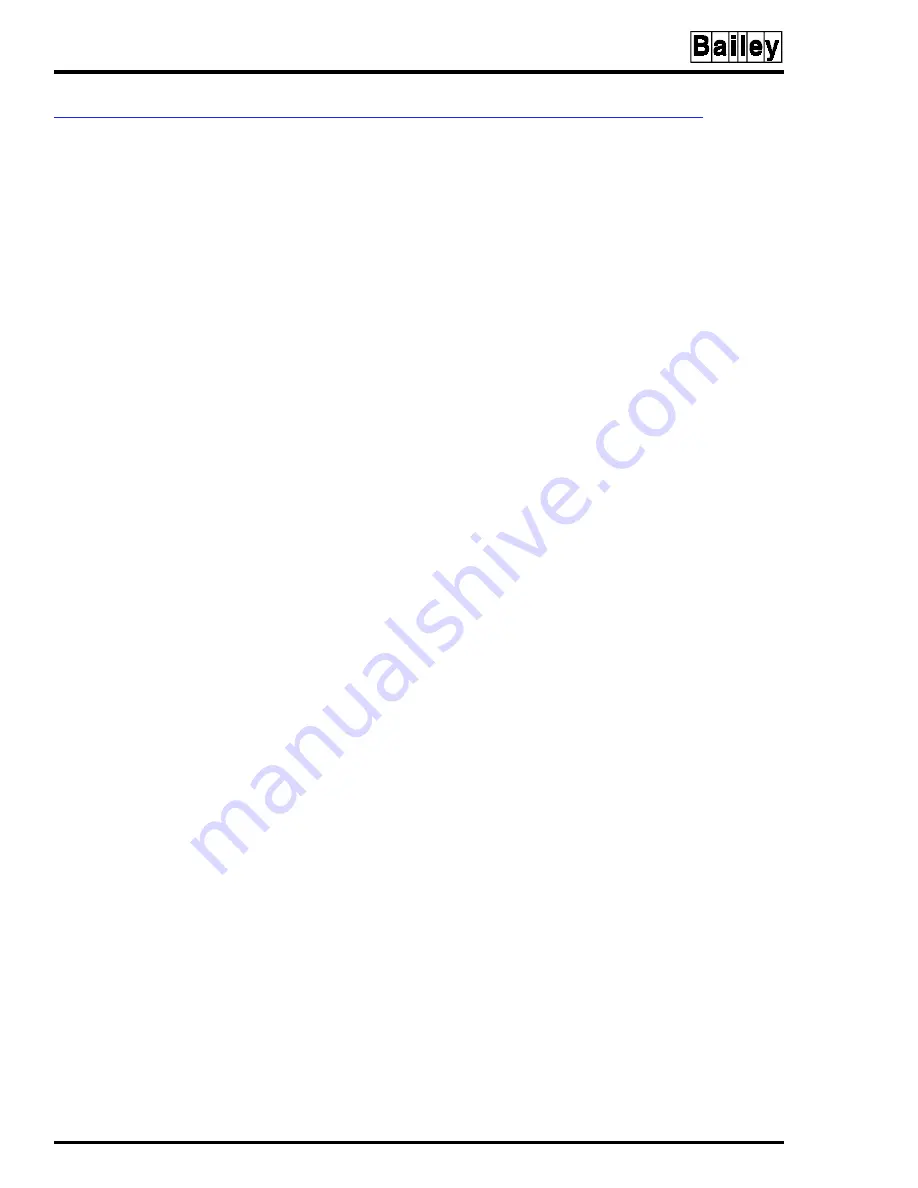
CALIBRATION
CONTROLLER TUNING
4 - 4
I-E96-315B
®
Tuning the Controller Gain
The practical method of setting controller gain requires an indi-
vidual with turbine control experience. The individual tuning
the system should be familiar with plant operation under nor-
mal conditions, know turbine start-up procedures and have
experience in tuning control systems. In cases where the valve
is a distance from the control cabinet or separated by barriers,
two people are needed to tune the system. One person observes
the valve operation while the other person sets the controller
gain and enters position demand. Communication by tele-
phone or intercom is recommended. The radio frequency inter-
ference from walkie-talkies can cause problems with the
control system. Exercise extreme care if you use a
walkie-talkie. When keying the unit, the operator should be at
least two meters away from the cabinet and the cabinet doors
closed.
Before tuning the controller gain, verify that the following con-
ditions exist:
1. Calibration of the HSS, hydraulic actuator and LVDT is
complete.
2. The controller gain is set to 1 (switch 2 pole eight is closed).
Refer to Table
for controller gain switch settings.
3. The calibration command bit in the block address specified
in S3 is set to 0 (normal operation).
4. The GO\HOLD bit in the block address specified in S4 is
set to 0 (HOLD).
5. The turbine is off-line.
To tune the controller gain:
1. Enter position demands (via the operator interface) of 25
percent, 50 percent, 75 percent and 90 percent, opening the
valve. Observe the response of the throttle valve at each
demand level. The valve should respond without oscillating at
any level of demand.
2. Enter position demands (via the operator interface) of 25
percent, 50 percent, 75 percent and 90 percent, closing the
valve. Observe the response of the throttle valve at each
demand level. The valve should respond without oscillating at
each level of demand.