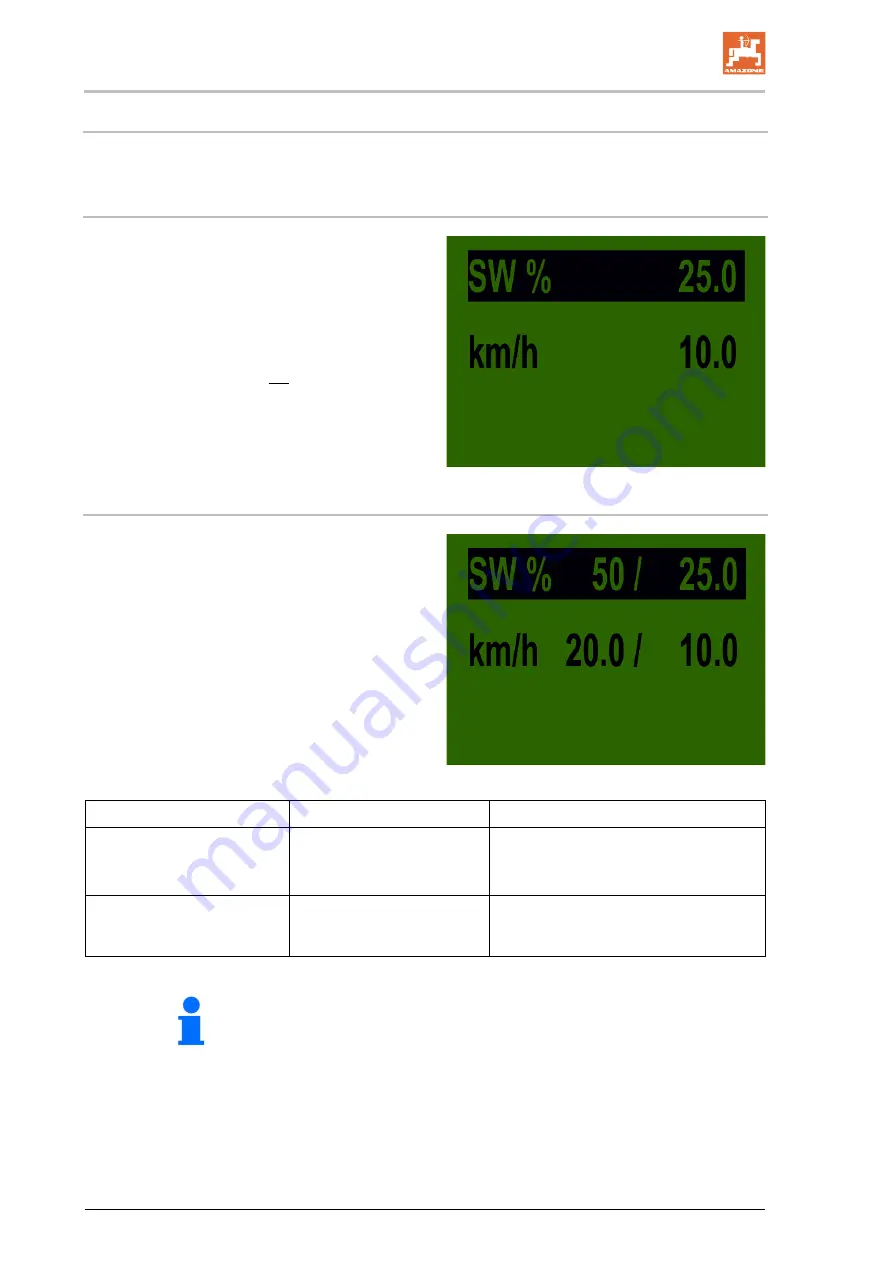
GreenDrill control terminal 5.2
54
GreenDrill BAH0108-0 03.20
6.3
Main menu
6.3.1
During operation - Display without speed sensor
Line 1 in the main menu shows
the seeding shaft speed [%] set during calibration.
Line 2 in the main menu shows
the forward speed [km/h] set for calibration.
The seeding shaft speed is not adjusted for
changing forward speeds. Always maintain the
indicated forward speed [km/h] during operation.
6.3.2
During operation - Display with speed sensor
Line 1 in the Main menu shows
the seeding shaft speed [%]
Setpoint
50 %
Actual value
25 %
Line 2 in the main menu shows the forward
speed [km/h]
Setpoint
20 km/h
Actual value 10 km/h
Display
Setpoint
Actual value
Seeding shaft speed [%]
The target seeding shaft
speed is calculated during
the calibration test
The actual seeding shaft speed is
calculated according to the forward
speed and is shown in the main menu.
Forward speed [km/h]
The target forward speed is
set in the "Calibration"
submenu
The actual forward speed [km/h] is
measured using the speed sensor and
is shown in the main menu.
The current seeding shaft speed should not undercut the 10%
displayed value to prevent deviations in the spread rate.
Summary of Contents for GreenDrill GD200-E
Page 2: ......
Page 32: ...Structure and function 32 GreenDrill BAH0108 0 03 20 4 1 1 6 Seed metering wheel table ...
Page 105: ......