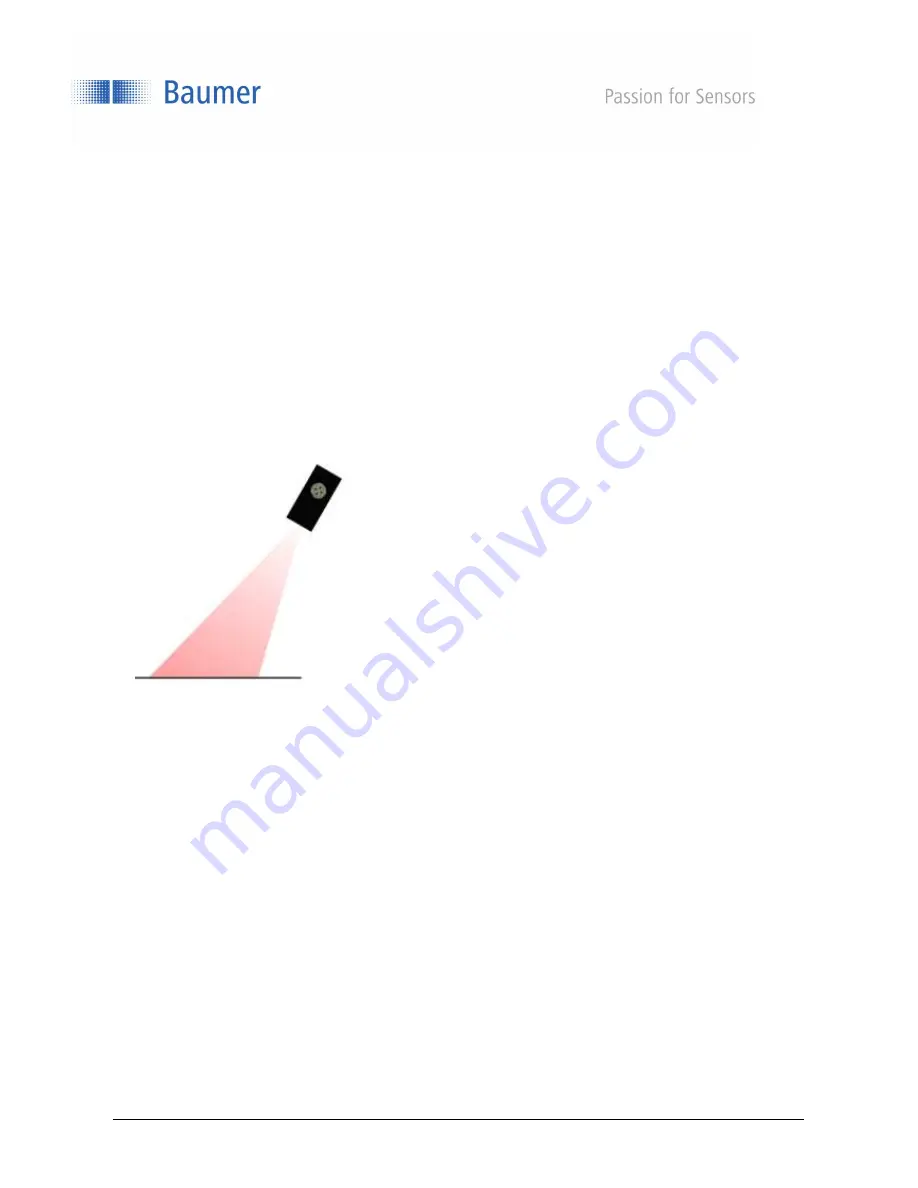
en_BA_OXH7_PosCon_TCP_IP.docx
36/98
Baumer Electric AG
Friday, June 15, 2018 12:44:11 PM/tof V1.0 ANW_81184815
Frauenfeld, Switzerland
The sensor is aligned with the reference surface. The reference surface must be within the sensor's field of
view (distance from sensor to reference surface less than distance from sensor to end of measuring range
Sde).