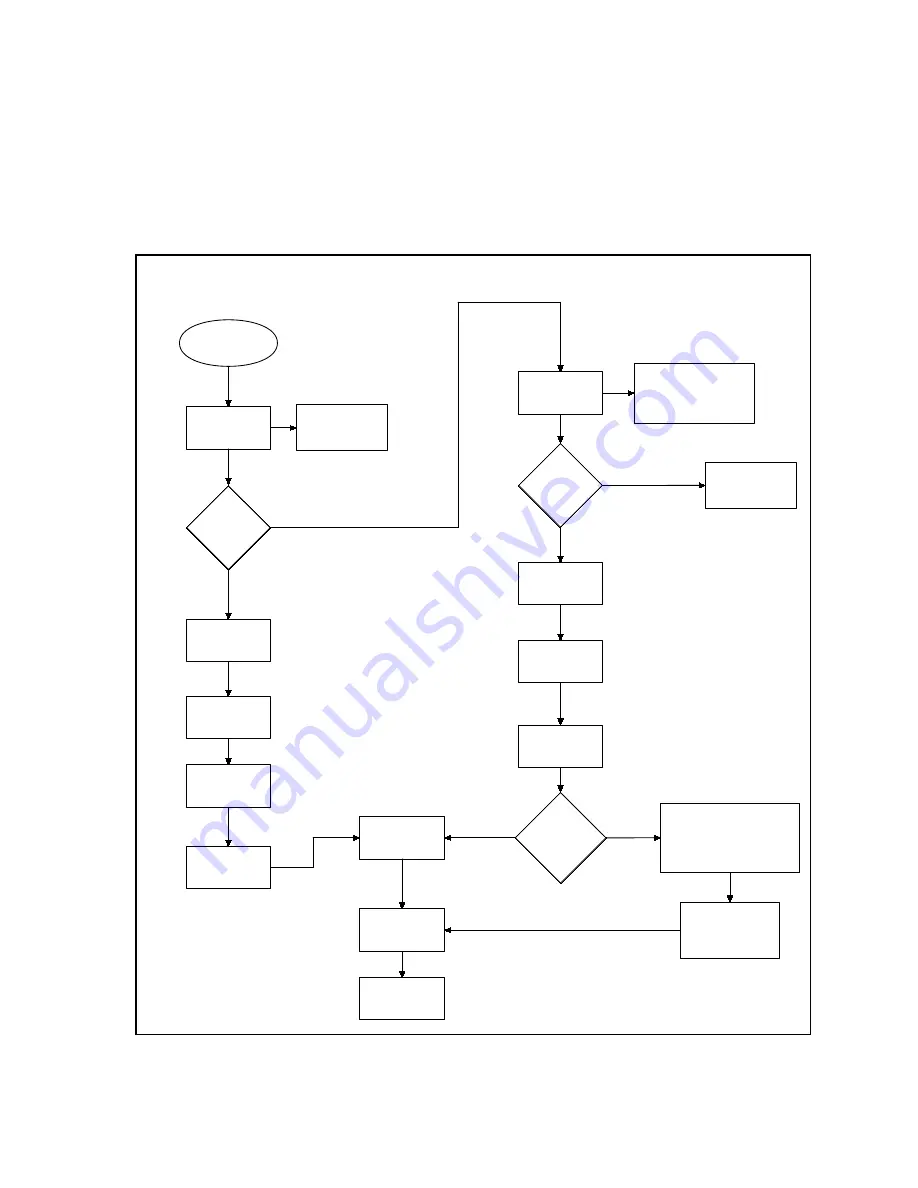
Section 3: Pinsetter Electronics
3-45
1. The pinsetter must be turned on, waiting for a ball.
2. The string wagon will be positioned at the front of the machine with ten pins sitting on the pin
deck.
3. The magnet in the cam control box will be positioned just above the home switch.
To begin a cycle a bowler must throw a ball. The pinsetter reacts as follows: Refer to
Figure 3-36.
Start
Pinsetter Ball
Detect
Allpinfall switches
in PMIs are "Open"
The Foul
Unit Triggered
YES
Was
there a
Strike?
Read PMI
Pinfall Switches
Gutter
Ball?
YES
NO
NO
Drive Motor
Turns "On"
No Changes
to the
Pinfall Switches
All of the
PinfallSwitches
"Closed"
Pinsetter CPU
Counts
1 Ball
Is there
a Foul?
NO
YES
Ready for next
ball after 5
seconds
Pins Up Switch
Closes
String Brake
Switch Closes
Energize Brake
Solenoids For Pins That
Were Knocked Over (To
Hold Those Pins Up)
Some of the
PinfallSwitches
"Closed"
Drive Motor
Turns "On"
Pins Up Switch
Closes
String Brake
Switch Closes
No Action
No Action
Scorer System
Scores Pinfall After
Trigg Time As Set In
The CMS System
Scorer System
Scores "Foul"
No Action
Home
Switch Closes
Drive Motor
Turns "Off"
All Pins Lower
To The Pindeck
Standing Pins
Lower To The
Pindeck
Figure 3-36. Pinsetter First Ball Cycles
Summary of Contents for StringPin
Page 1: ...Service Manual February 2019 55 900001 000 StringPin Pinsetter Ten Pin...
Page 6: ...6 StringPin Pinsetter Service Manual Intentionally Blank Page...
Page 35: ...Section 2 Overview 2 25 1 REAR ACCESS Figure 2 25 Machine Rear Access 1 REAR ACCESS...
Page 40: ...2 30 Section 2 Overview Intentionally Blank Page...
Page 102: ...4 16 Section 4 Adjustments Intentionally Blank Page...
Page 112: ...5 10 Section 5 Maintenance Service Intentionally Blank Page...
Page 126: ...7 8 Section 7 Cables Intentionally Blank Page...