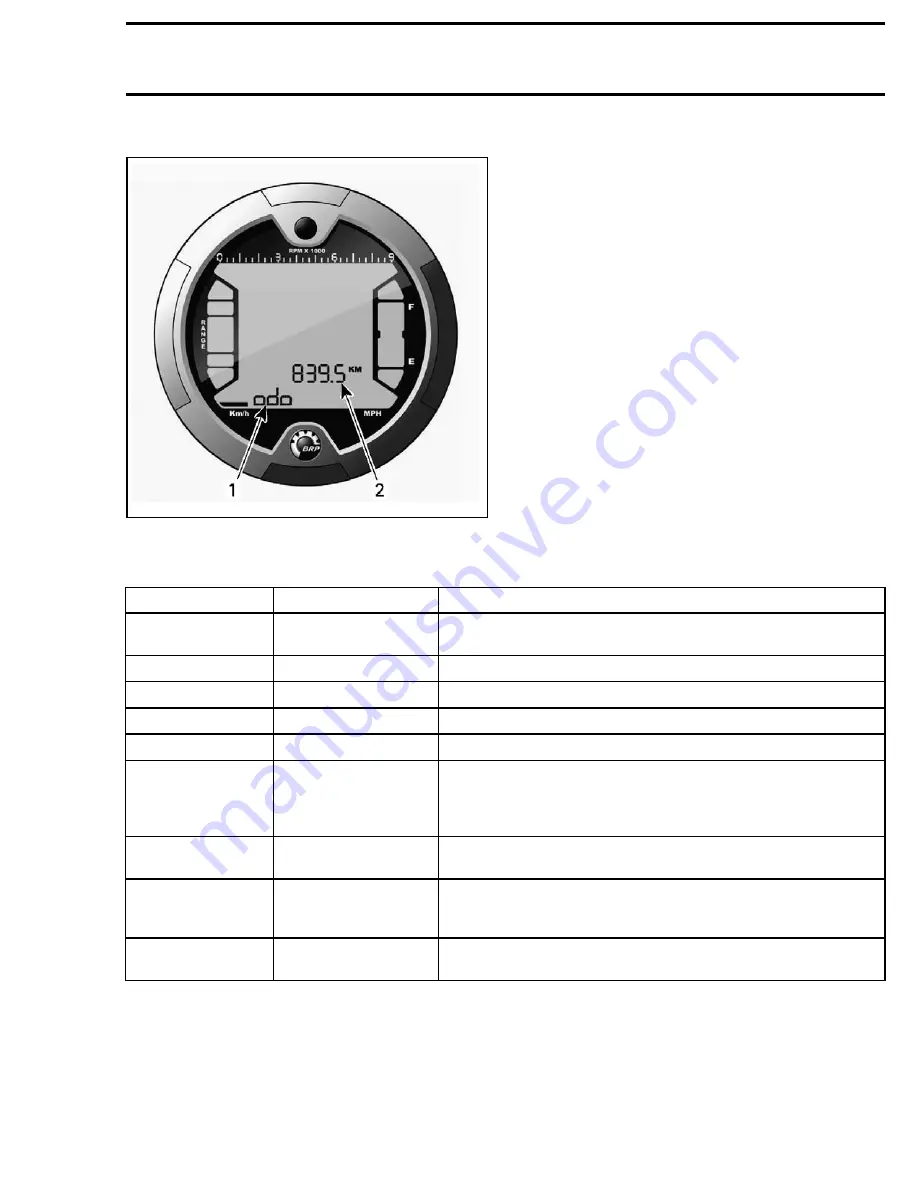
Section 06 ELECTRICAL SYSTEM
Subsection 04 (LIGHTS, GAUGE AND ACCESSORIES)
Display 3 (mode/message)
vmo2008-001-020_h
1. Display 3 (mode/message)
2. Display 2 (mode)
This display will show either an abbreviation of the
mode selected for viewing in display 2 or will com-
municate important messages to the operator if an
anomaly occurs.
Abbreviation Mode:
– ODO (odometer)
– TRIP (trip meter)
– TRIP TIME (hour meter)
– ENGINE HOURS (vehicle hour meter)
– RPM (engine revolutions per minute).
Message Mode:
MESSAGE
PILOT LIGHT(S) ON
DESCRIPTION
PARK BRAKE
Parking brake
Is displayed when parking brake is applied for more than
15 seconds (while riding).
LO BATT
Check engine
Low battery voltage, check battery voltage and charging system.
HI BATT
Check engine
High battery voltage, check battery voltage and charging system.
LOW OIL
(1)
Check engine
Engine low oil pressure, stop engine immediately.
HI TEMP
(2)
Check engine
Engine is overheating, stop engine immediately.
LIMP HOME
Check engine
Serious fault detected by the engine management that can
change the normal operation of the engine.
Check engine
indicator light will also blink, refer to
ENGINE MANAGEMENT
for
more details.
CHECK ENGINE
Check engine
Engine management fault. Check engine indicator light will also
be ON, refer to
ENGINE MANAGEMENT
for more details.
MAINTENANCE
SOON
Check engine
Periodic maintenance required.
NOTE:
To reset message, use B.U.D.S. software and click
Reset
Service
button in
Vehicle
tab.
NO ECM
COMMUNICATION
Check engine
Communication error between multifunction gauge and engine
control module (ECM). Refer to
ENGINE MANAGEMENT
.
CAUTION:
(1)
If the LOW OIL message and check engine light do not turn off right after engine
starting, stop engine. Check engine oil level. Refill if necessary. If the oil level is good, refer to the
LUBRICATION SYSTEM section.
CAUTION:
(2)
If the HIGH TEMP message and check engine light do not turn off right after engine
starting, stop engine. Refer to the COOLING SYSTEM section.
vmr2008-140
289
Summary of Contents for Outlander 400 EFI 2008
Page 2: ......
Page 433: ...2008 2015 OUTLANDER 400 EFI vdd2014 001 001 GENERAL SYSTEM...