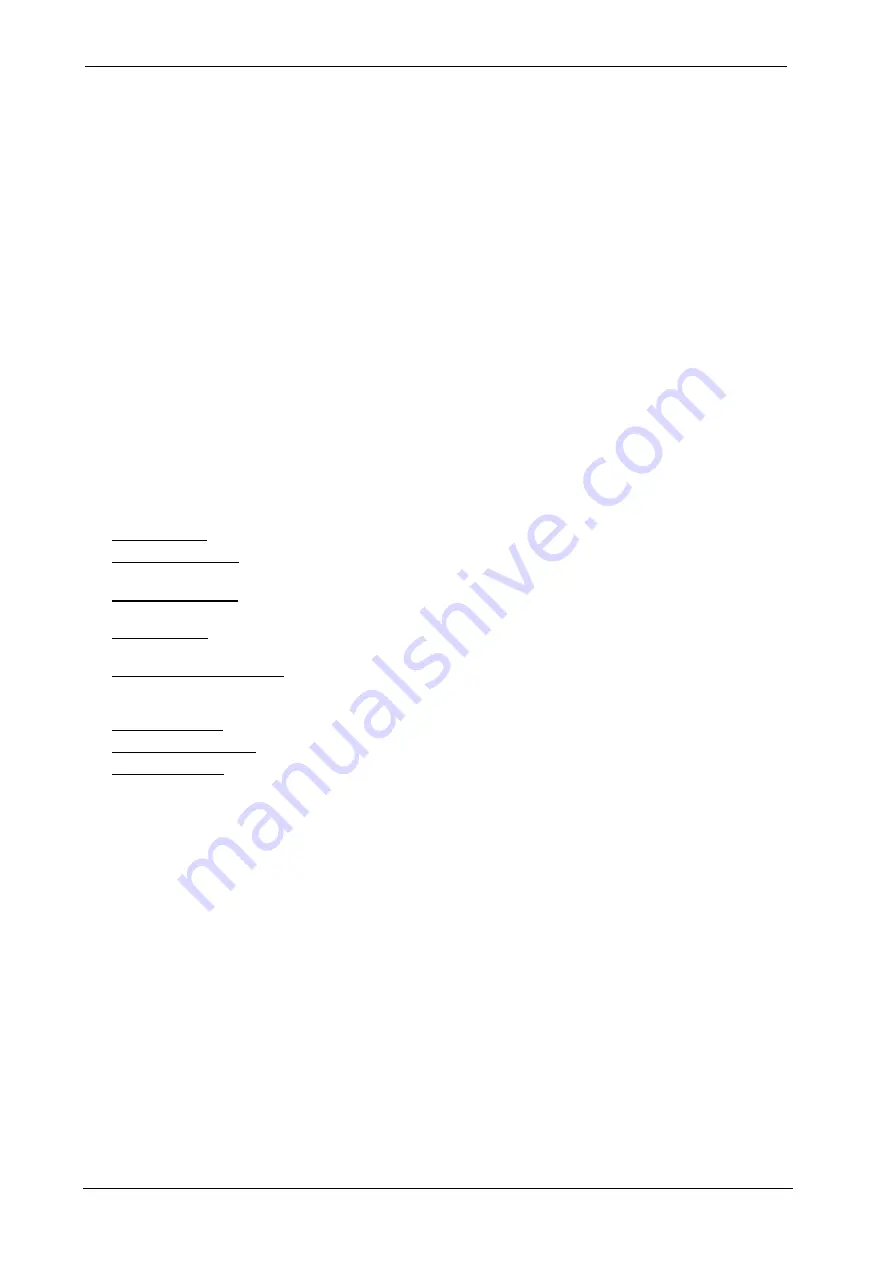
Application notes
54
IMGT30017EN
5A.2 Drive
selection
•
Base GT3000 size selection on drive rated current instead of drive power. The drive output current should be greater than the rated
current of the controlled motor.
•
If a single drive feeds multiple motors, select a GT3000 with an output current 10% higher than the sum of the motor currents.
Provide an independent hardware thermal protection for each motor; the internal software thermal protection of the drive is not
effective for multiple motor applications.
•
Vector control FOC cannot be used in applications with multiple motors in parallel. Use V/Hz or SLS control instead.
•
If the multiple motor application requires that some motors are disconnected and reconnected during drive operation, select a
GT3000 with a current rating suitable to handle the sum of the steady-state current of all connected motors plus the transient
starting current of the motor(s) that needs to be reconnected.
•
The starting and acceleration torque of a motor controlled by a drive is limited by the maximum drive current. Select an oversized
drive if high starting torque is required.
5A.3 Application
notes
•
If an application requires an output contactor, the contactor state should only be changed when the drive is disabled. The contactor
should be interlocked to the drive logic.
•
If the drive faults, the motor shaft spins freely. If this is not acceptable, a mechanical brake must be provided.
•
If the drive is fed by a generator set, verify that the generator can withstand the harmonic distortion produced by the drive.
•
The drive provides a DC braking option. Its use results in fairly high motor temperatures. If frequent use of this function is required,
verify the motor is sized appropriately, or contact the motor manufacturer.
5A.4 Applications with special motors
•
Motors with brake. The brake shall have independent power supply. When the brake is engaged, the drive must be disabled.
•
Motors with conic rotor. The brake is controlled by the magnetic motor field. If necessary, fit and adjust the boost. In some cases
it may be necessary to use a larger size drive.
•
Double winding motors. The drive output current shall be greater than the rated current of each motor winding. The winding can
only be switched when the motor is stopped and the drive is disabled.
•
Classified motors. The drive cannot be operated in environments where there are explosion or fire hazards. If the motor and drive
must be operated in such environments, both the drive and motor must be of the explosion-proof type.
•
Power transmission mechanism.
The lubrication system and rotation limits vary from manufacturer to manufacturer. With oil
lubrication, frequent operations at low speeds may cause overheating due to insufficient lubrication. Check with manufacturer for
extended low-speed operation.
•
Synchronous motors. It is advisable to provide an output reactor to compensate for insufficient inductance in the motor.
•
Submersible motor pumps. The rated current of these motors is higher than the standard.
•
Single phase motors. GT3000 drives are not designed to control single-phase motors.
5A.5 Motor selection
When selecting a motor, verify the following:
•
Natural resonance. Vibration can be minimized by using a flexible coupling or by placing a rubber shock absorber beneath the
motor base. With the drive it is possible to avoid critical frequencies.
•
GT3000 provides variable frequency control. Motors and loads must be capable of operation over the speed and power range
provided by the drive.
•
Noise. The noise of the motors increases compared to the operation with supply from the net (inverter commuting frequency
= 2kHz). The use of output reactors or of sinusoidal filters reduces or cancels the noise increase.
•
Protecting the motor winding and bearings
The output of the drive comprises – regardless of output frequency – pulses of approximately 1.35 times the mains network voltage
with a very short rise time.
This is the case with all drives employing modern IGBT inverter technology.
The voltage of the pulses can be almost double at the motor terminals, depending on the motor cable properties.
This in turn can cause additional stress on the motor insulation.
Modern variable speed drives with their fast rising voltage pulses and high switching frequencies can cause current pulses through
the motor bearings, which can gradually erode the bearing races.
The stress on motor insulation can be avoided by using optional du/dt filters. du/dt filters also reduce bearing currents.
To avoid damage to motor bearings, insulated N-end (non-driven end) bearings and output filters must be used according to the
table 5A. In addition, the cables must be selected and installed according to the instructions given in this manual.
Summary of Contents for GT3000
Page 1: ...GT3000 Hardware Software Manual www answerdrives com ...
Page 2: ......
Page 4: ......
Page 8: ...Table Of Contents GT3000 iv IMGT30017EN ...
Page 12: ...General Safety Precautions viii IMGT30017EN ...
Page 25: ...GT3000 Technical Data IMGT30017EN 13 Frames IV V VIN SVGT045 166 IP20 ...
Page 26: ...Technical Data GT3000 14 IMGT30017EN Frames IV V VIN SVGT045 166 IP54 ...
Page 28: ...Technical Data GT3000 16 IMGT30017EN Frames VII VIII IP00 SVGT200 521K SVGT200 470F ...
Page 29: ...GT3000 Technical Data IMGT30017EN 17 F series Frames 2xVII 2xVIII Parallel IP00 SVGT520 940M ...
Page 30: ...Technical Data GT3000 18 IMGT30017EN K series Frames 2xVII 2xVIII Parallel IP00 SVGT580 960K ...
Page 36: ...Installation GT3000 24 IMGT30017EN 3A 2 1 4 Frames VII VIII Installatiion ...
Page 58: ...GT3000 Installation 46 IMGT30004EN ...
Page 107: ...GT3000 Terminal Boards and Power Schematics IMGT30017EN 95 ...
Page 110: ...Terminal Boards and Power Schematics GT3000 98 IMGT30017EN ...