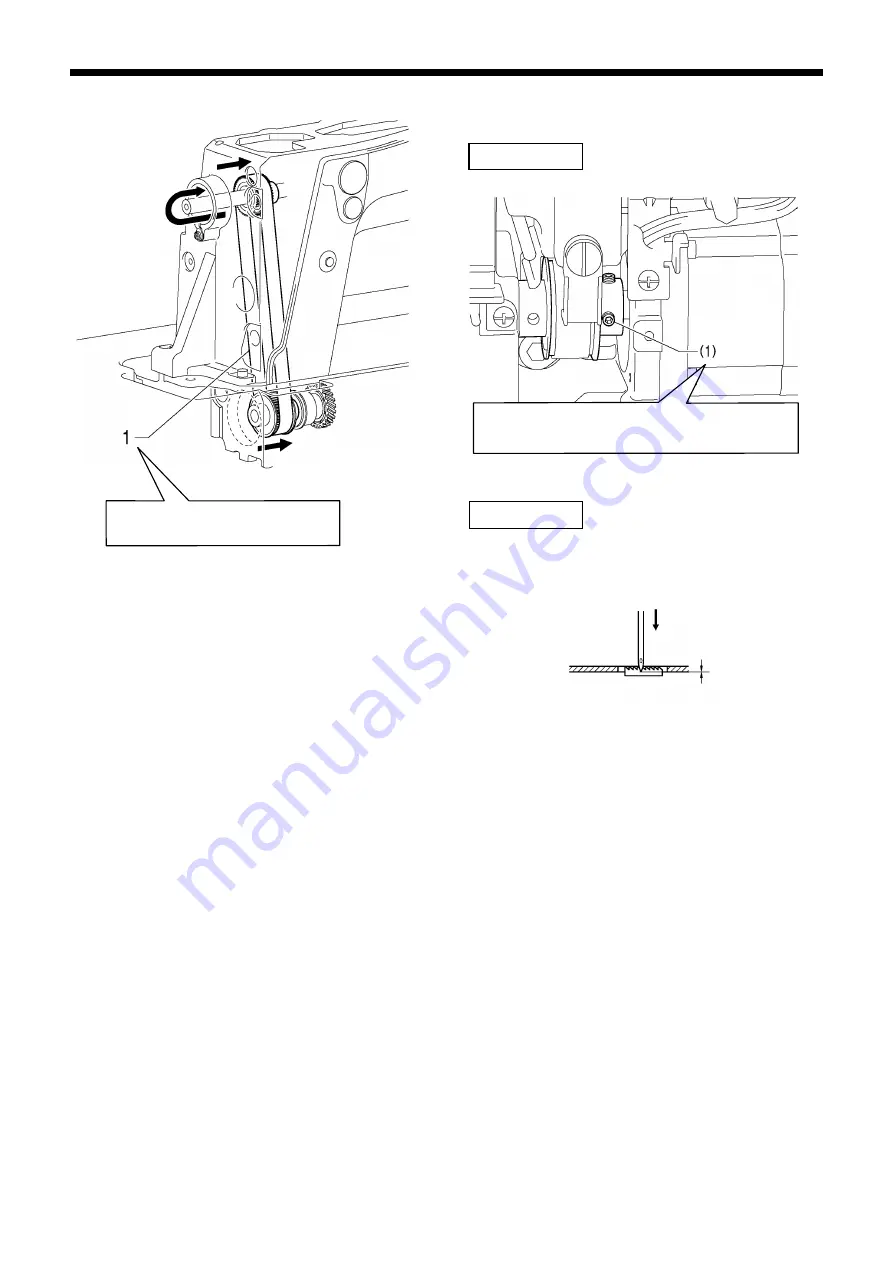
S-7300A
6. ASSEMBLY
81
6-4. Timing belt
Pass over the upper shaft and set
onto the pulley.
Lower shaft side
Upper shaft side
0 ~ 1mm
1148D
1. Timing belt
(1) Set screw
Set so that the first set screw (1) in the rotation
direction of timing pulley D is facing downward.
1149D
Set the needle tip and needle plate to
the positions shown in the illustration.
■
Belt setting position
1276D