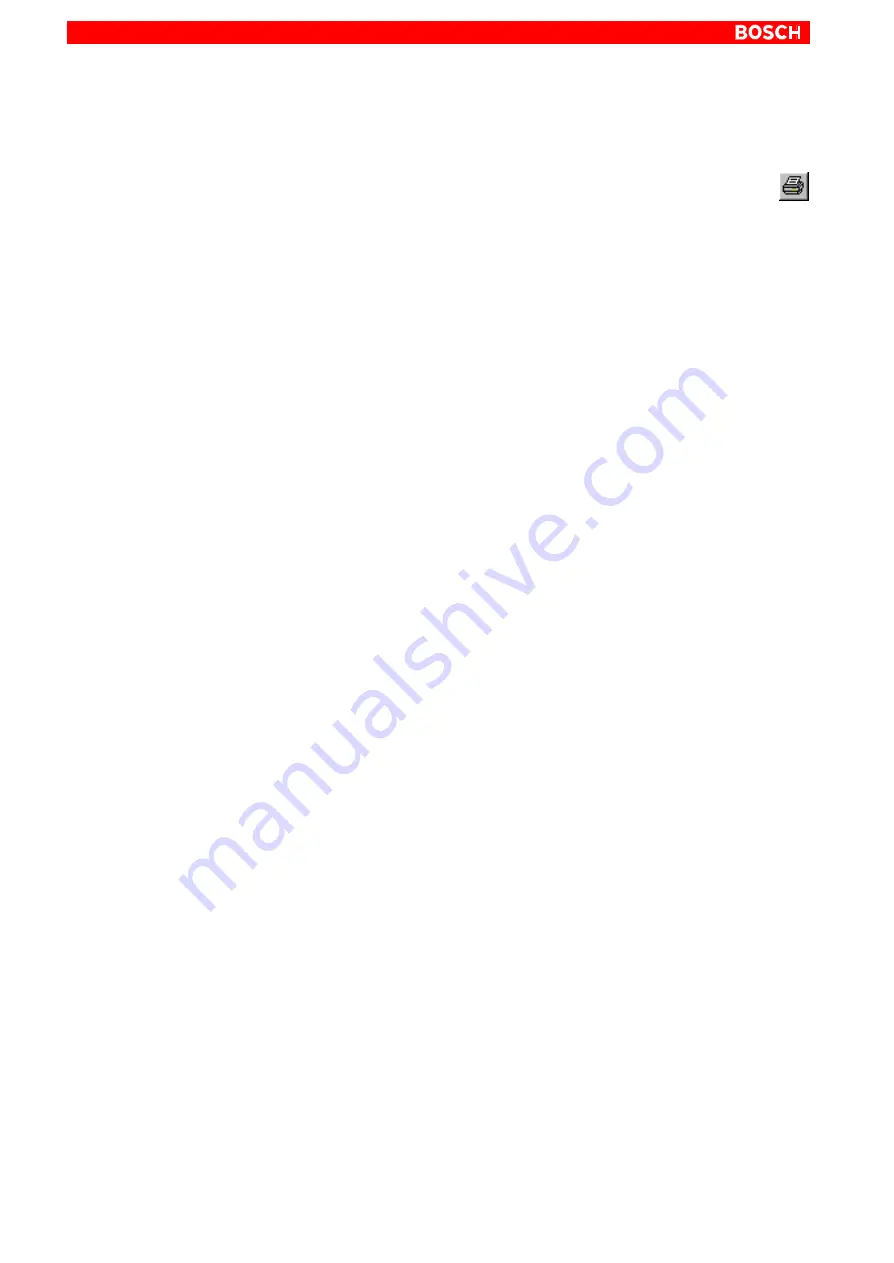
Project Configurator
3–22
1070 072 262-101 (01.09) GB
3.1.10
Document Configuration File
L
Start documentation via menu FILE
"
PRINT or
symbol.
The following options may be selected in the dialog box ”print configuration
file”:
D
Overall system
D
Selected racks
D
Version with Ethernet parameters
D
Version without Ethernet parameters