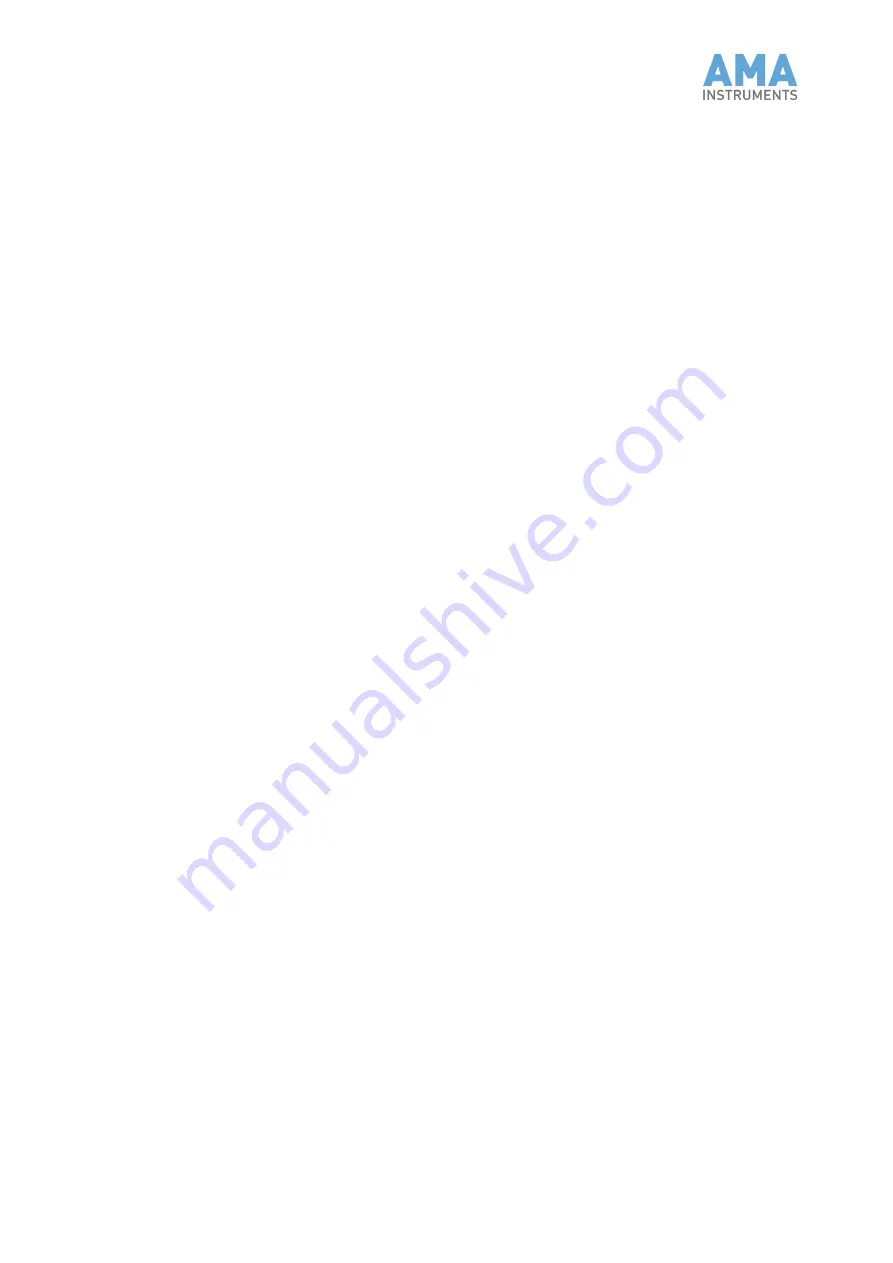
Operating Manual GC 5000 BTX; Version 5 – 11/2010
3
Page
11.0
Software reference continuing
11.3.10
Analog output configuration………………………………………………………… 85
11.3.11
Alarm configuration…………………………………………………..…..………….. 86
11.3.12
CP Analysis…………………………………………………………………………… 87
11.3.13
CP File Editor……………….……………………………………………………...... 88
11.3.14
Module setup………………..……………………………………………………...... 97
11.4
Program steps……………………………………………………………………….. 98
11.4.1
Standard BTX …………………………………………………………………………98
11.4.2
BTX with stripper Column ………………………………………………………….. 101
11.5
View…………………………..……………………………………………………….. 104
11.6
Run calibration (manual and auto-calibration)……………………………………. 107
11.7
Run validation ……………………………………………………………………….. 109
11.8
Help
functions …………….………………………………………………………… 110
11.8.1
Remote support….………….………………………………………………………. 110
11.8.2
About (current Software Version)………………………………………………….. 110
12.0
Miscellaneous procedures ……………………………………………………… 111
12.1
Programming and editing values ………………………………………………….. 111
12.2
Programming GC oven parameters …………………………………………….. 112
12.2.1
How to display the running temperature program …………..…………………… 112
12.2.2
Select the parameters for the running temperature program ………………….. 113
12.3
Start and stop ……………………………………………………………………… 114
12.4
Subsequent data processing………………..……………………………………… 116
13.0
Maintenance ………………………………………………………………………. 119
13.1
Security instructions ………………………………………………………………… 119
13.2
Maintenance schedule ……………………………………………………………… 120
13.3
Maintenance work ……………………………………………………………….. 121
13.3.1
Exchange the enrichment tube …………………………………………………….. 121
13.3.2
Maintenance of the pump ………………………………………………………….. 122
13.3.3
Exchange the input filter of the MFC ……………………………………………… 122
13.3.4
Exchange or repair the capillary column ………………………………............... 123
13.3.5
Adjust the detector signal ………………………………………………………….. 125
13.3.6
Check the glow plug ………………………………………………………………… 125
13.3.7
Check the thermocouples ………………………………………………………….. 126
13.3.8
Check the heating units of detector and valve oven ……………………………. 126
13.3.9
Exchange of the PID lamp ………………………………………………............... 127
13.3.10
Clean the PID lamp window ………………………………….……………………. 128
13.3.11
Exchange the rotor of the rotary valve …………………………………………… 128
13.3.12
Exchange the GC oven motor …………………………………………………….. 130
13.3.13
Exchange the back panel fan ……………………………………………..………. 130
13.3.14
Exchange the Peltier cooler fan …………………………………………………… 131
13.3.15
FID maintenance …………………………………………………………............... 131
14.0
Troubleshooting …………………………………………………………………. 132
14.1
General faults ……………………………………………………………………… 132
14.2
Alarm messages …………………………………………………………………….. 134
14.3
Warning messages………………………………………………………………… 136
14.4
Error messages ..……………………………………………………………………. 139
15.0
Spare parts list ……………………………………………………………………. 140
Summary of Contents for The GC 5000 BTX
Page 1: ...Operating Manual Gas chromatograph GC 5000 BTX...
Page 35: ...Operating Manual GC 5000 BTX Version 5 11 2010 33 Fig 5 Connection of analog outputs...
Page 102: ...Operating Manual GC 5000 BTX Version 5 11 2010 100 Injection Waiting for end of cycle time...
Page 105: ...Operating Manual GC 5000 BTX Version 5 11 2010 103 Injection Waiting for end of cycle time...