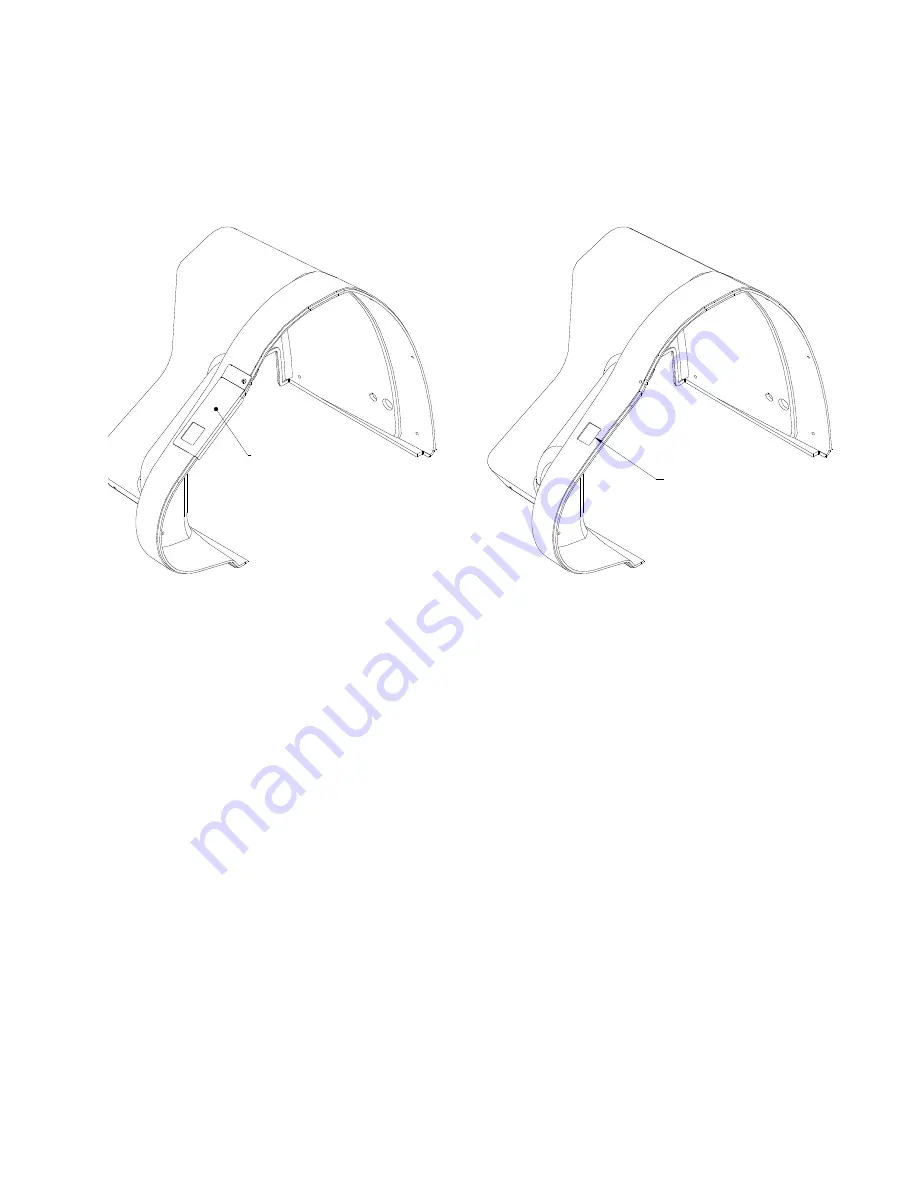
102
User’s Manual—SNAP™ 700 Printer
13. Using the supplied Template, scribe a cutout line on the Rear Cover.
SCRIBE TEMPLATE
SCRIBE AND REMOVE
THIS MATERIAL
14. Remove the material within this scribed line. Drill corners and use a Dremel Tool or
Small Saw.
15. Slide Cover onto Printer. The Cutout should be over the Control Plate on the Sensor.
The Sensor may require both horizontal and vertical readjustment to fit below the cutout.
16. Reattach the Rear Cover. Reconnect Stacker connection.
17. When ready to use a sense mark format, program the Sensor per instructions provided
with the Sensor.
5. Programming the Contrast Sensors
There are two optional contrast sensors available for the SNAP 700 printer. 620006-1 is the
standard contrast sensor. It works well in most situations where there is significant contrast
between the material background and the sense mark. In situations where there is less
contrast between the material and the sense mark, or the material and sense mark are of
similar colors, the 620007-1 Color Contrast Sensor may be required.
Both sensors have to be “taught” the difference between the material background and the
sense mark. The procedures are similar, and are described below.
Summary of Contents for SNAP 700
Page 113: ...User s Manual SNAP 700 Printer 113 Electrical Drawings...
Page 115: ...User s Manual SNAP 700 Printer 115 Harness Connections...
Page 117: ...User s Manual SNAP 700 Printer 117 Mechanical Assembly Drawings...
Page 119: ...User s Manual SNAP 700 Printer 119 Unwind Assembly Two Shaft Design New...
Page 121: ...User s Manual SNAP 700 Printer 121 Unwind Assembly RFID 3 4 Two Shaft Design New...
Page 122: ...122 User s Manual SNAP 700 Printer Unwind Motor Assembly...
Page 123: ...User s Manual SNAP 700 Printer 123 Decurler Assembly...
Page 124: ...124 User s Manual SNAP 700 Printer Web Guide Assembly...
Page 128: ...128 User s Manual SNAP 700 Printer Bottom Print Head Assembly...
Page 129: ...User s Manual SNAP 700 Printer 129 Print Head Assembly...
Page 130: ...130 User s Manual SNAP 700 Printer Platen Roller Assembly...
Page 131: ...User s Manual SNAP 700 Printer 131 Ink Arbor Assembly...
Page 132: ...132 User s Manual SNAP 700 Printer Ink Unwind Rewind Motor s Assembly...
Page 133: ...User s Manual SNAP 700 Printer 133 Drive Assembly...
Page 134: ...134 User s Manual SNAP 700 Printer Knife Assembly...
Page 137: ...User s Manual SNAP 700 Printer 137 Knife Drive Motors Assembly...
Page 138: ...138 User s Manual SNAP 700 Printer Knife Drive Motors Assembly RFID...
Page 139: ...User s Manual SNAP 700 Printer 139 RFID Reader Assembly...
Page 140: ...140 User s Manual SNAP 700 Printer Covers Assembly...
Page 141: ...User s Manual SNAP 700 Printer 141 Cooling Fans Assembly...
Page 142: ...142 User s Manual SNAP 700 Printer Stacker Assembly Sheet 1 of 2...
Page 143: ...User s Manual SNAP 700 Printer 143 Stacker Assembly Sheet 2 of 2...