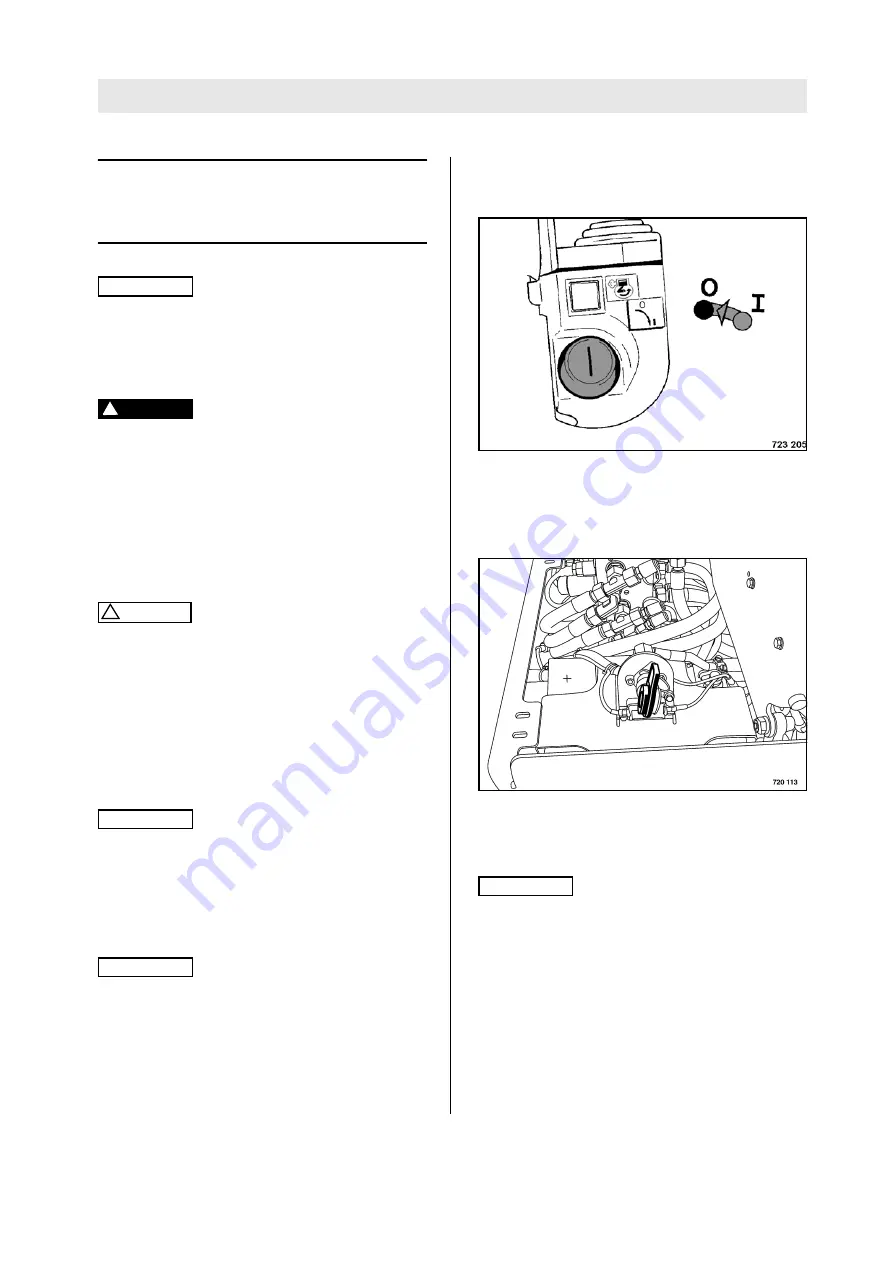
Operation
BOMAG
47
BMP 8500
4.11 Replacing, recharging the
radio remote control power
pack
i
Note
As standard the power pack is recharged in the
machine through the spiral cable. A separate bat-
tery charger is available as an option. The re-
charging time is approx. 6 hours.
!
Danger
Operate the battery charger only in dry rooms
at temperatures of min. 0 °C to max. 40 °C!
A charged power pack is a concentrated ener-
gy source! Do not store charged power packs
in a tool box or similar, because metal parts
may cause a short circuit. Short circuits may
also be caused by keys etc. in a trouser pock-
et.
!
Caution
Change the power pack only when the sender
is switched off.
Before connecting the battery charger make
sure that the mains voltage is in accordance
with the specifications mentioned on the bat-
tery charger.
Strictly follow the operating instructions for
the battery charger.
i
Note
Ageing of the power pack reduces the discharging
capacity and therefore the operating time of the
sender.
The full discharging capacity is only reached after
several charging cycles.
i
Note
As the charging of the power pack succeeds, the
charging current drops, so that overcharging of the
power pack is almost impossible. However, if the
control is switched off for a couple of days (holi-
days, bad weather) you should also disconnect the
charging unit from the mains supply or switch off
the main battery switch.
Charging the power pack in the ma-
chine
Fig. 69
l
Switch off the transmitter (Fig. 69) with the ig-
nition key.
l
Plug the spiral cable into the transmitter
Fig. 70
l
The main battery switch (Fig. 70) must be
switched on.
i
Note
The power pack recharging time is approx. 6
hours.
Summary of Contents for BMP 8500
Page 2: ......
Page 7: ...BOMAG 7 BMP 8500 1 Technical Data...
Page 12: ...Technical Data BOMAG 12 BMP 8500...
Page 13: ...BOMAG 13 BMP 8500 2 Safety regulations...
Page 23: ...BOMAG 23 BMP 8500 3 Indicators and Controls...
Page 24: ...Indicators and Controls BOMAG 24 BMP 8500 Fig 10...
Page 31: ...BOMAG 31 BMP 8500 4 Operation...
Page 55: ...BOMAG 55 BMP 8500 5 Maintenance...
Page 64: ...Maintenance BOMAG 64 BMP 8500...
Page 68: ...Every 10 operating hours BOMAG 68 BMP 8500...
Page 76: ...Every 250 operating hours BOMAG 76 BMP 8500...
Page 88: ...Every 3000 operating hours BOMAG 88 BMP 8500...
Page 94: ...As required BOMAG 94 BMP 8500...
Page 95: ...BOMAG 95 BMP 8500 6 Trouble shooting...
Page 126: ...Trouble shooting BOMAG 126 BMP 8500...
Page 127: ......
Page 128: ......