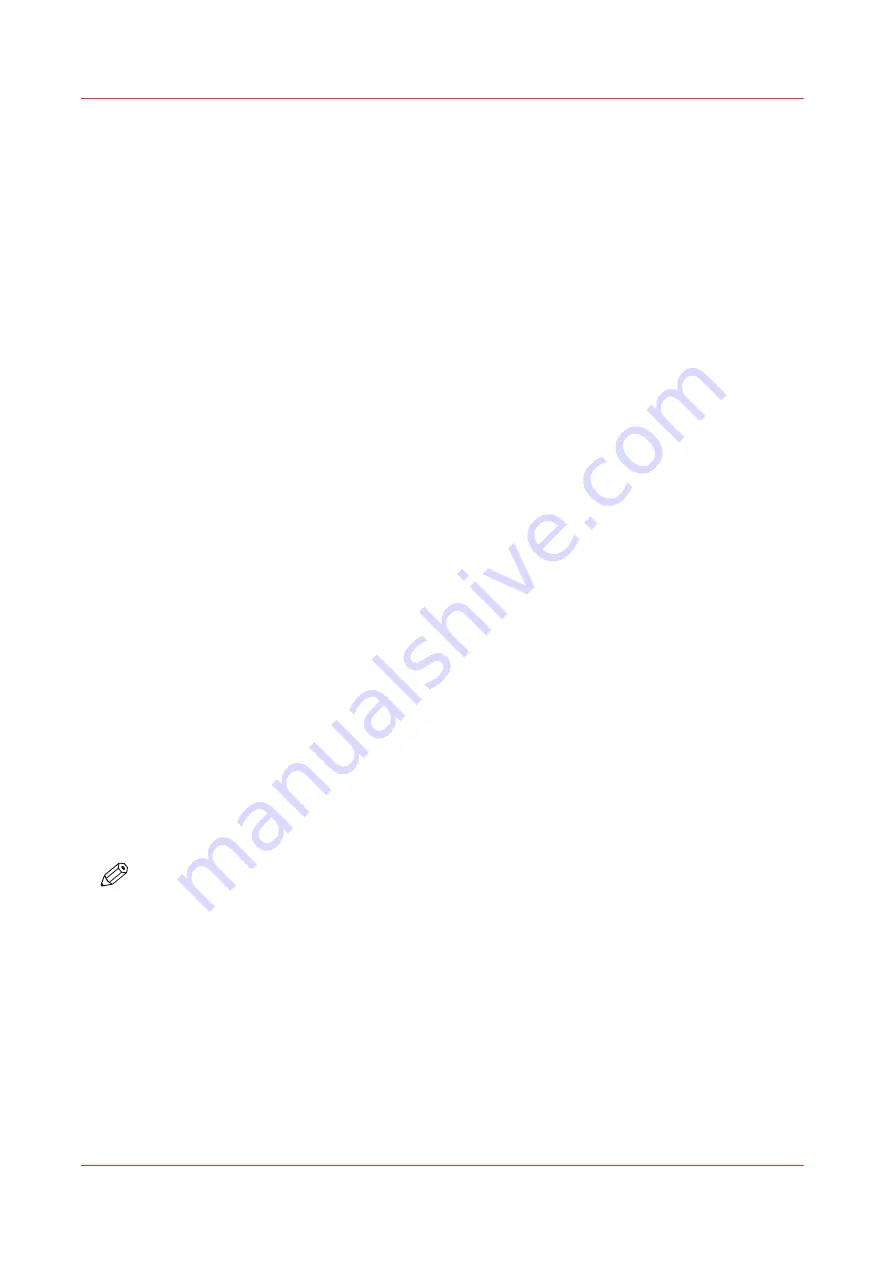
Batch Mode Printing
Introduction
Batch mode printing is available for streamlining multi-layered jobs for specialty applications or
facilitating set collation of multiple images on one piece of media. Individual print jobs are sent
from the RIP to the printer, and then combined on the printer to create a batch job for flatbed
printing. There are two types of batch mode jobs: Composite and Collated.
Composite
All images are printed on a single piece of media without interruption. Composite batch mode
can be used if you want to print more than the three layers allowed in the ONYX software and/or
mix print modes on the same piece of media. The first print job is printed, and then the carriage
moves to the start position for the second print job and prints it. This continues until the last print
job is printed and then the gantry moves to the home position to complete the batch job.
Collated
Collated batch mode prints a set of individual print jobs on separate pieces of media, and then
repeats the number of copies of the set, as required. The carriage moves to the park position
between each print job, the media is changed, the media thickness is confirmed and the
Start
button or
Start print
icon is pushed to continue printing the next image.
For example:
• If you want to collate 3 print jobs (J1,J2,J3) and print two 2 sets, the print order of the collated
batch job would be J1,J2,J3,J1,J2,J3.
• If you want to print 3 copies of the same job double-sided with different images front (F) and
back (B), the print order would be F,B,F,B,F,B.
Managing the Job and Batch Lists
Like in the Job lists, you can control the appearance of columns in the Batch job list: change the
order that columns appear, the width of each column, and also select the columns to appear on
the display.
1. Control the order of columns by dragging the column header to a different position.
2. Change the width of a column by clicking on the vertical line that separates column headers
and dragging to the left or right.
3. Chose the columns to display by right-clicking on a column header and then click on a column
name to add or remove it. Columns with a check mark will appear on the display and those
with no check will not be seen.
NOTE
Columns can be set back to their original appearance by right-clicking any column header
(name) and selecting
Reset to default
.
Procedure
1.
Send the individual jobs to be batched together from the RIP to the printer (or use existing Active
jobs).
Batch Mode Printing
72
Chapter 5 - How to Operate Your Océ Arizona Printer
Océ Arizona 1200 Series
Summary of Contents for Oce Arizona 1200 Series
Page 1: ...Operation guide Oc Arizona 1200 Series User Manual...
Page 6: ...Contents 6 Oc Arizona 1200 Series...
Page 7: ...Chapter 1 Introduction...
Page 11: ...Chapter 2 Product Compliance...
Page 14: ...Product Compliance 14 Chapter 2 Product Compliance Oc Arizona 1200 Series...
Page 15: ...Chapter 3 Safety Information...
Page 39: ...Chapter 4 How to Navigate the User Interface...
Page 60: ...Software Update Module 60 Chapter 4 How to Navigate the User Interface Oc Arizona 1200 Series...
Page 61: ...Chapter 5 How to Operate Your Oc Arizona Printer...
Page 82: ...Media Registration 82 Chapter 5 How to Operate Your Oc Arizona Printer Oc Arizona 1200 Series...
Page 83: ...Chapter 6 Operating the Oc Arizona 1200 XT...
Page 89: ...Chapter 7 Roll Media Option...
Page 113: ...Chapter 8 Static Suppression Option...
Page 117: ...Chapter 9 How to Manage a White Ink Workflow...
Page 161: ...Chapter 10 Ink System Management...
Page 165: ...Chapter 11 Troubleshooting...
Page 167: ...Chapter 12 Printer Maintenance...
Page 213: ...Chapter 13 Regulation Notices...
Page 219: ...Appendix A Application Information...
Page 225: ......