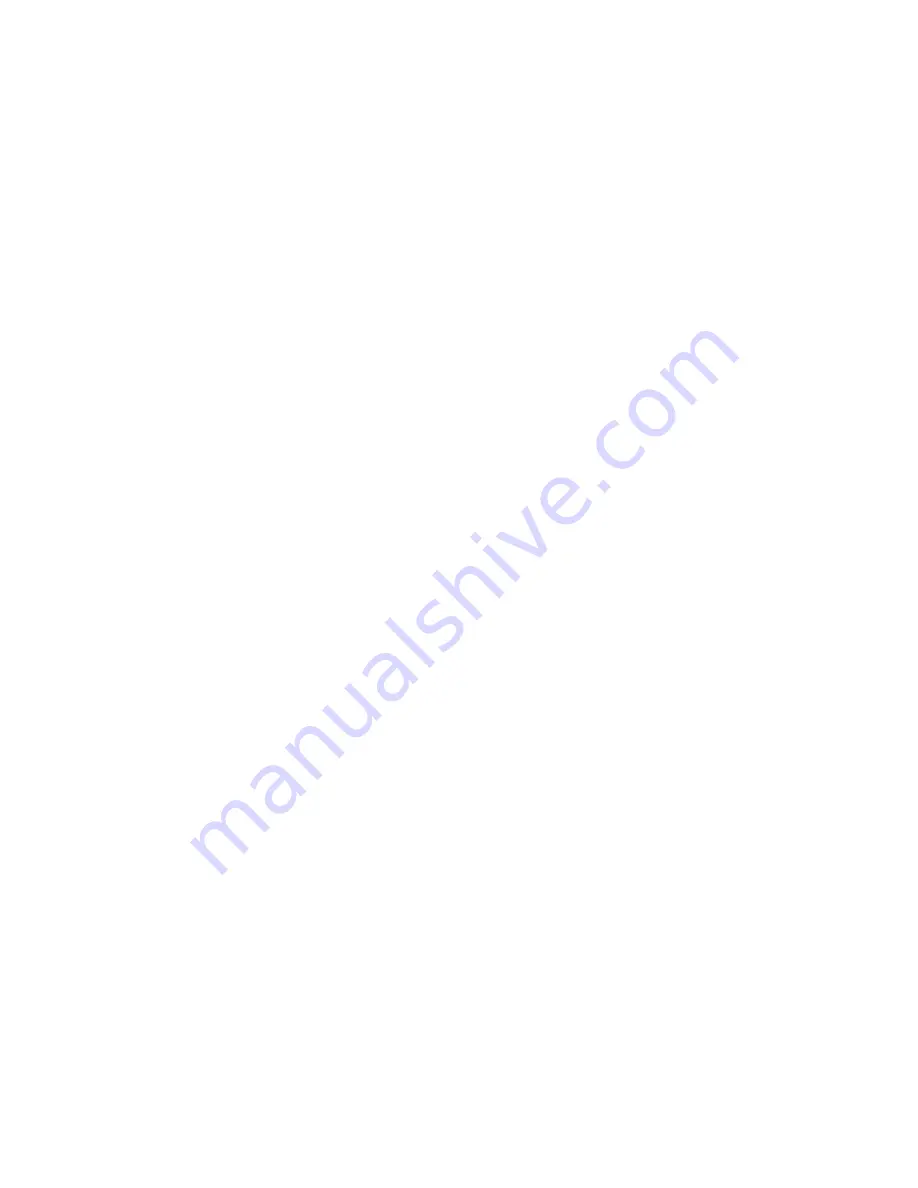
7–19
T-365
5. Install the evaporator fan assembly in reverse order of removal. Torque the four 1/4-20 clamp bolts to 0.81
mkg (70 inch-pounds). Connect the wiring connector.
6. Replace access the panel making sure that the panel does not leak. Make sure that the TIR locking device is
lockwired.
7.15 EVAPORATOR SECTION CLEANING
Containers and Container units that are exposed to certain fumigants may develop visible surface corrosion. This
corrosion will show up as a white powder found on the inside of the container and on the reefer unit evaporator sta-
tor and fan deck.
Analyses by Carrier Transicold environmental specialists have identified the white powder as consisting predomi-
nantly of aluminum oxide. Aluminum oxide is a coarse crystalline deposit most likely the result of surface corrosion
on the aluminum parts within the container. If left untreated over time, it may build up in thickness and eventually
flake as a lightweight white powder.
The surface corrosion of aluminum is brought about by exposure to chemicals such as sulfur dioxide and possibly
other fumigants that are commonly used for fumigation and protection of some perishable cargo such as grapes,
for example. Fumigation is the process by which a chemical is released into an enclosed area to eliminate infesta-
tions of insects, termites, rodents, weeds and soil-born disease.
Typically any aluminum oxide that becomes detached from evaporator fan stators will be blown into the wet evapo-
rator coil where it will be caught and then flushed out of the unit during routine defrost cycles.
However, it is still highly recommended that after carrying cargo subject to fumigation procedures, that the inside of
the unit be thoroughly cleansed prior to reuse.
Carrier Transicold has identified a fully biodegradable and environmentally safe alkaline cleaning agent (Tri-
Pow’r® HD) for the unit. This will assist in helping to remove the corrosive fumigation chemicals and dislodging of
the corrosive elements.
This cleaner is available from the Carrier Transicold Performance Parts Group (PPG) and can be ordered through
any of the PPG locations; Part Number NU4371-88.
As a general safety precaution, before using this product, refer to and retain the Material Safety Data (MSDS)
sheet. This document can be found at:
www.nucalgon.com/products/coil_cleaners_tripower.htm
Prior to Cleaning:
• Always wear goggles, gloves and work boots.
• Avoid contact with skin and clothing, and avoid breathing mists.
• When mixing, add water to the sprayer first, then the cleaner.
• ALWAYS provide for proper ventilation when cleaning indoor evaporator coils (rear doors must be open).
• Be aware of surroundings - food, plants, etc., and the potential for human exposure.
• Always read directions and follow recommended dilution ratios. More is not always better. Using non-diluted
cleaner is not recommended.
Cleaning Procedure:
1. Remove the upper evaporator access panel inside of the unit.
2. Spray the surface with water before applying the cleaning solution. This helps the cleaner work better.
3. Liberally apply the prepared cleaner solution (5 parts water and 1 part cleaner).
4. Allow the cleaner to soak in for 5 to 7 minutes.
5. Assess area for rinsing. Follow all local regulations regarding disposal of waste water.
6. Thoroughly rinse the cleaner and surrounding area, floor, etc. When rinsing where heavy foaming solution is
present, it is very important to take the time to thoroughly rinse the equipment and surroundings.
7. Always rinse the empty coil cleaner bottle, cap tightly and dispose of properly.
Summary of Contents for 69NT40-561-300
Page 2: ......
Page 4: ......
Page 10: ......
Page 14: ......
Page 22: ......
Page 34: ......
Page 108: ......
Page 116: ......
Page 164: ...T 365 8 2 Figure 8 2 Unit Wiring Diagram Based on Drawing 62ï11755 ...
Page 165: ...8 3 T 365 Figure 8 3 Wiring Diagram Based on Drawing 62ï11755 ...
Page 166: ...T 365 8 4 Figure 8 4 Wiring Diagram Based on Drawing 62ï11755 ...
Page 168: ......
Page 172: ......
Page 173: ......