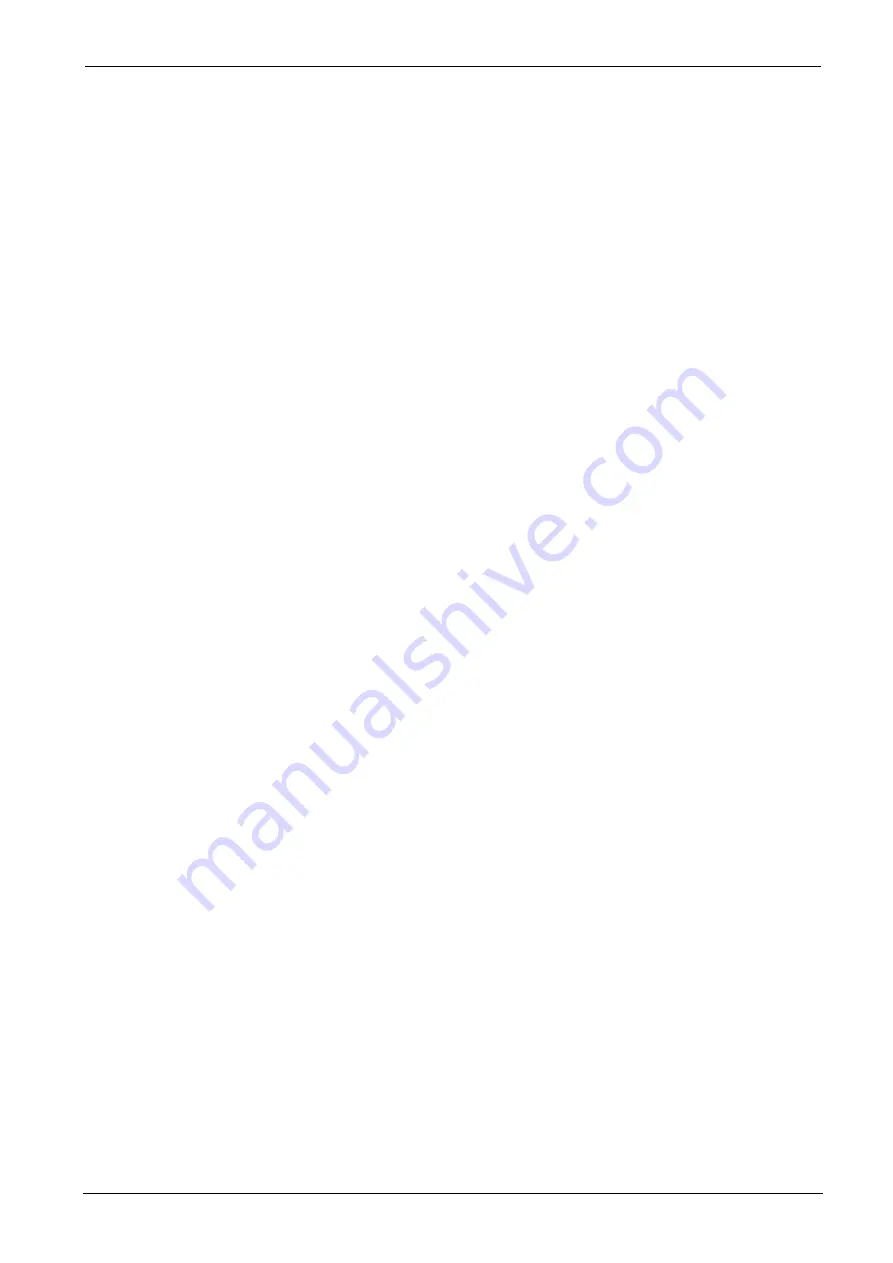
GT3000
Installation
104 IMGT30017EN
A2.1.3
Solutions to fulfill conducted emission requirements
Some basic principles have to be followed when designing and using drive systems incorporating AC drive products.
The emissions can be divided into two parts, the conducted emission and the radiated emission.
The disturbances can be emitted in various ways. Conducted disturbances can propagate to other equipment via all conductive parts including
cabling, earthing and the metal frame of an enclosure.
Conducted emission:
Can be reduced in the following way:
By RFI filtering for HF disturbances
Using sparking suppressors in relays, contactors, valves, etc. to attenuate switching sparks
Using ferrite rings in power connection points
Radiated emission:
To be able to avoid disturbance through air, all parts of the PDS should form a Faraday Cage against radiated
emissions. The PDS includes cabinets, auxiliary boxes, cabling, motors, etc. Some methods for ensuring the continuity
of the Faraday Cage are listed as follows:
Enclosure:
• The enclosure must have an unpainted non-corroding surface finish at every point that other plates, doors, etc. make contact.
• Unpainted metal to metal contacts shall be used throughout, with conductive gaskets, where appropriate.
• Use unpainted installation plates, bonded to common earth point, ensuring all separate metal items are firmly bonded to achieve a single path to
earth
• Use conductive gaskets in doors and covers. Covers should be secured at not more than 100 mm intervals where radiation could escape.
• Separate radiative i.e. “dirty” side from the “clean side” by metal covers and design.
• Holes in enclosure should be minimised.
• Use materials with good attenuation e.g. plastic with conductive coating, if a metal enclosure cannot be used.
Cabling & Wiring:
• For high frequency earthing of power cable shields, use special HF cable entries.
• Use conductive gaskets for HF earthing of control cable shield.
• Use shielded power and control cables.
• Route power and control cables separately.
• Use twisted pairs to avoid common mode disturbances.
• Use ferrite rings for common mode disturbances, if necessary.
• Select and route internal wires correctly.
Installation:
• Auxiliaries used with CDM’s should be CE marked products to both EMC & Low Voltage Directives, not only to LV directive, unless they are not
concerned, e.g. being with a component without a direct function.
• Selection and installation of accessories in accordance with manufacturers’ instructions
• 360° earthing at motor end.
• Correct internal wiring methods.
• Special attention must be given to earthing.
A2.2
RADIO FREQUENCY INTERFERENCE (RFI) FILTER
The EMC emission limits for PDS depend on the installation environment, type of power supply network and power of the drive.
RFI filters are used to attenuate conducted disturbances in a line connecting point where the filter leads the disturbances to earth.
RFI filters are needed when a PDS is connected to the public low-voltage network (First Environment).
It is also recommended to use filters in industrial situations (Second Environment), if there are potential victims in the neighbourhood and thus
possible EMC problems.
Installation of the RFI filter: Reliable HF/low impedance connections are essential to ensure proper functioning of the filter, therefore the following
instructions shall be followed.
• Filter shall be assembled on a metal plate with unpainted connection points all in accordance with filter manufacturer’s instructions.
• The frames of the filter cubicle (if separate) and the drive cubicle shall be bolted together at several points. Paint shall be removed from all
connection points.
• The input and output cables of the filter shall not run in parallel, and must be separated from each other.
• The maximum length of the cable between the filter and the drive must be shorter than 0.3m; do not obstruct the drive cooling intake. For longer
connections use a shielded cable only.
• The filter must be earthed using the designated filter ground terminal only. Note that the cable type and size are critical.
Relays, contactors and magnetic valves must be equipped with spark suppressors. This is also necessary when these parts are mounted outside the
frequency converter cubicle.
Summary of Contents for GT3000
Page 1: ...GT3000 Hardware Software Manual www answerdrives com ...
Page 2: ......
Page 4: ......
Page 8: ...Table Of Contents GT3000 iv IMGT30017EN ...
Page 12: ...General Safety Precautions viii IMGT30017EN ...
Page 25: ...GT3000 Technical Data IMGT30017EN 13 Frames IV V VIN SVGT045 166 IP20 ...
Page 26: ...Technical Data GT3000 14 IMGT30017EN Frames IV V VIN SVGT045 166 IP54 ...
Page 28: ...Technical Data GT3000 16 IMGT30017EN Frames VII VIII IP00 SVGT200 521K SVGT200 470F ...
Page 29: ...GT3000 Technical Data IMGT30017EN 17 F series Frames 2xVII 2xVIII Parallel IP00 SVGT520 940M ...
Page 30: ...Technical Data GT3000 18 IMGT30017EN K series Frames 2xVII 2xVIII Parallel IP00 SVGT580 960K ...
Page 36: ...Installation GT3000 24 IMGT30017EN 3A 2 1 4 Frames VII VIII Installatiion ...
Page 58: ...GT3000 Installation 46 IMGT30004EN ...
Page 107: ...GT3000 Terminal Boards and Power Schematics IMGT30017EN 95 ...
Page 110: ...Terminal Boards and Power Schematics GT3000 98 IMGT30017EN ...