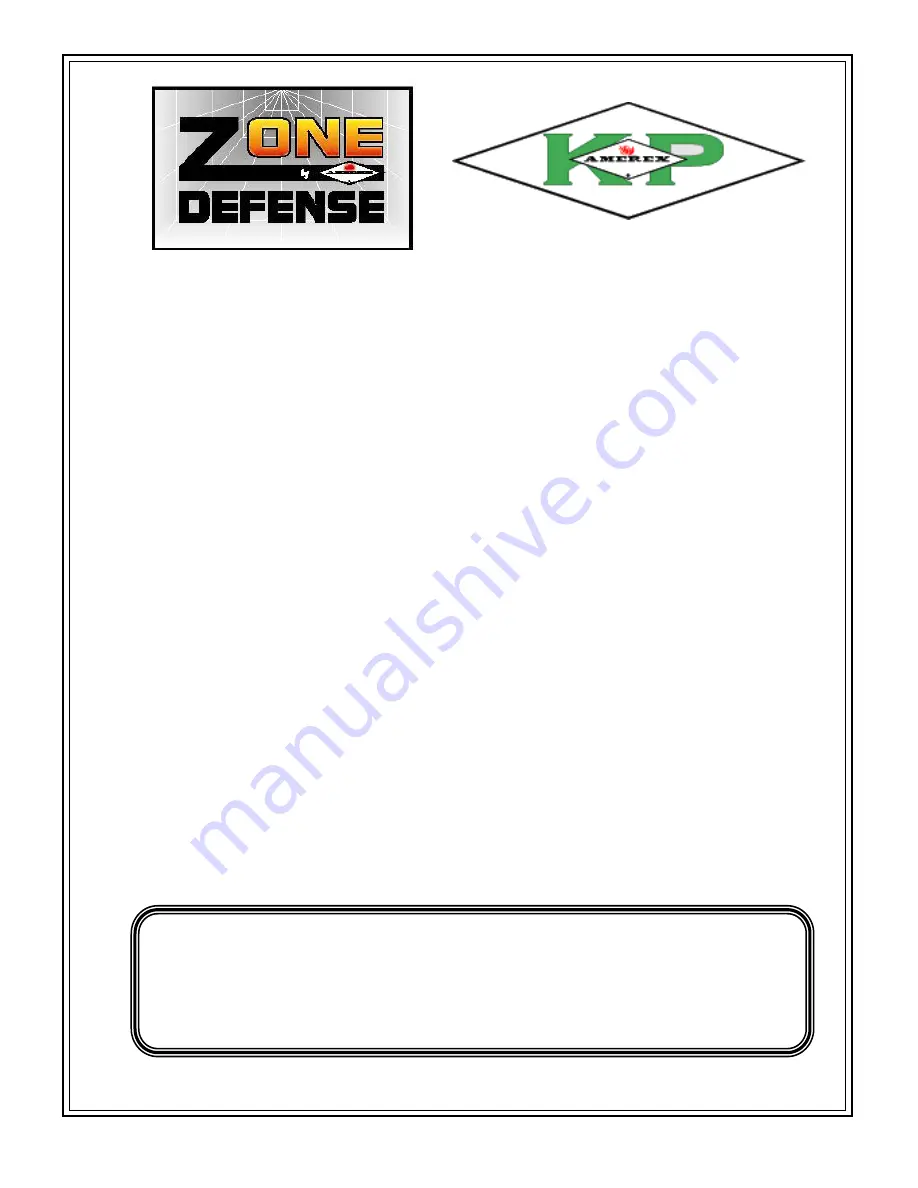
DESIGN, INSTALLATION,
MAINTENANCE & RECHARGE
MANUAL
NO. 20150
AMEREX
RESTAURANT
FIRE SUPPRESSION SYSTEM
TESTED AND LISTED BY
UNDERWRITERS LABORATORIES
TO UL STANDARD 300
and
UNDERWRITERS LABORATORIES OF
CANADA ULC/ORD 1254.6-1995
*
AMEREX CORPORATION
Post Office Box 81
Trussville, Alabama 35173-0081
Phone: (205) 655-3271
Fax: (205) 655-5112
e-mail: sales @amerex-fire.com web page: www.amerex-fire.com
Printed in U.S.A.
December 2008
(rev. February 14, 2019)
MM#20150-9/2014
No part of this manual may be reproduced or transmitted in any form or by any means electrical or
mechanical, including photocopying or by any storage and retrieval system without the expressed
permission in writing from Amerex Corporation.
A Factory Trained and Authorized Distributor must perform the installation and service of any
Amerex Restaurant Fire Suppression System in strict accordance with this manual.
*
ULC Certification does not apply to the STRIKE
TM
or SRM.