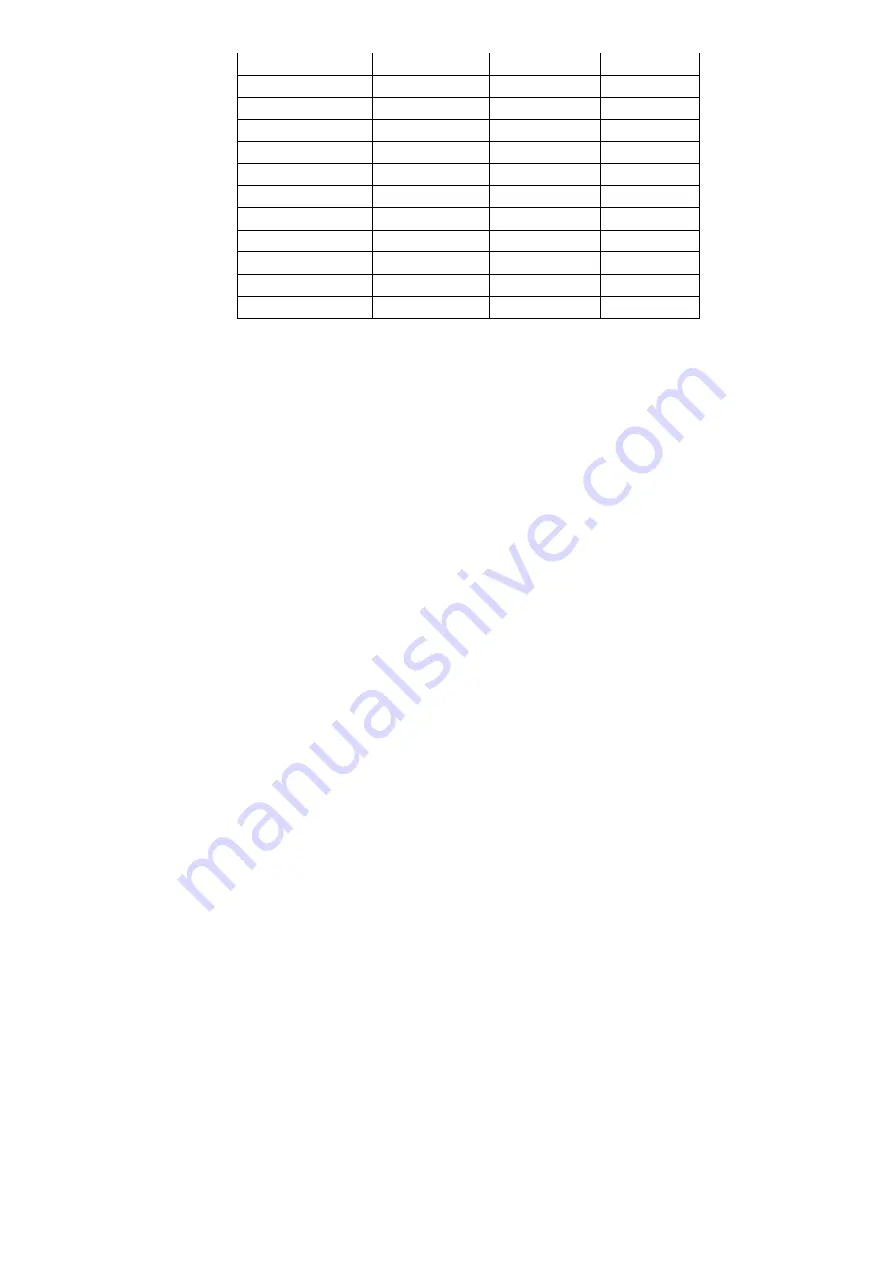
72
29.4
50.5
151.9
-
32.2
65.6
167
-
35
81.9
183.3
-
37.8
99.3
200.7
-
40.6
118.1
219.5
-
43.3
138.1
239.5
-
46.1
159.6
261
-
48.9
182.4
283.8
-
51.7
206.8
308.2
-
54.4
232.7
334.1
-
57.2
260.3
361.7
-
60
289.6
391
-
Table 17
– R1233zd(E) Pressure / Temperature
5.1.7 Standing Vacuum Test
When performing the standing vacuum test or chiller dehydration, use a manometer or a wet bulb indicator. Dial
gages cannot indicate the small amount of acceptable leakage during a short period of time.
1. Attach an absolute pressure manometer or wet bulb indicator to the chiller.
2. Evacuate the vessel to at least 0.06 kPa [abs], using a vacuum pump.
3. Shut off pump valve to hold the vacuum and record the manometer or wet bulb indicator reading.
4. If the pressure rise is less than 56 Pa within 8 hours, the chiller is sufficiently tight.
If the pressure rise exceeds above criteria, re-pressurize the vessel and conduct leak test and repair the leak
point.
5.1.8- Chiller dehydration
Dehydration is recommended if the chiller has been open for a considerable period of time, if the chiller is known
to contain moisture, or if there has been a complete loss of chiller holding charge or refrigerant pressure.
CAUTION: Do not start or megohm-test the compressor motor or any other pump motor, even for a rotation check,
if the chiller is under dehydration vacuum. Insulation breakdown and severe damage may result.
WARNING: Power to the motor and VFD must be disconnected by an isolation switch before placing the machine
under a vacuum. To be safe, isolate input power before evacuating the chiller if you are not sure if there are live
leads to the hermetic motor.
Dehydration can be done at room temperatures. Using a cold trap (
Fig. 41
) may substantially reduce the time
required to complete the dehydration and is recommended should the unit be exposed to liquid moisture. The
higher the room temperature, the faster dehydration takes place. At low room temperatures, a very deep vacuum
is required for boiling off any moisture. If the ambient temperatures are low, contact a qualified service
representative for the dehydration techniques required.
Summary of Contents for PIC 5+
Page 26: ...26 VFD not shown Fig 13 Sensors actuators location ...
Page 52: ...52 Fig 24 19DV control box ...
Page 53: ...53 1 Power supply 24V AC 2 LEN 3 CCN 4 Ethernet 5 USB Fig 25 19DV HMI box rear view ...
Page 54: ...54 Fig 26 19DV IOB1 wiring Fig 27 19DV IOB2 wiring ...
Page 57: ...57 ...
Page 113: ...113 APPENDIX A SmartView SCREEN AND MENU STRUCTURE ...
Page 114: ...114 Detailed menu description ...
Page 116: ...116 APPENDIX B MAINTENANCE SUMMARY AND LOGSHEETS Cont 19DV monthly Maintenance Log ...