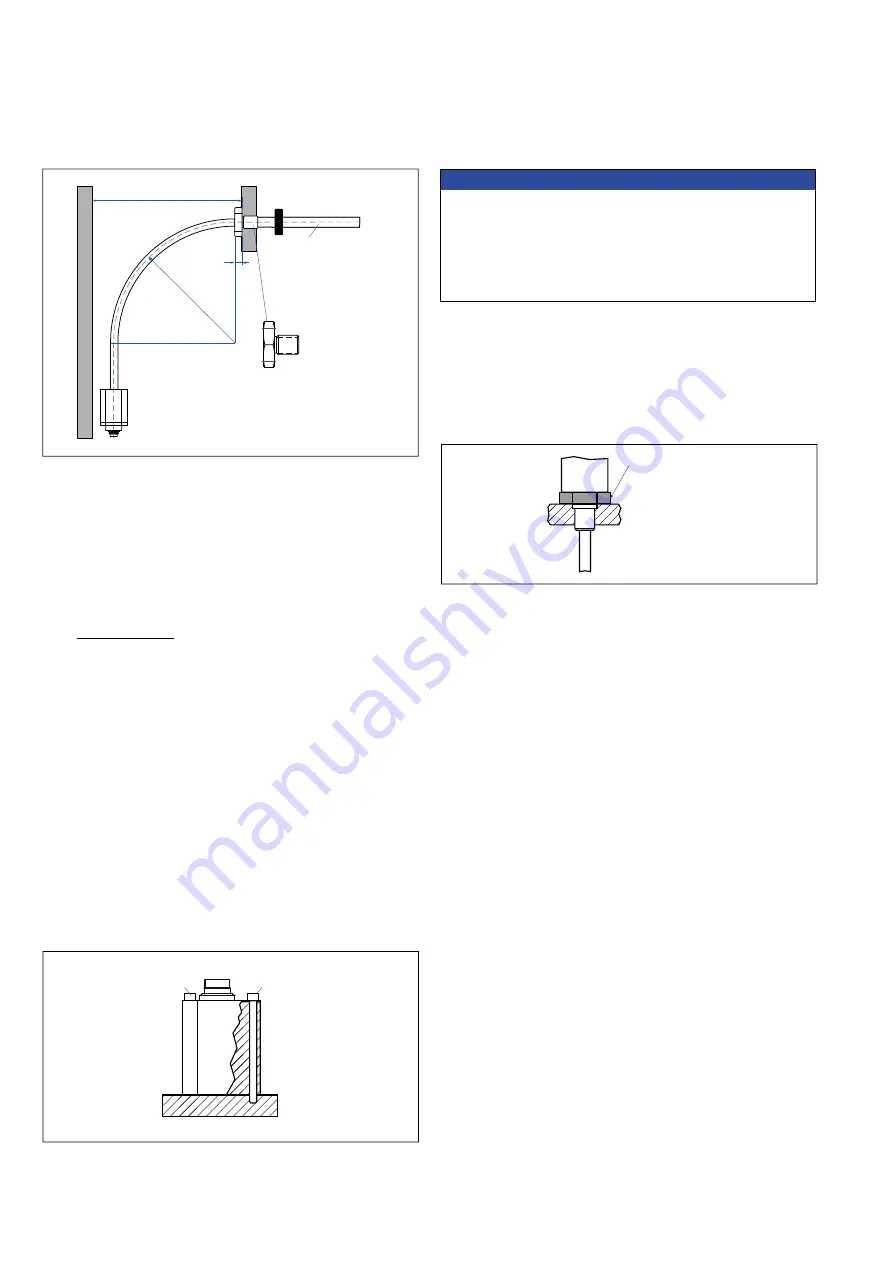
Temposonics
®
R-Series
V
Analog
Operation Manual
I 22 I
Mounting the RFV
1. RFV-B
• Insert the flexible sensor rod in a support tube.
• Mount the sensor electronics housing by means of 3 non-
magnetic socket head screws M4×59. Fastening torque: 1.4 Nm
(Fig. 16). Secure the screws, e.g. using Loctite 243, before re-
installing.
Recommendation: Seal the sensor via flange.
2. RFV-B with pressure rod HD/HL/HP or HFP profile (see
“Frequently ordered accessories”)
Advantage: The flexible sensor rod is inserted in a support tube.
• Mount the sensor electronics housing by means of 3 non-
magnetic socket head screws M4×59. Fastening torque: 1.4 Nm
(Fig. 16). Secure the screws, e.g. using Loctite 243, before re-
installing.
• Installation details: see below
3. RFV-M/-S
• Insert the flexible sensor rod in a support tube.
• Mount the sensor via flange.
• Installation details: see below
• Please note that liquid can enter the sensor between the thread
and the flexible rod.
Installation of RFV with threaded flange »M«, »S«
Fix the sensor rod via threaded flange M18×1.5-6g or ¾"-16 UNF-3A.
Note the fastening torque of
RFV-M: 65 Nm
RFV-S: 50 Nm
Installation of an RFV sensor with pressure rod HD/HL/HP in a fluid
cylinder
The rod-style version has been developed for direct stroke measure-
ment in a fluid cylinder. Mount the sensor via threaded flange or a hex
nut.
• Mounted on the face of the piston, the position magnet travels over
the rod without touching it and indicates the exact position through
the rod wall – independent of the hydraulic fluid.
• The pressure resistant sensor rod is installed into a bore in the
piston rod.
• The base unit is mounted by means of only 3 screws. It is the
only part that needs to be replaced if servicing is required, i.e. the
hydraulic circuit remains closed. For more information see chapter
“4.7 Replacement of base unit” on page 34.
• Note the fastening torque of
HD:
65 Nm
HL:
50 Nm
HP:
55 Nm
• Seat the flange contact surface completely on the cylinder mounting
surface.
• The cylinder manufacturer determines the pressure-resistant gasket
(copper gasket, O-ring, etc.).
• The position magnet should not grind on the sensor rod.
• The piston rod drilling for RFV sensors with pressure rod (outer
diameter 12.7 mm (0.5 in.)) is ≥ 16 mm (≥ 0.63 in.). The borehole
depends on the pressure and piston speed.
• Adhere to the information relating to operating pressure.
• Protect the sensor rod against wear.
500 (20) recommended
≥ 300 (≥ 11.81)
Position magnet
10
(0.4)
A/F 46
Flange M18×1.5-6g
¾"-16 UNF-3A
Customized support tube
required e.g. Ø 12.7 × 1.65
(Ø 0.5 × 0.65),
inside Ø 9.4 (Ø 0.37),
non-magnetic
R > 250
(R > 9.84)
Fastening torque:
RFV-M: 65 Nm
RFV-S: 50 Nm
HD: 65 Nm
HL: 50 Nm
HP: 55 Nm
Socket head screw
M4×59
Socket head screw
M4×59
Fastening torque of socket head screw M4×59: 1.4 Nm
Fig. 15: Clearances for installation and handling
Fig. 16: Mounting with socket head screws M4×59
Fig. 17: Mounting example of threaded flange
NOTICE
To fulfill the requirements of EMC standards for emission and
immunity the following points are necessary:
• The sensor electronics housing has to be connected to machine
ground (Fig. 45).
• Embed the flexible sensor element in an appropriately shielded
environment, e.g. in a pressure rod HD/HL/HP.
Controlling design dimensions are in millimeters and measurements in ( ) are in inches