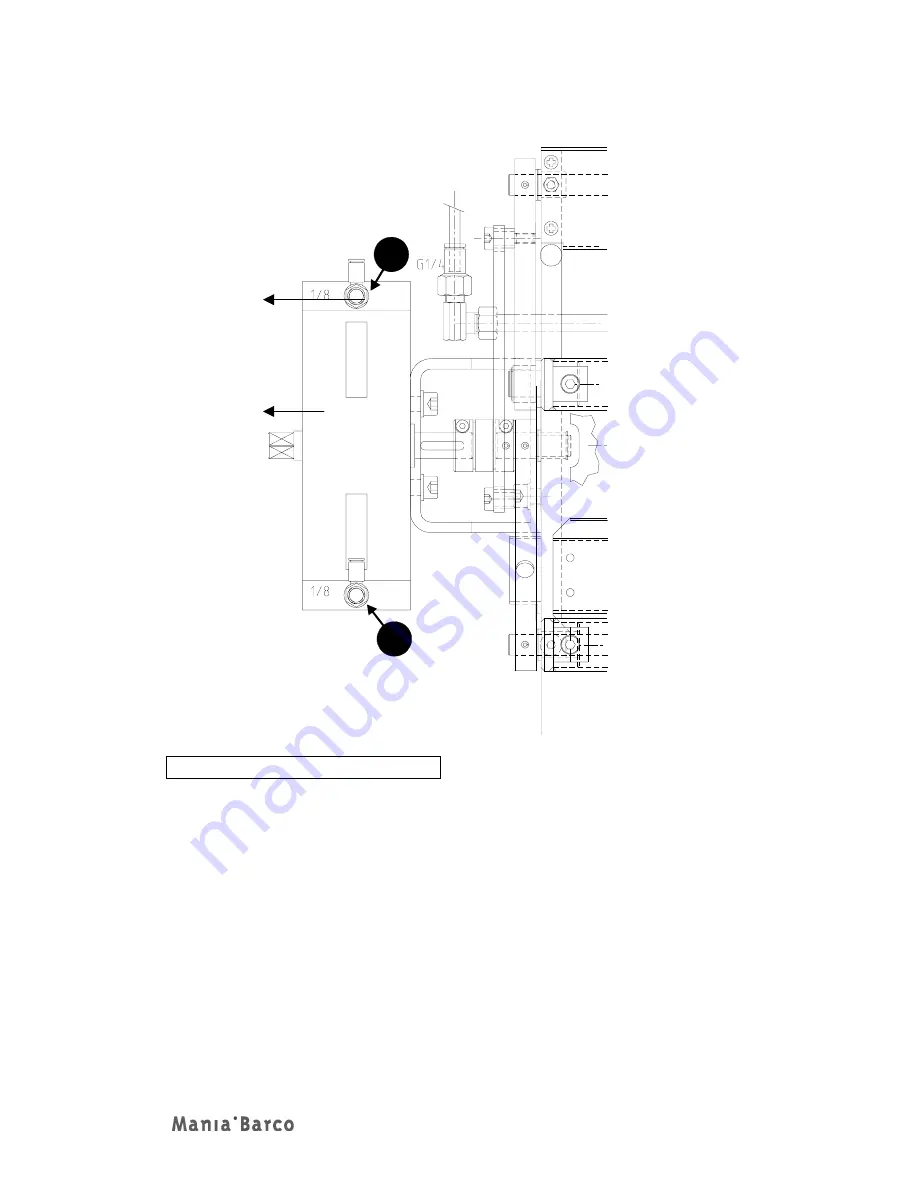
Field Service Manual
December 2003
Page 44 of 276
Mechanical.
2
1
Speed adjustment film bridge
Speed controller: pneumatic device to adjust the amount of pressure
Rotary actuator: Making a rotation by means off pressure
Adjust the speed of the film bridge.
1. Close both speed controllers
and
on the rotary actuator.
2. The upper speed controller
of the rotary actuator controls the speed of the film
feed bridge coming down.
3. The lower speed controller
of the rotary actuator controls the speed of the film
feed bridge going upwards. Whenever you change the speed of the film feed
bridge, you have to check it again putting the film feed bridge several times up
and down. Fine tune if necessary. Place the film feed bridge up with the command
“8 SFDREL” and lower it down again with the command “8 RFDREL”
Rotary
Actuator
Speed
Controller
Summary of Contents for SilverWriter 800
Page 6: ...Field Service Manual December 2003 Page 6 of 276 ...
Page 8: ...Field Service Manual December 2003 Page 8 of 276 ...
Page 18: ...Field Service Manual December 2003 Page 18 of 276 ...
Page 20: ...Field Service Manual December 2003 Page 20 of 276 ...
Page 24: ...Field Service Manual December 2003 Page 24 of 276 ...
Page 95: ...Field Service Manual December 2003 Page 95 of 276 Multi FilmFeeder solid state panel ...
Page 96: ...Field Service Manual December 2003 Page 96 of 276 ...
Page 122: ...Field Service Manual December 2003 Page 122 of 276 ...
Page 130: ...Field Service Manual December 2003 Page 130 of 276 ...
Page 134: ...Field Service Manual December 2003 Page 134 of 276 ...
Page 168: ......
Page 172: ...Field Service Manual December 2003 Page 172 of 276 ...
Page 174: ...Field Service Manual December 2003 Page 174 of 276 ...
Page 187: ...Field Service Manual December 2003 Page 187 of 276 ...
Page 216: ...Field Service Manual December 2003 Page 216 of 276 ...
Page 220: ...Field Service Manual December 2003 Page 220 of 276 Main directory structure ...
Page 225: ...Field Service Manual December 2003 Page 225 of 276 Adding a DPF file in the plotter queue ...
Page 227: ...Field Service Manual December 2003 Page 227 of 276 Stop logging ...
Page 234: ...Field Service Manual December 2003 Page 234 of 276 ...
Page 240: ...Field Service Manual December 2003 Page 240 of 276 ...
Page 242: ...Field Service Manual December 2003 Page 242 of 276 ...
Page 246: ...Field Service Manual December 2003 Page 246 of 276 ...
Page 248: ...Field Service Manual December 2003 Page 248 of 276 ...
Page 252: ...Field Service Manual December 2003 Page 252 of 276 ...
Page 268: ...Field Service Manual December 2003 Page 268 of 276 ...
Page 270: ...Field Service Manual December 2003 Page 270 of 276 ...
Page 274: ...Field Service Manual December 2003 Page 274 of 276 ...