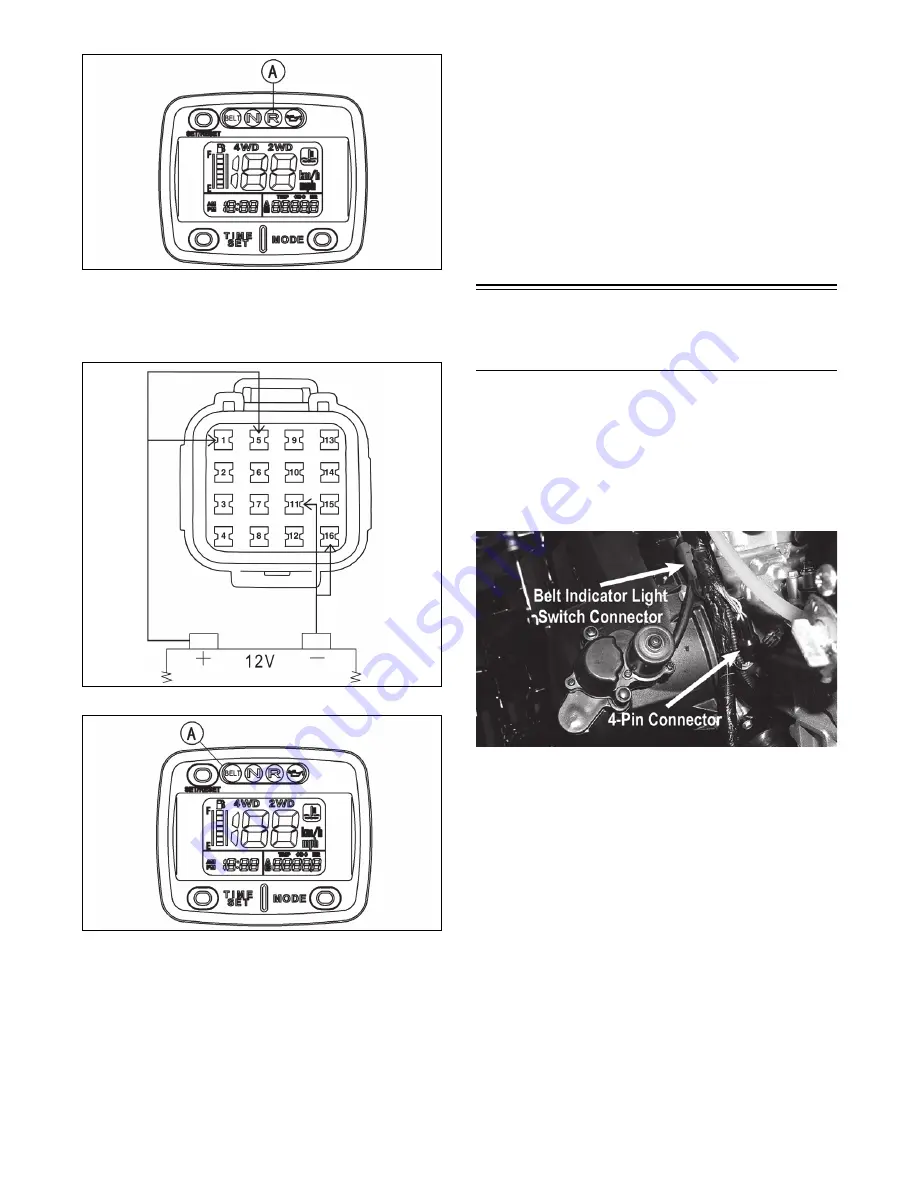
5-22
ATV2140
17. Connect a jumper wire from the negative battery
terminal to terminal (11) in the connector. The belt
indicator light (A) should illuminate.
ATV2208K
ATV2142
INSTALLING
1. Route the new wiring harness down through the
opening; then place the speedometer into position
and secure with the three nuts. Connect the
multi-pin connector.
2. Install the front fenders and front rack; then install
the instrument pod and secure with the nylon fas-
teners.
3. Secure the ignition switch with the retaining nut.
V-Belt Failure Mode
Clearing
PROCEDURE
NOTE: See Section 2 for V-belt inspection.
1. Turn the ignition switch to the OFF position; then
disconnect the 4-pin connector and the belt indica-
tor light switch connector.
KX098A
2. Install the Reset Connector (p/n 0486-161) into the
forward 4-pin connector; then turn the ignition
switch to ON. Allow the belt indicator light to
flash for 10 seconds or more; then turn the ignition
switch to OFF.
NOTE: The light will flash rapidly for 5 seconds;
then it will flash slowly. Allow the light to flash
slowly for at least 5 seconds before turning the
ignition switch off.
3. Remove the reset connector and connect the 4-pin
connectors and the belt indicator light switch
connector.
4. Turn the ignition switch to the ON position and
confirm that the belt indicator light goes off.
Summary of Contents for 650 Twin2004
Page 1: ...ATV Service Manual 2004 2004 A A RC C C T T I 650 Twin...
Page 9: ...1 6 NOTES...
Page 83: ...3 54 NOTES...
Page 128: ...Wiring Diagram Harness p n 0486 147 739 259A 5 27...
Page 156: ...6 28 NOTES...
Page 184: ...8 18 NOTES...
Page 194: ...9 10 NOTES...
Page 198: ...10 4 NOTES...