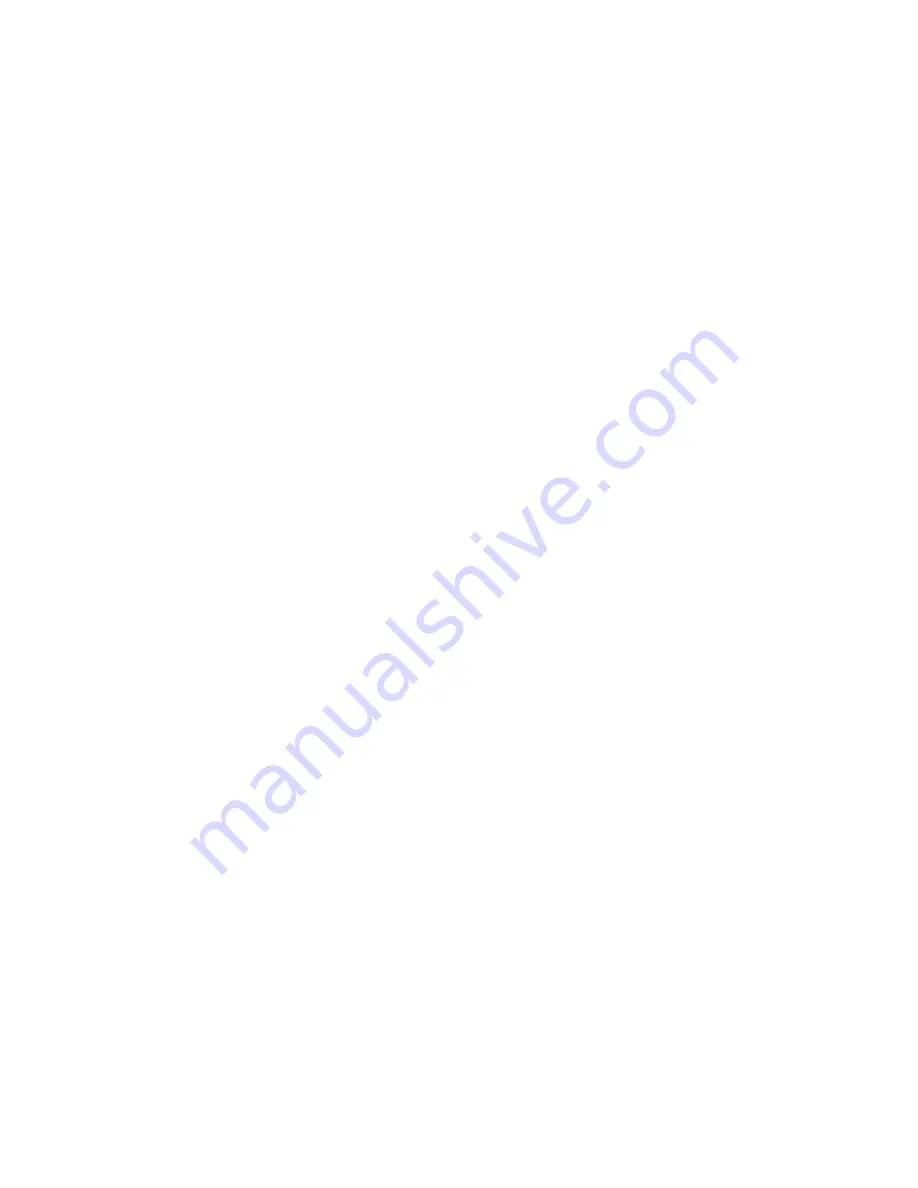
3
Avago Technologies Confidential
High Speed Electrical Signal Interface
TX
TX[0-11]p/n are the CXP module transmitter electrical
data inputs and are internally AC coupled (0.1
m
F) dif-
ferential lines with 100
W
differential terminations. AC
coupling capacitors exist inside the CXP module and are
not required on the host board. All transmitter electrical
input channels are compliant to module CPPI specifica-
tions per IEEE 802.3ba other than jitter tolerance perfor-
mance as per specified in the Transmitter Electrical Char-
acteristics section of this data sheet.
RX
Rx[0-11]p/n are the CXP module receiver electrical data
outputs and are internally AC coupled (0.1
m
F) differen-
tial lines that should be terminated with 100
W
differen-
tial at the host side. AC coupling capacitors exist inside
the CXP module and are not required on the host board.
All receiver electrical output channels are compliant to
module CPPI specifications per IEEE 802.3ba other than
jitter output performance and output differential voltage
swing as per specified in the Receiver Electrical Character-
istics section of this data sheet.
Tx Equalization Control
Tx Input Equalization Control: Four bit code blocks (bits
7-4 or 3-0) are assigned to each channel.
•
Codes 1xxxb are reserved.
•
Writing 0111b calls for full-scale equalization.
•
Writing 0000b calls for no equalization.
Intermediate code values call for intermediate levels of
equalization.
Rx De-emphasis Control
Rx Output de-Emphasis Control: Four bit code blocks (bits
7-4 or 3-0) are assigned to each channel.
•
Codes 1xxxb are reserved.
•
Writing 0111b calls for full-scale de-emphasis.
•
Writing 0000b calls for minimum de-emphasis.
Writing intermediate code values calls for intermediate
levels of de-emphasis.
Regulatory & Compliance
Various standard and regulations apply to the modules.
These include eye-safety, EMC, ESD and RoHS. See the
Regulatory Section for details regarding these and
component recognition.
Handling and Cleaning
The transceiver module can be damaged by exposure to
current surges and over voltage events. Care should be
taken to restrict exposure to the conditions defined in
the Absolute Maximum Ratings. Wave soldering, reflow
soldering and/or aqueous wash process with the modules
on board are not recommended. Normal handling precau-
tions for electrostatic discharge sensitive devices should
be observed.
Each module is supplied with an inserted port plug for
protection of the optical ports. This plug should always be
in place whenever a fiber cable is not inserted.
The optical connector includes recessed elements that
are exposed whenever a cable or port plug is not inserted.
Prior to insertion of a fiber optic cable, it is recommended
that the cable end be cleaned to avoid contamination from
the cable plug. The port plug ensures the optics remains
clean and no additional cleaning should be needed. In the
event of contamination, dry nitrogen or clean dry air at
less than 20 psi can be used to dislodge the contamina-
tion. The optical port features (e.g. guide pins) preclude
use of a solid instrument. Liquids are also not advised.