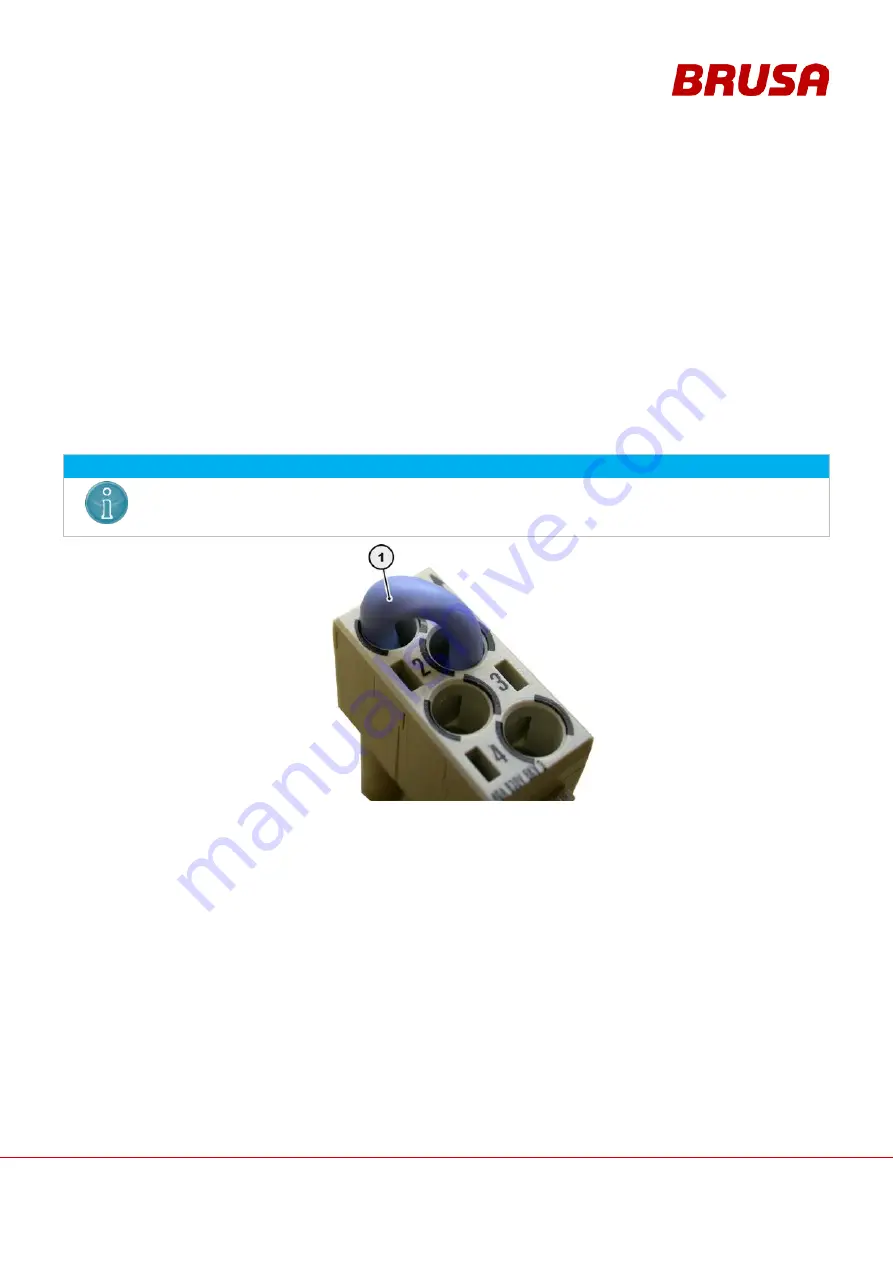
13
Technical information
and start-up
BSC624-12V-B
3.4
Safety installations / power limitations
3.4.1
Short-circuit protection
Since, due to its resonant clock topology, the transformer stage has a certain internal resistance, the device is
generally short-circuit proof. In the case of an external short-circuit (caused by the operator), this means that the
voltage breaks down while the signal
E_LV_UNDERVOL
is emitted.
In the
buck mode
, undervoltage is identified on the LV side in the case of a short-circuit.
In the
boost mode
, undervoltage is identified on the HV side in the case of a short-circuit.
Independent of the operating mode, undervoltage is also identified at the respective power input.
3.4.2
Interlock
INSTRUCTION
In order to guarantee the function of the interlock, for the cable bridge (1) in the HV power connector
it is not allowed to use another cable then the delivered. The cable has to prepare according the
manual chapter
9.1 Producing the cable glands for the HV power connector.
With this safety installation, the proper connection of the connectors on the device is monitored. The device
comprises an internal as well as an external interlock identification, which function independently of each other. An
interruption of the interlock circuit causes an immediate shut-down of the device. In order to use the external
interlock identification, the respective interlock pins must be connected at the control connector and the error
detection must be activated (for details, please refer to the
PARAM
manual). With a shut-down of the device, the
signal
CRE_INTERLOCK
is emitted.
The internal interlock identification monitors the HV power connector exclusively and is always active. The optional
external interlock identification is an interlock loop, which is ideally looped through all HV components in the
vehicle. The interlock signal must be generated and analysed respectively via an upstream control unit (e.g.
BRUSA PDU254).
Further information on the interlock can be found in chapter