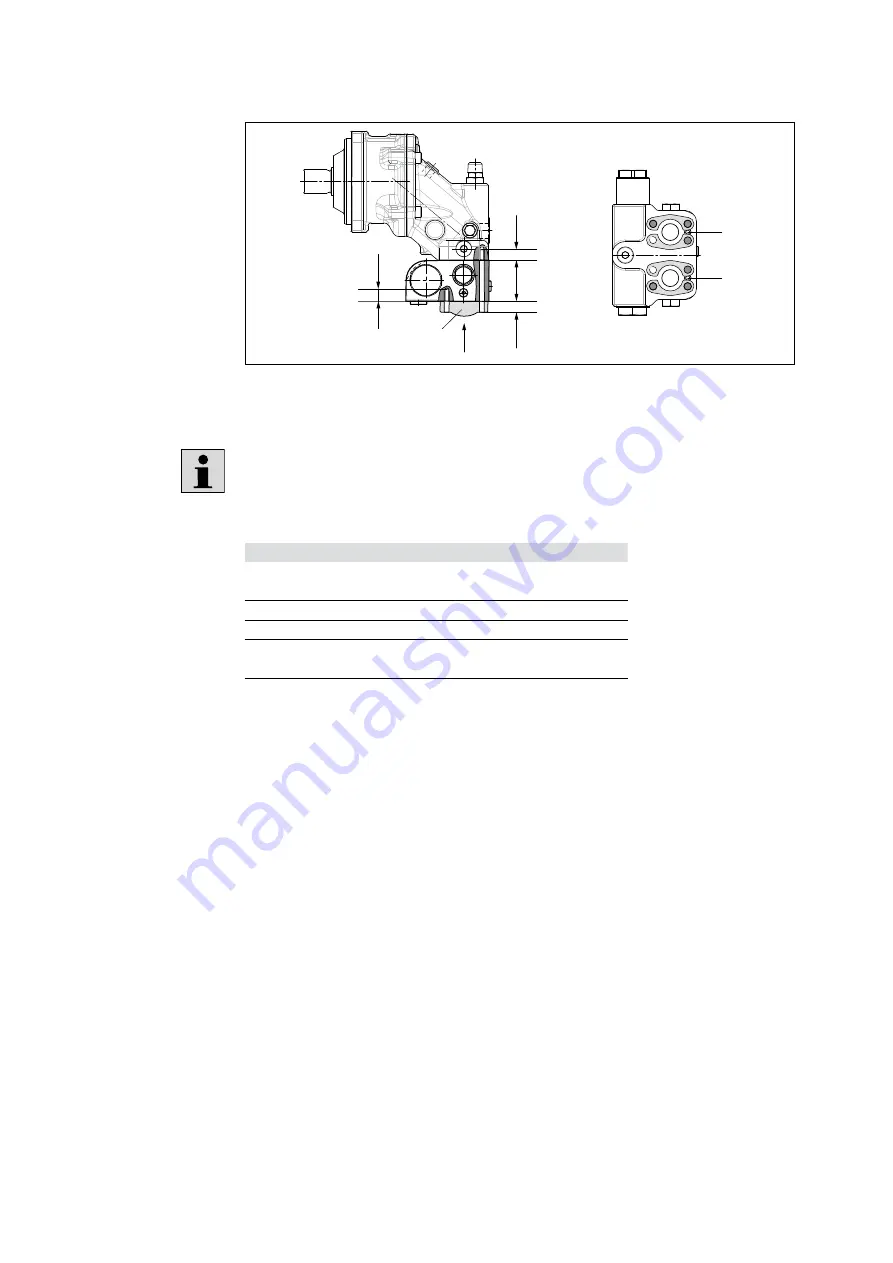
34/56 Installation
Bosch Rexroth AG
, A2FM/A2FE/A2FMT Series 70, RE 91071-01-B/06.2018
2
4
6
8
7
5
3
1
2)
2)
Y
1)
B1
B2
B3
Y
B4
1)
SAE flange
2)
Tacking screw (M6 x 1, length = B1 + B2, DIN 912)
Fig. 11: Mounting the counterbalance valve
The SAE flange and corresponding mounting bolts are not included in the scope
of delivery.
Table 14: Thread sizes and dimensions
Size
56, 63
80, 90
Dimension B1
1)
M10 x 1.5
17 deep
M12 x 1.75
18 deep
Dimension B2
68 mm
68 mm
Dimension B3
Customer-specific (flange-dependent)
Dimension B4
M10 x 1.5
15 deep
M12 x 1.75
16 deep
DIN 13 fastening thread For DIN 13 mounting bolts, we recommend checking the tightening torque
on a case-by-case basis according to VDI 2230 Edition 2003.
1)
Min. required thread reach 1 x Ø of thread
View