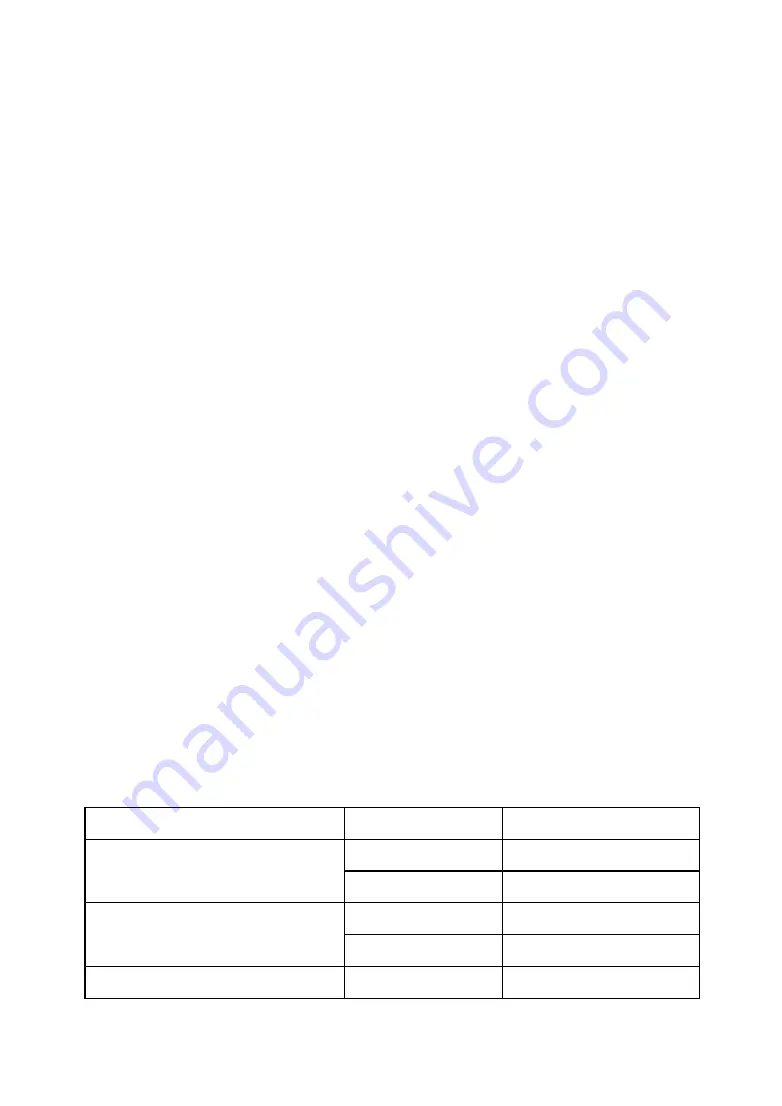
107
4. Trial run
After installing the gear pump in the truck, check it reassembled for specified
performance and do the trial run for it. If the pump’s gears are seized or internal parts
worn excessively, you should renew the hydraulic oil and filters or clean them. The trial
run procedures are as follows:
(a) Install the gear pump in the truck. Then install a pressure gauge in pressure
inspection port of the control valve.
(b) Loose the adjustment screw of the relief valve and run the pump at 500 to 1000
rpm for ten minutes. The oil pressure should be lower than 10 kg/cm
2
.
(c) Increase the speed of the pump to 1500 to 2000 rpm for ten minutes.
(d) Without the change of the speed in step, increase the pressure to 20 to 30 kg/cm
2
at a time and run the pump for five minutes. Then increase the pressure to 175 kg/cm
2
.
Each circuit works for five minutes and then renews the return filter.
During the increase of the pressure, observe the change of oil temperature and pump
body surface temperature and working voice. If the oil temperature or pump body surface
temperature is excessively high, decrease the load to reduce the oil temperature, then go
on doing the test.
(e) After the trial run, measure the flow amount through lift speed with the pressure of
175 kg/cm
2
of the relief valve.
7.2.2 Troubleshoot
If the hydraulic system has a fault, find out the possible cause according to the
following tables and repair it.
1. Control valve
Problem
Possible cause
Remedy
Lower oil pressure of the lifting oil
circuit
Spool is held up
Disassembly and clean
Oil hole is blocked
Disassembly and clean
Vibrate and the oil pressure rising
slowly
Spool is held up
Disassembly and clean
Exhaust not fully
Exhaust fully
The oil pressure of the steering oil
Spool is held up
Disassembly and clean
Summary of Contents for CPD10
Page 1: ......
Page 6: ...1 Ⅰ External view and specification External view of electric forklift truck ...
Page 26: ...21 2 General information when operating 3 Nameplate of forklift truck 4 Lubrication system ...
Page 27: ...22 5 Capacity chart 6 Inspections before starting 7 Adjust parking brake 8 Add hydraulic oil ...
Page 33: ...28 Fig 1 2 Gear box and differential 2 3t ...
Page 34: ...29 Fig 1 3 Differential ...
Page 57: ...52 Fig 4 2 Principle of electric system DC CPD10 25 ...
Page 58: ...53 Fig 4 3 Principle of electric system DC CPD30 ...
Page 60: ...55 Fig 4 5 Principle of electric system AC ...
Page 77: ...72 4 8 Harness Fig 4 10 Harness DC CPD10 30 ...
Page 78: ...73 Fig 4 11 Harness AC CPD10J 15J ...
Page 79: ...74 Fig 4 12 Harness AC CPD20J 30J ...
Page 81: ...76 Fig 5 1 Assembly diagram of lifting motor Fig5 2 Lifting motor ...
Page 101: ...96 3 Hydraulic oil circuit ...
Page 115: ...110 Fig 8 2 Inner and outer mast 2 3t ...
Page 124: ......