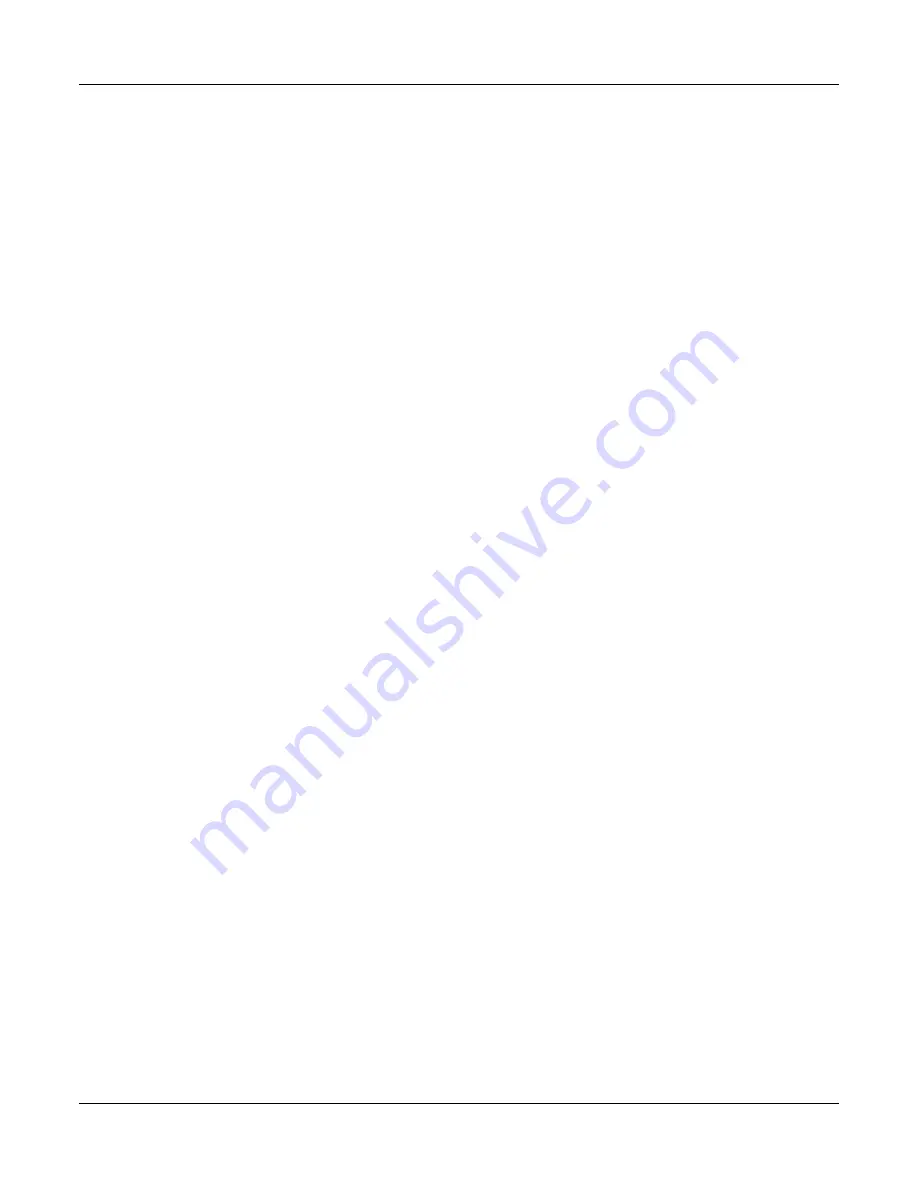
TRACKPOINT 3
OPERATION
3-103
3.7.4.12
RS-232 PARAMETER DESCRIPTION
These are the descriptions of the parameters used in the Format Sentences above unless otherwise
listed.
The TARGET NUMBER (#) represents the various target symbols and can range from 0 to 9. The
zero is output when in the self-test mode to indicate that the RS-232 data is simulated.
The TIME (TOD) is output at the beginning of each target's data. It is synchronous with the 24-
hour time on the screen of the TrackPoint. It is equal to the time that the TrackPoint received the
acoustic reply. When synchronized with the GPS clock the accuracy of the time as output is within
50 milliseconds of the actual time of reply.
The HEADING (HDG) is only displayed when a compass interface is used. The HEADING can either
be the Magnetic heading of the vessel or the True heading, if the NMEA heading data has been de-
termined to be corrected for True North. The NMEA ORE output sentence shows an identifier in the
string to show whether data is Magnetic (M), True (T) or from an Analog source (A). The heading is
also displayed on the upper left corner of the TrackPoint's screen.
The BEARING (BRG) output in degrees is a relative bearing from the ship to the target. When the
compass interface is in use, and the SYSTEM / COMPASS / RS232 TGT DATA is set to North Ref.,
the target bearing is referenced to North. The target bearing is corrected for the entered hydro-
phone offsets (target is referenced to the pitch roll center of the vessel) or if Antenna Offsets are
entered it is corrected again to the Antenna offset point. The SYSTEM / COMPASS / RS232 TGT
DATA switch can be set to either NORTH REF or BOW REF. See section 3.4.2.
The DEPRESSION ANGLE output on REV4 formats is the depression angle calculated from the fi-
nal horizontal distance and the depth (either input or calculated depth). The depression angle out-
put on the NUWC formats is the angle as measured by the hydrophone’s three elements but it has
been corrected for pitch and roll motion. It is not compensated by the hydrophone X,Y,Z deviation,
caused by the offset between hydrophone and vessel pitch / roll center. (I.e., the arc that the
hydrophone swings through during vessel motion.) System takes wherever the hydrophone was
when the reply was received and reconverts depression angle based on a gravity level measure-
ment at that position.
The SLANT RANGE (S.R.) is the measured travel time between the hydrophone and the trans-
ponder. It is output in meters, feet or yards, depending on RS-232 UNITS selection. The Slant
Range is the actual measured slant range to the transponder or responder. In transponder or re-
sponder mode no hydrophone offsets are applied to the data. If in Pinger mode it is a calculated
value with offsets applied if applicable. (See NOTE below.)
The X and Y position are the coordinates from the ship to the target. They are output in meters,
feet or yards if STANDARD, STANDARD-EC, STD W/PR, STD-EC W/PR, NCSC or NMEA ORE is se-
lected, or just meters if Format REV 4 or REV 4-EC is selected. If NMEA TTM is selected then the X
and Y ranges are in kilometers.
Summary of Contents for TRACKPOINT 3 4211A
Page 3: ......
Page 5: ......
Page 13: ...PRECAUTIONS viii ...
Page 14: ...SECTION ONE GENERAL INFORMATION ...
Page 15: ......
Page 18: ...TRACKPOINT 3 GENERAL INFORMATION 1 3 TRACKPOINT 3 CONSOLE FRONT VIEW FIGURE 1 1 ...
Page 20: ...TRACKPOINT 3 GENERAL INFORMATION 1 5 TRACKPOINT 3 SYSTEM COMPONENTS FIGURE 1 3 ...
Page 21: ...TRACKPOINT 3 GENERAL INFORMATION 1 6 FIGURE 1 4 ...
Page 27: ...TRACKPOINT 3 GENERAL INFORMATION 1 12 ...
Page 28: ...SECTION TWO INSTALLATION ...
Page 29: ......
Page 34: ...TRACKPOINT 3 INSTALLATION 2 5 FIGURE 2 2 ...
Page 35: ...TRACKPOINT 3 INSTALLATION 2 6 FIGURE 2 3 ...
Page 38: ...TRACKPOINT 3 INSTALLATION 2 9 MODEL 4740A INSTALLATION FIGURE 2 5 ...
Page 39: ...TRACKPOINT 3 INSTALLATION 2 10 FIGURE 2 6 C A U T I O N ...
Page 52: ...TRACKPOINT 3 INSTALLATION 2 23 FIGURE 2 15 ...
Page 53: ...TRACKPOINT 3 INSTALLATION 2 24 FIGURE 2 16 ...
Page 56: ...TRACKPOINT 3 INSTALLATION 2 27 FIGURE 2 17 ...
Page 62: ...SECTION THREE OPERATION ...
Page 63: ......
Page 132: ...TRACKPOINT 3 OPERATION 3 69 ...
Page 177: ...SECTION FOUR PRINCIPLES OF OPERATION ...
Page 178: ......
Page 183: ...TRACKPOINT 3 PRINCIPLES OF OPERATION 4 5 ...
Page 185: ...TRACKPOINT 3 PRINCIPLES OF OPERATION 4 7 TRACKPOINT BLOCK DIAGRAM FIGURE 4 3A ...
Page 186: ...TRACKPOINT 3 PRINCIPLES OF OPERATION 4 8 TRACKPOINT BLOCK DIAGRAM FIGURE 4 3B ...
Page 189: ...SECTION FIVE MAINTENANCE ...
Page 190: ......
Page 193: ...TRACKPOINT 3 MAINTENANCE 5 1 DSP CARD PROGRAMMING MODE JUMPER FIGURE 5 1 ...
Page 201: ...APPENDIX A CARE OF CABLES ...
Page 202: ......
Page 204: ...TRACKPOINT 3 APPENDIX A A 2 ...
Page 205: ...APPENDIX B STATIC DISCHARGE ...
Page 206: ......
Page 208: ...TRACKPOINT 3 APPENDIX B B 2 ...
Page 209: ...APPENDIX C WARRANTY ...
Page 210: ......
Page 212: ...TRACKPOINT 3 APPENDIX C C 2 ...
Page 213: ...APPENDIX D DRAWINGS ...
Page 214: ......
Page 216: ...TRACKPOINT 3 APPENDIX D D 2 ...
Page 217: ......
Page 218: ......
Page 219: ......
Page 220: ......
Page 221: ......
Page 222: ......
Page 223: ......
Page 224: ......
Page 225: ......
Page 226: ......
Page 230: ......
Page 231: ......
Page 232: ......
Page 235: ......
Page 236: ......
Page 240: ......
Page 241: ......
Page 242: ......
Page 244: ......
Page 246: ......
Page 247: ......
Page 248: ......
Page 249: ......
Page 250: ......
Page 251: ......
Page 252: ......