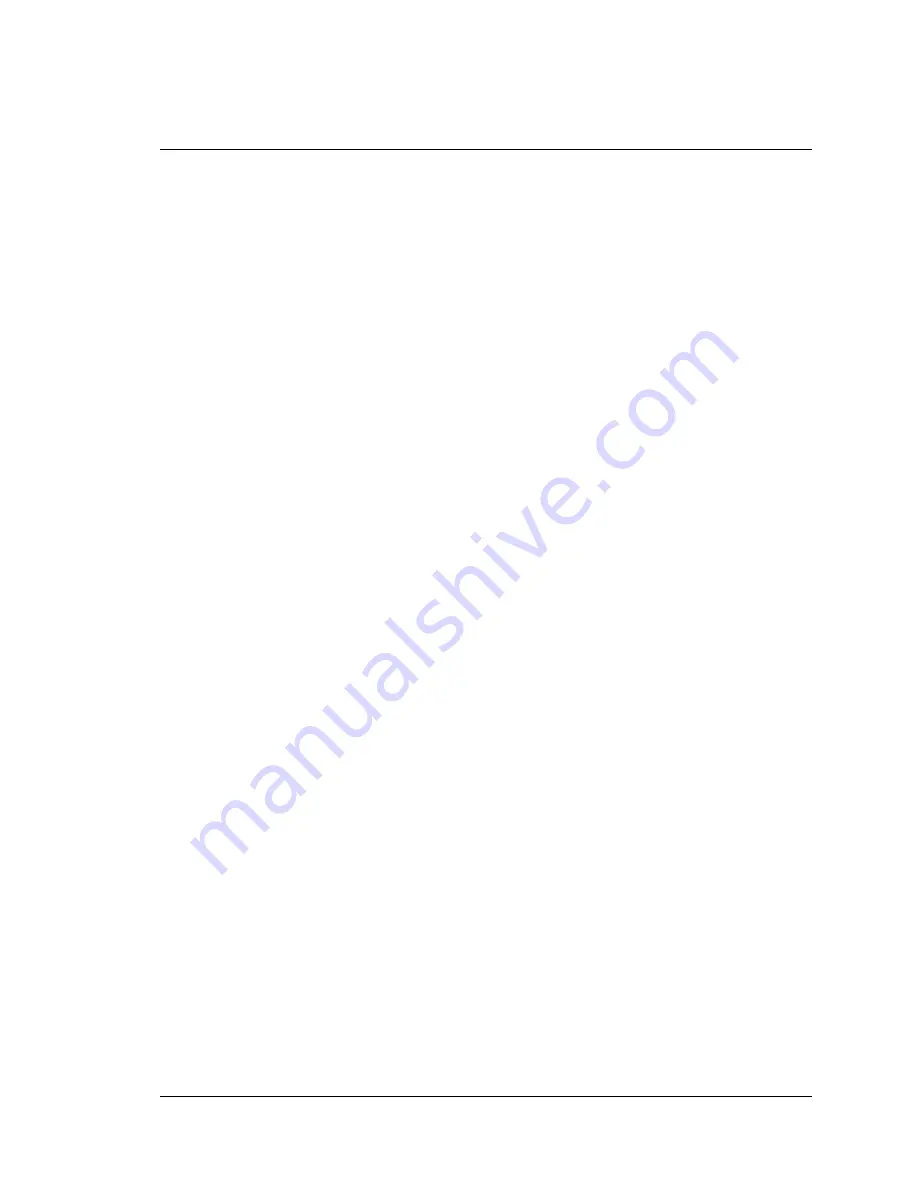
Functional
Description
3
Subsystems
Hydrogen Peroxide Delivery Subsystem
The hydrogen peroxide delivery assembly transfers hydrogen peroxide
solution from the cassette assembly to the vaporizer assembly. The
delivery process involves: accepting a valid cassette from the user,
positioning the cells in the hydrogen peroxide extractor assembly,
delivering hydrogen peroxide solution from a cell to the vaporizer,
isolating the vaporizer from atmosphere, and disposing of a used
cassette.
Vaporization Subsystem
The vaporizer receives hydrogen peroxide solution from the delivery
system and vaporizes the liquid hydrogen peroxide and water. The
condenser condenses the hydrogen peroxide vapor while allowing the
water vapor to pass through the chamber. The condenser vaporizes the
hydrogen peroxide and transfers the vapor to the chamber. The vaporizer
pressure transducer also monitors the pressure of the vapor in the
vaporizer/condenser housings.
Vacuum Subsystem
The vacuum subsystem evacuates the chamber during the vacuum steps
of the cycle, controls chamber pressure, and admits filtered air into the
chamber during venting. The vacuum subsystem is found in the base
module and the top module.
Plasma Subsystem
The plasma subsystem generates electrical energy creating a gas plasma
in the chamber that reduces residual hydrogen peroxide from the
chamber atmosphere and in the materials of the load.
The plasma subsystem consists of the LFPS II; an integrated plasma
energy feedthrough. The door open/close sensor functions as a safety
switch to prevent the LFPS II from operating when the door is open.
Hydrogen Peroxide Monitor Subsystem
The hydrogen peroxide monitor measures the concentration of hydrogen
peroxide vapor at a fixed location in the chamber during the injection and
diffusion stages of the sterilization process. The UV lamp and the lamp
manager are located in the top module; the UV detector assembly is
located in the chamber module.
STERRAD
®
NX
™
Service Guide
23
Summary of Contents for sterrad NX
Page 1: ...STERRAD NX Sterilization System Service Troubleshooting Guide...
Page 10: ......
Page 16: ......
Page 21: ...Functional Description 3 Figure 1 Software Control Diagram STERRAD NX Service Guide 21...
Page 38: ......
Page 100: ......
Page 124: ......