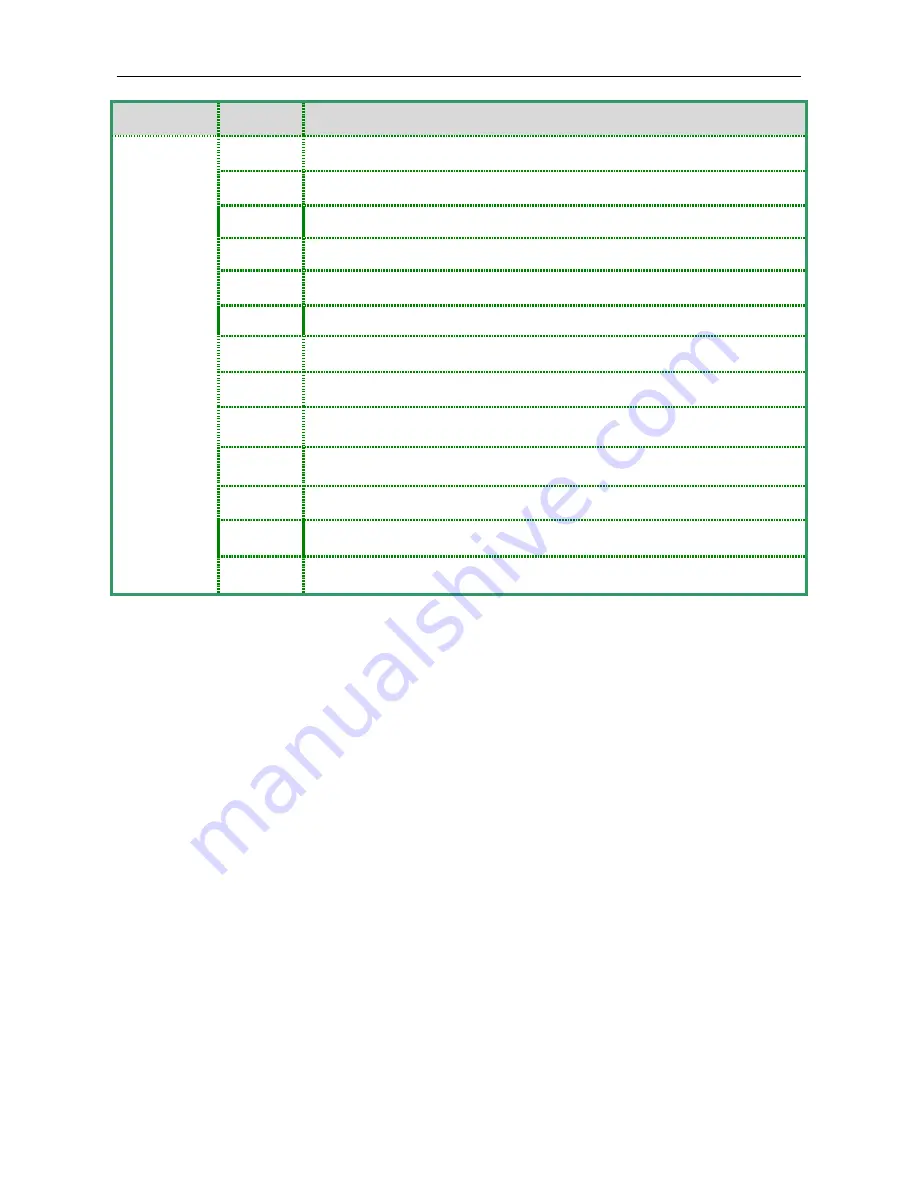
FST 500 Manual
- Page 94 -
Content
Address
Functions
Status
monitor
Read only
2104H
Output Current A (XXX.X)
2105H
DC-BUS Voltage U (XXX.X)
2106H
Output Voltage E (XXX.X)
2107H
Step number of Multi-Step Speed Operation (step)
2108H
Time of PLC Operation (sec)
2109H
Value of External Trigger (count)
210AH
The Correspondent Value of Power Factor (XXX.X)
210BH
Pr.65 X Low word of H (XXX.XX)
210CH
Pr.65 X High word of H (XXX.XX)
210DH
AC Drive Temperature (XXX.X)
210EH
PID Feedback Signal (XXX.XX)
210FH
PID Target Value (XXX.XX)
2110H
AC Drive Mode Type Information
3.7 Communication program of PC:
The following is a simple example of how to write a communication program for Modbus ASCII mode
on a PC by C language.
#include<stdio.h>
#include<dos.h>
#include<conio.h>
#include<process.h>
#define PORT 0x03F8 /* the address of COM1 */
/* the address offset value relative to COM1 */
#define THR 0x0000
#define RDR 0x0000
#define BRDL 0x0000
#define IER 0x0001
#define BRDH 0x0001
#define LCR 0x0003
#define MCR 0x0004
#define LSR 0x0005
#define MSR 0x0006
unsigned char rdat[60];
/* read 2 data from address 2102H of AC drive with address 1 */
unsigned ch
ar tdat[60]={':','0','1','0','3','2','1','0',‟2', '0','0','0','2','D','7','\r','\n'};
Summary of Contents for FST-500 Series
Page 8: ...FST 500 Manual Page 8 1 1 3 External Parts and Labels...
Page 9: ...FST 500 Manual Page 9 1 1 4 Remove instructions...
Page 17: ...FST 500 Manual Page 17...
Page 22: ...FST 500 Manual Page 22 2 4 Control Terminal Wiring Factory Settings...
Page 27: ...FST 500 Manual Page 27 3 1 2 How to Operate the Digital Keypad LC M02E...
Page 49: ...FST 500 Manual Page 49 Commonly used V F Setting 1 General Purpose...
Page 110: ...FST 500 Manual Page 110 Chapter 5 Troubleshooting 5 1 Over Current OC...
Page 111: ...FST 500 Manual Page 111 5 2 Ground Fault 5 3 Over Voltage OV...
Page 112: ...FST 500 Manual Page 112 5 4 Low Voltage Lv...
Page 113: ...FST 500 Manual Page 113 5 5 Over Heat OH1 5 6 Overload...
Page 114: ...FST 500 Manual Page 114 5 7 Keypad Display is Abnormal 5 8 Phase Loss PHL...
Page 115: ...FST 500 Manual Page 115 5 9 Motor cannot Run...
Page 116: ...FST 500 Manual Page 116 5 10 Motor Speed cannot be Changed...
Page 134: ...FST 500 Manual Page 134...
Page 135: ...FST 500 Manual Page 135...
Page 145: ...FST 500 Manual Page 145 EMI Filter 40TDS4W4B Used on 5 7 5 HP 230V Three Phase Models...