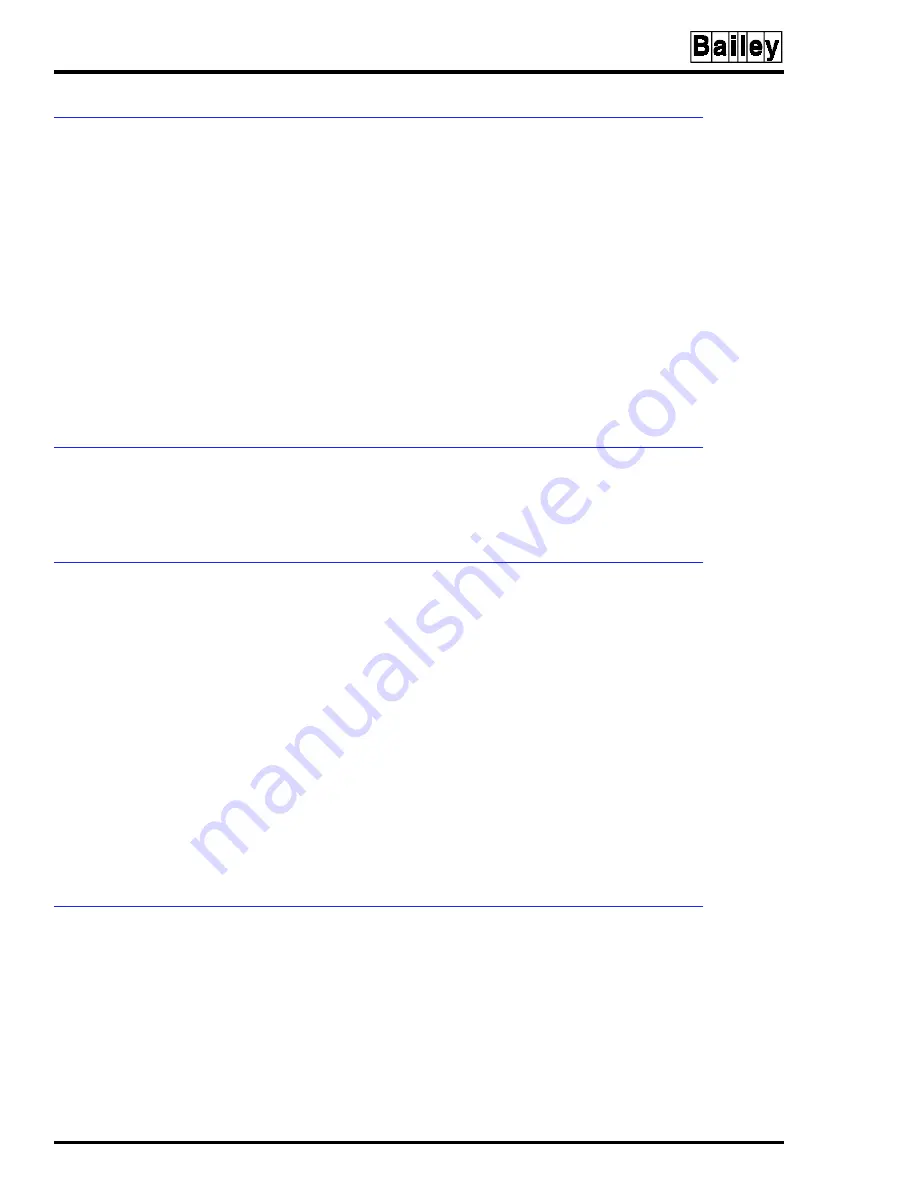
INTRODUCTION
MFC DESCRIPTION
1 - 2
I-E96-213A
®
MFC DESCRIPTION
The IMMFC05 is a multi-layered printed circuit board. On
board is a CMOS 68000 microprocessor (12 MHz speed),
EPROM, RAM, and NVM (battery backed nonvolatile memory),
VLSI and advanced CMOS support circuitry. The board is
attached to a faceplate. Visible through the faceplate is a group
of eight LEDs and a Status LED. The eight LEDs display mod-
ule operation and error codes; the Status LED indicates the
operating state.
The IMMFC05 occupies one slot in the Module Mounting Unit
(MMU) of the INFI 90 cabinet. Each MMU can hold a total of 12
single width INFI 90 modules. The MMU backplane provides
module power, Module Bus (module to module communica-
tion), and Slave Expander Bus (slave module to MFC
communication).
FEATURES
The module's main purpose is process I/O interfacing and con-
trol strategy execution. In addition, the following features are
available.
Redundancy
An IMMFC05 configured the same as the primary provides
backup to the primary module. In a redundant setup, one
module is the primary. It performs computations, runs control
functions, etc. The other, the backup module, monitors
(tracks) the primary. The backup copies the primary control-
lers outputs, and waits in a hot standby mode. There is con-
stant communication between the primary and the backup
module. If the primary module should fail, the backup
assumes immediate control. Since the backup copied the pri-
mary's outputs, there is no break in control to the process.
Redundancy is enabled with switch SW4. Refer to
NOTE: Firmware revision levels must be the same in the primary
and redundant modules. If it is different and a failover occurs, the
redundant module may operate erratically.
On-Line Configuration
On-line configuration enables users with backup MFCs to
make configuration changes. On-line configuration changes do
not affect the primary module or interrupt the control process.
This happens by taking the backup MFC out of the tracking
mode, changing the desired functions and putting it back in
the tracking mode. When the new configuration in the backup
MFC starts up, it uses the present values of process outputs in