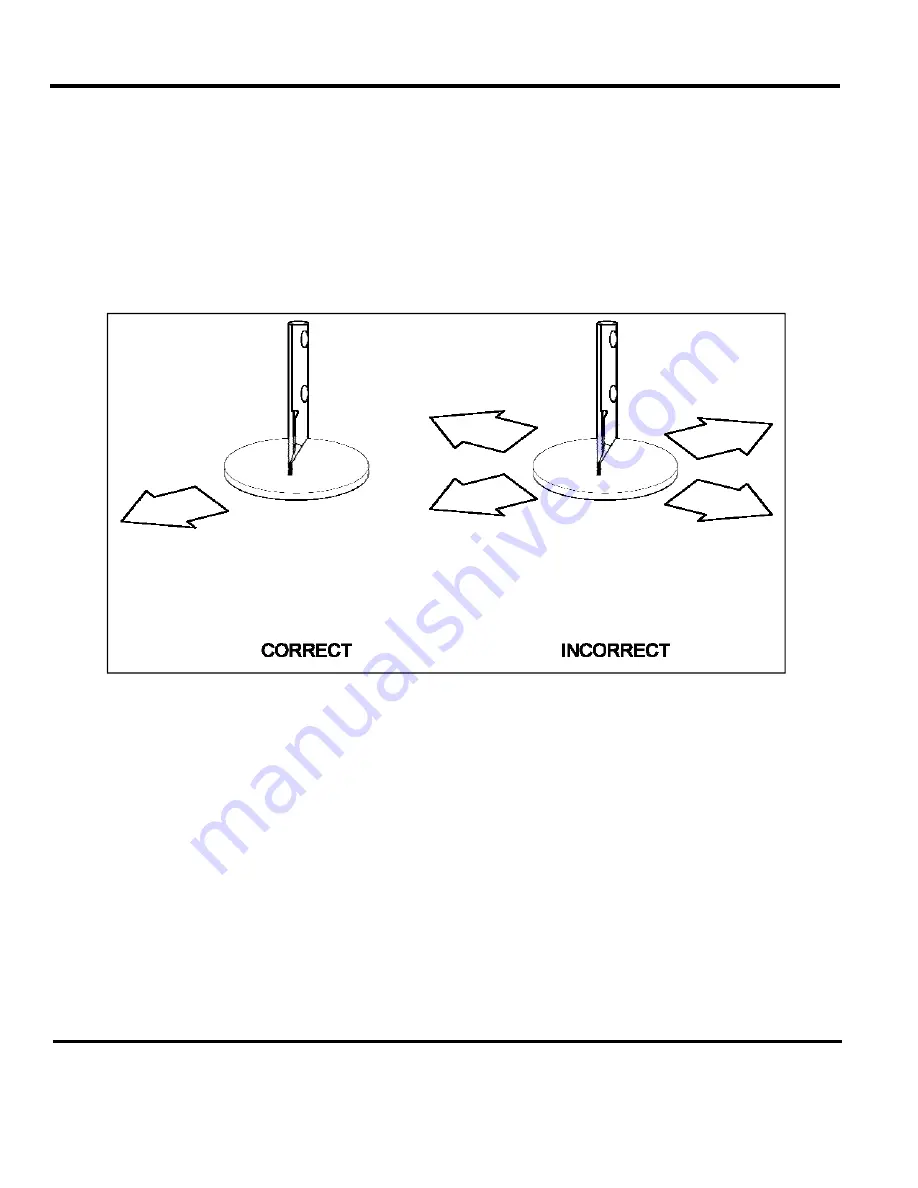
CHAPTER 4: SERVICE
SERIES 300 FAST RESPONSE WELD HEAD SYSTEM
4-4
990-115
Section III: Operator Service Procedures
Electrode Maintenance
When a welding schedule has been suitable for a particular welding application over many welds, but poor
quality welds are now resulting, electrode deterioration could be the problem. If you are needing to increase
weld current to maintain the same welding quality, the electrode tip has probably increased in surface area
(that is, mushroomed) , effectively increasing weld resistance. Try replacing the electrode.
The rough surface of a worn electrode tip tends to stick to the workpieces. So, periodic tip resurfacing
(dressing) is required to remove pitting, oxides and welding debris from the electrode. You should limit
cleaning of an electrode tip on the production line to using a #400-600 grit electrode polishing disk.
If you must clean a badly damaged tip with a file, be sure that the electrode surfaces are maintained parallel,
and use a polishing disk after filing to ensure that the electrode tip faces are smooth.
The best method of preventing electrode problems is to regularly re-grind electrode tip surfaces and shapes
in a certified machine shop.
Figure 4-1. Electrode Tip Surface Maintenance
Summary of Contents for 300 Series
Page 1: ...990 115 REV Q ELECTRONIC WELD HEAD CONTROL 300 Series OPERATION MANUAL ...
Page 8: ...SERIES 300 FAST RESPONSE WELD HEAD SYSTEM viii 990 115 ...
Page 32: ......
Page 62: ......
Page 78: ......