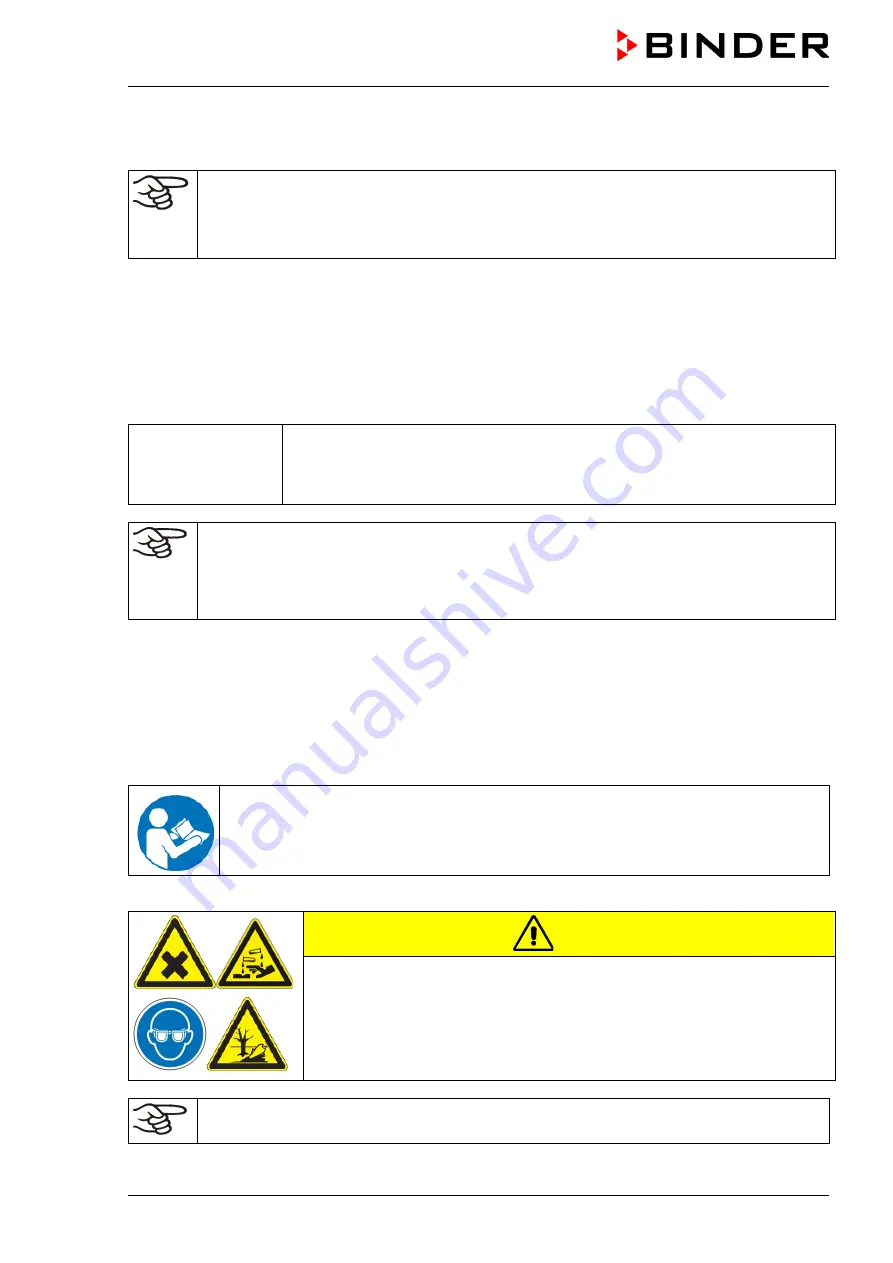
MK LIT (E5) 01/2021
page 144/172
27.3 Decontamination / chemical disinfection
With every decontamination / disinfection method, always use adequate personal safety con-
trols.
If the CO
2
fire suppression device has been triggered, please observe the information in chap.
The operator must ensure that proper decontamination is performed in case a contamination of the cham-
ber by hazardous substances has occurred.
Disconnect the chamber from the power supply prior to chemical decontamination. Pull the power plug.
Do not use decontamination agents that may cause a hazard due to reaction with components of the device
or the charging material. If there is doubt regarding the suitability of cleaning products, please contact
BINDER service.
You can use the following disinfectants:
Inner chamber
Standard commercial surface disinfectants free from acid or halides.
Alcohol based solutions.
We recommend using the disinfectant spray Art. No. 1002-0022.
We recommend using the disinfectant spray Art. No. 1002-0022 for chemical disinfection.
Any corrosive damage that may arise following use of other disinfectants is excluded from lia-
bility by BINDER GmbH.
Any corrosive damage caused by a lack of cleaning, is excluded from liability by BINDER GmbH.
In case of contamination of the interior by biologically or chemically hazardous material, there are two pos-
sible procedures depending on the type of contamination and charging material.
(1) Spray the inner chamber with an appropriate disinfectant.
Before start-up, the chamber must be absolutely dry and ventilated, as explosive gases may form
during the decontamination process.
(2) If necessary, have strongly contaminated inner chamber parts removed by an engineer for cleaning,
or have them exchanged. Sterilize the inner chamber parts in a sterilizer or autoclave.
In case of eye contact, the disinfectant spray may cause eye damage due to chemical
burns. Follow the operating instructions and safety hints labeled on the bottle of the disin-
fectant spray.
Recommended precautions: To protect the eyes use sealed protective goggles.
CAUTION
Danger of chemical burns through eye contact
with the disinfectant
spray.
Eye damage. Environmental damage
∅
Do NOT empty the disinfectant into drains.
Wear protective goggles.
After using the disinfectant spray, allow the chamber to dry thoroughly, and aerate it suffi-
ciently.
Summary of Contents for 9020-0402
Page 159: ...MK LIT E5 01 2021 page 159 172 30 7 Dimensions LIT MK 240 dimensions mm...
Page 160: ...MK LIT E5 01 2021 page 160 172 LIT MK 720 dimensions mm...
Page 162: ...MK LIT E5 01 2021 page 162 172...
Page 163: ...MK LIT E5 01 2021 page 163 172...
Page 165: ...MK LIT E5 01 2021 page 165 172...
Page 166: ...MK LIT E5 01 2021 page 166 172 31 3 Safety concept certificate from T V S d...
Page 173: ......