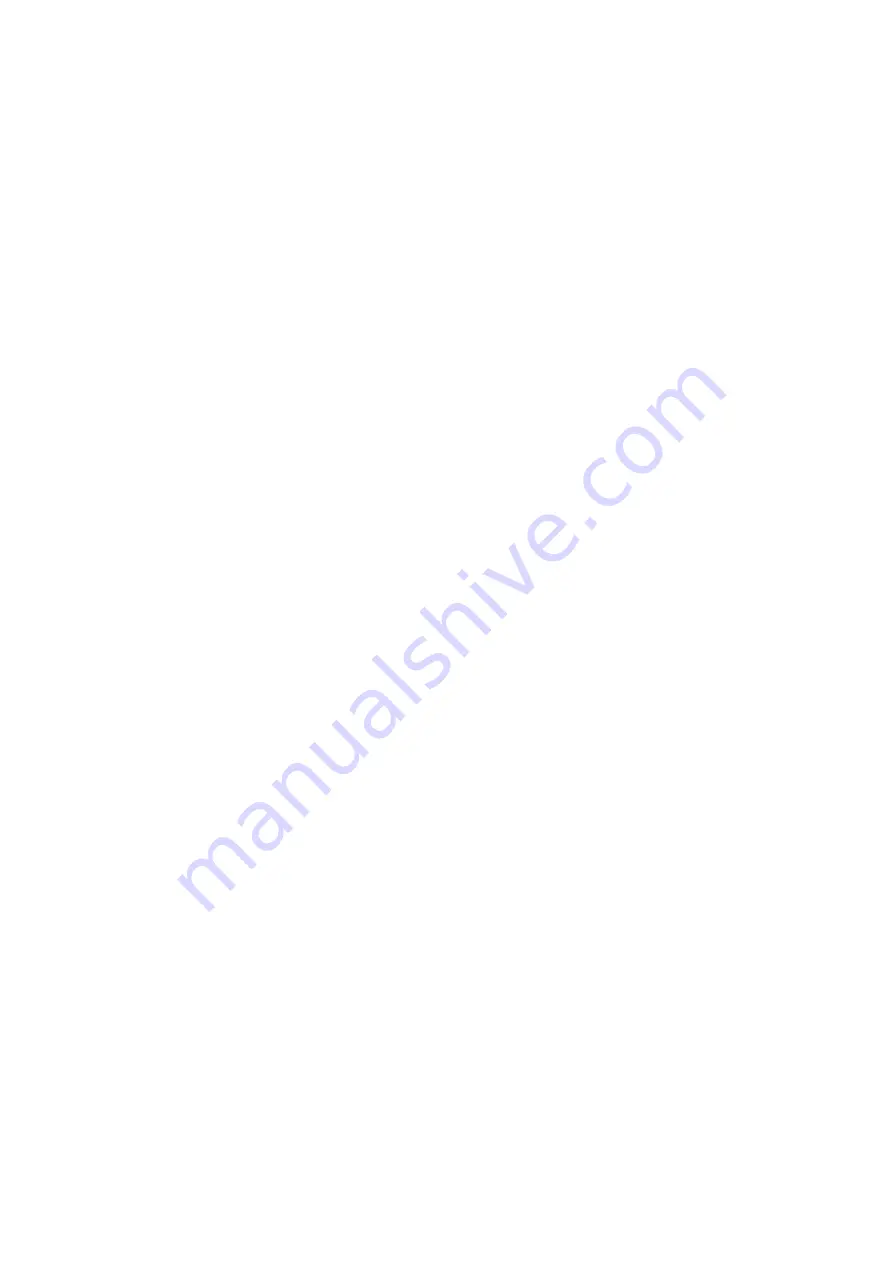
67
• 4 minutes have elapsed after initializing stop.
When any one of the above conditions is true, the shutdown sequence stops the compressor by deactivating the
compressor start relay. Then the guide vane shall be closed and stay at the fully closed position, the refrigerant
pump relay will be turned off after 120 seconds post lube, and the chilled water/brine pump and condenser water
pump will be shut down.
5. BEFORE INITIAL START-UP
5.1 - Necessary checks
5.1.1 - Job data required
Checks before system start-up: Before the start-up of the refrigeration system, the complete installation, including
the refrigeration system must be verified against the installation drawings, dimensional drawings, system piping
and instrumentation diagrams and the wiring diagrams.
During the installation test national regulations must be followed. If no national regulation exists, paragraph 9-5 of
standard EN 378-2 can be used as a guide.
External visual installation checks:
• Compare the complete installation with the refrigeration system and power circuit diagrams.
• Check that all components comply with the design specifications.
• Check that all safety documents and equipments required by the applicable European standard are present.
• Verify that all safety and environmental protection devices and arrangements are in place and comply with
the applicable European standard.
• Verify that all documents for pressure containers, certificates, name plates, files, instruction manuals required by
the applicable European standard are present.
• Verify the free passage of access and safety routes.
• Check that ventilation in the plant room is adequate.
• Check that refrigerant detectors are present.
• Verify that the instructions and directives to prevent the deliberate removal of refrigerant gases that are harmful
to the environment are being applied.
• Verify the installation of connections.
• Verify the supports and fixing elements (materials, routing and connection).
• Verify the quality of welds and other joints.
• Check the mechanical integrity of the machine.
• Check the protection against heat.
• Check the protection of moving parts.
• Verify the accessibility for maintenance or repair and to check the piping.
• Verify the status of the valves.
• Verify the quality of the thermal insulation and of the vapour barriers.
5.1.2 - Equipment required
• mechanic’s tools (refrigeration)
• digital volt-ohmmeter (DVM)
• true RMS (root mean square) digital multimeter with clamp-on current probe or true RMS digital clamp-on
ammeter rated for at least 480 vac
• electronic leak detector absolute pressure manometer or electronic micron gage (see Fig. 39)
• drum charging valve (unless refrigerant bottles already have charging valves)
• charging hose
• Refrigerant charge device
Summary of Contents for PIC 5+
Page 26: ...26 VFD not shown Fig 13 Sensors actuators location ...
Page 52: ...52 Fig 24 19DV control box ...
Page 53: ...53 1 Power supply 24V AC 2 LEN 3 CCN 4 Ethernet 5 USB Fig 25 19DV HMI box rear view ...
Page 54: ...54 Fig 26 19DV IOB1 wiring Fig 27 19DV IOB2 wiring ...
Page 57: ...57 ...
Page 113: ...113 APPENDIX A SmartView SCREEN AND MENU STRUCTURE ...
Page 114: ...114 Detailed menu description ...
Page 116: ...116 APPENDIX B MAINTENANCE SUMMARY AND LOGSHEETS Cont 19DV monthly Maintenance Log ...