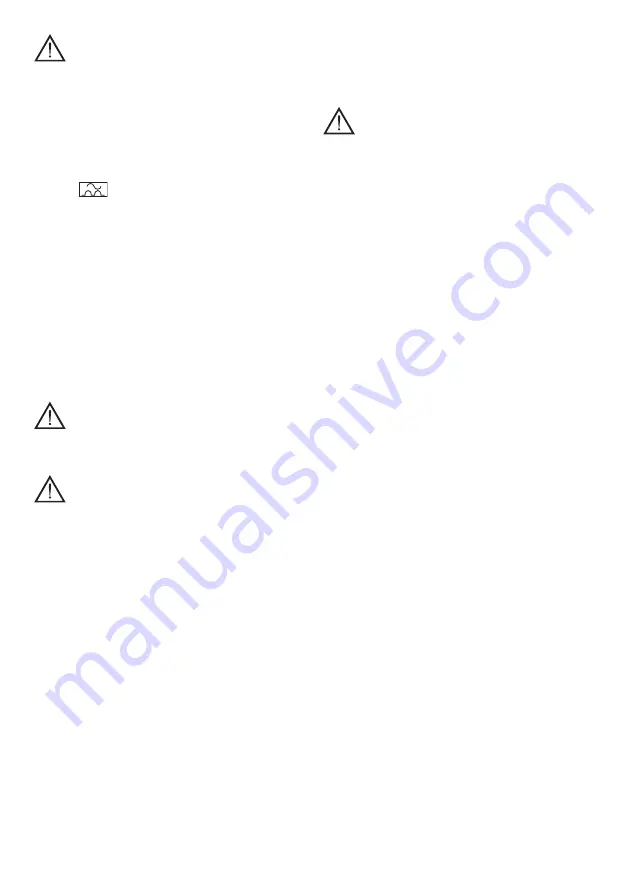
- 8 -
WARNING! Prevent the machine from tipping up or shifting
dangerously, by positioning it on a level surface that is able to
support its weight.
CONNECTION TO THE MAIN POWER SUPPLY
- Before making any electrical connection whatsoever, check the power
source rating plate to make sure that the mains voltage and frequency
correspond with those at the place where the machine is to be installed.
- The power source must be connected only and exclusively to a power
supply system with a neutral conductor connected to earth.
- In order to guarantee protection against indirect contact use RCD’s of
the following types:
- Type A (
).
- In order to satisfy the requirements of the EN 61000-3-11 (Flicker)
standard we recommend connecting the power source to interface
points of the main power supply that have an impedance of less than
Zmax = 0.2 ohm.
- The plasma cutting system does not fall within the requisites of IEC/EN
61000-3-12 standard.
Should it be connected to a public mains system, it is the installer’s
responsibility to verify that the plasma cutting system itself is suitable
for connecting to it (if necessary, consult the distribution network
company).
Plug and outlet
Connect the power supply cable to a standard (
3P + T
) plug of
appropriate capacity and prepare a power supply outlet fitted with fuses
or an automatic circuit-breaker; the corresponding earth terminal should
be connected to the (yellow-green) earth conductor of the power supply.
Table 1 (
TAB.1
) shows the recommended sizes (in amps) of the delayed
mains fuses, to be chosen according to the maximum rated current
output from the power source, and to the rated power supply voltage.
ATTENTION! Failure to comply with the above rules renders
the safety system (class
I
) ineffective, with resulting serious risks for
people (e.g. electric shock) and for property (e.g. fire).
CUTTING CIRCUIT CONNECTIONS
ATTENTION! BEFORE CARRYING OUT THE FOLLOWING
CONNECTIONS, MAKE SURE THE CURRENT SOURCE IS OFF AND
DISCONNECTED FROM THE MAINS.
Table 1
(TAB. 1)
gives the recommended values for the return cable (in
mm
2
) according to the maximum energy supplied by the machine.
Compressed air connections (Fig. H).
- Prepare a compressed air distribution line with a working pressure and
minimum capacity indicated in table 2 (TAB. 2).
- Pressure reducer connected as indicated (Fig. E).
IMPORTANT!
Do not exceed the maximum input pressure of 8 bar. Air containing large
quantities of humidity or oil can cause excessive wear of consumable
parts or damage the torch. If in doubt concerning the quality of the
compressed air available, it is recommended to use an air dryer to be
installed downstream of the inlet filter. Use a flexible hose to connect the
compressed air line to the machine, using one of the fittings supplied to
be mounted on the air inlet filter at the back of the machine.
Connecting the cutting current return cable.
Connect the cutting current return cable to the piece to be cut or the
metal support bench taking the following precautions:
- Check that a good electric contact is established especially when
cutting sheet metal with insulating, oxidised coatings etc.
- Connect the mass as close as possible to the cutting point.
- Do not use metal structures that are not part of the workpiece as a
cutting current return conductor; this can endanger safety and give
unsatisfactory cutting results.
- Do not connect the mass on the section of the piece to be removed.
Connecting the plasma cutting torch (Fig. F) (were available)
Insert the male end of the torch in the central connector on the front
panel of the machine, making sure the polarisation key is aligned. Fully
tighten the locking ring nut clockwise to guarantee there are no leaks in
the air and current flows.
In some models, the torch is supplied already connected to the current
source.
IMPORTANT!
Before commencing cutting operations, check the consumable parts
are assembled correctly, inspecting the torch head as indicated in the
“TORCH MAINTENANCE” chapter.
WARNING!
USING THE PLASMA CUTTING SYSTEM SAFELY.
Only the torch model as envisaged, coupled with the corresponding
power source as indicated in TAB. 2, are able to guarantee effective
protection by the safety system provided by the manufacturer
(interlocking system).
- DO NOT USE other makes of torch and related consumable parts.
- DO NOT ATTEMPT TO COUPLE THE POWER SOURCE with torches
built for cutting or welding procedures that are not contemplated
in these instructions.
Failure to comply with these rules may cause serious hazards,
endangering the physical safety of the user and damaging the
apparatus.
6. PLASMA CUTTING: PROCESS DESCRIPTION
The plasma arc and plasma cutting application principle.
Plasma is a gas heated to an extremely high temperature and ionised
so that it becomes an electrical conductor. This cutting procedure uses
plasma to transfer the electric arc to the metal piece that is melted by the
heat and separated. The torch uses compressed air supplied by a single
source, both for plasma gas and for cooling and protection gas.
Starting the pilot arc
The cycle is started by a pilot current that flows between the electrode
(polarity -) and the torch nozzle (po) and the start of the air flow.
Approaching the torch to the piece to be cut, connected to the current
source polarity (+), the pilot arc is transferred and creates a plasma arc
between the electrode (-) and the piece itself (cutting arc). The pilot arc is
excluded as soon as the cutting arc is established between the electrode
and the piece.
The factory setting stay time of the pilot arc is 2 seconds (4 seconds in
GOUGING mode); if the arc transfer to the piece is not effected within this
time, the cycle is automatically blocked, maintaining the cooling air.
To start the cycle again, release the torch button and press it again.
Preliminary procedures.
Before commencing cutting operations, check the consumable parts
are assembled correctly, inspecting the torch head as indicated in the
“TORCH MAINTENANCE” paragraph.
- Turn on the current supply and set the cutting current
(Fig. D-1)
according to the thickness and type of metal material to be cut.
- Press the air button
(Fig. C-3)
to start the air flow.
- During this phase, adjust the air pressure until the pressure value
required for the type of torch being used is visible on the display
(TAB.
2)
.
- Adjust the knob:
pull upwards
to release it and then
turn
it to adjust
the pressure to the value indicated in the TORCH TECHNICAL DATA.
- Read the required value on the pressure gauge and then press the knob
to lock the setting.
- Allow the air flow to end spontaneously to make it easier to remove any
condensate accumulated in the torch.
Cutting procedure (Fig. L).
- Approach the torch nozzle to the edge of the piece (about 2 mm), and
press the torch button; the pilot arc is triggered after about 1 second.
- If the distance is suitable, the pilot arc is immediately transferred to the
piece giving rise to the cutting arc.
- Move the torch on the surface of the piece along the ideal cutting line
at a regular pace.
- Adjust the cutting rate according to the thickness and selected current,
checking that the arc exiting the lower surface of the piece is inclined
by 5-10 degrees in relation to the vertical line, in the opposite direction
to the operating direction.
Grid cutting procedure (where applicable)
This function can be useful when cutting perforated or grid metal sheets:
- Use the “select mode” button (Fig. C-2) to select the grid cutting mode.
On completing the cutting cycle, keeping the torch button pressed, the
pilot arc will restart automatically. Only use this function when required