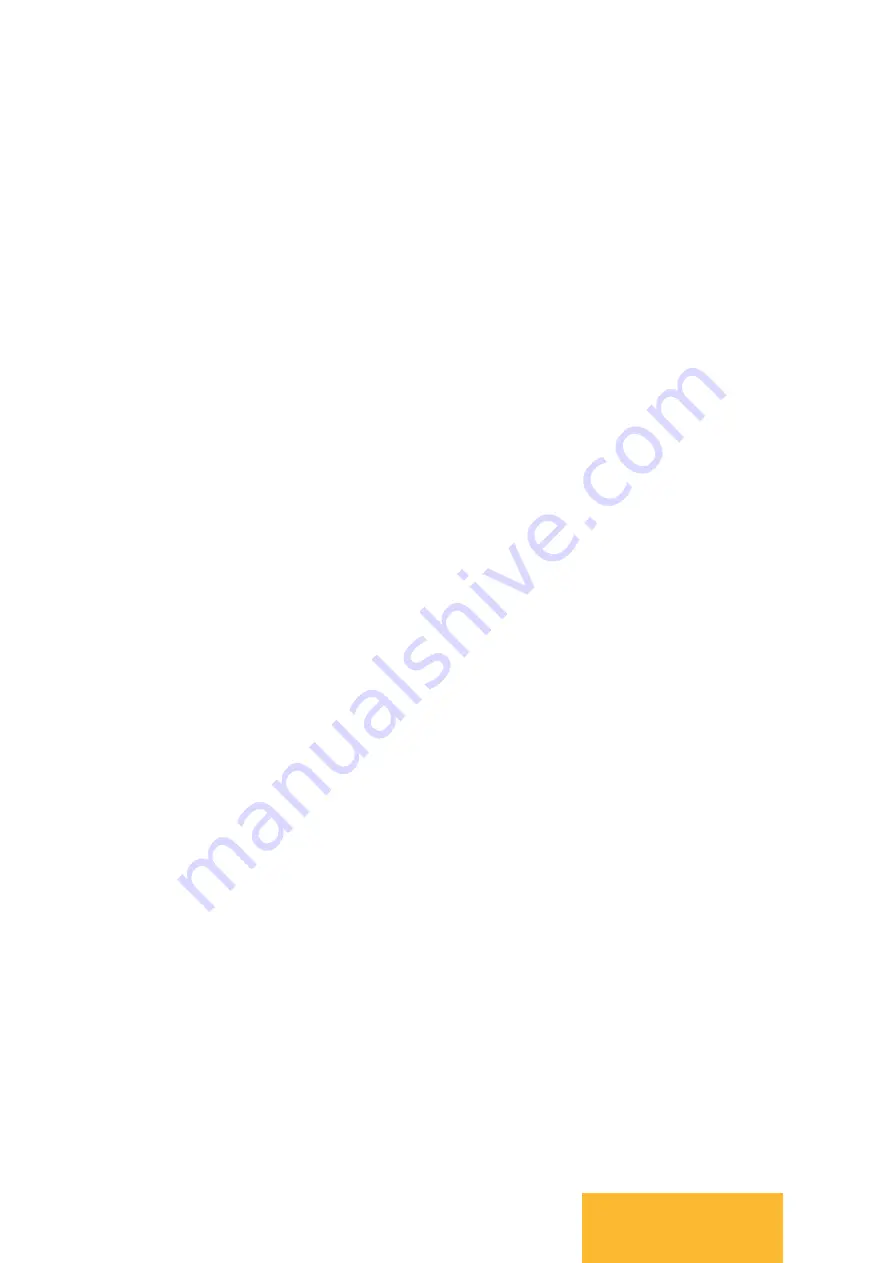
78
CHAPTER 6
HIGH VOLTAGE BATTERY
& DRIVE SYSTEM
The HV battery and drive system operate up to 400V
DC. The system can be “live” while the vehicle is
powered on and for up several minutes after the
vehicle is powered off.
Never assume that a connector or electrical
component is safe to handle; use a 600V-rated
multimeter to check the potential between HV
connector terminals, and between each terminal
and bare metal on the vehicle chassis or battery to
ensure that they are not “hot.” Any potential above
60V should be considered dangerous high voltage
and should not be handled without appropriate high
voltage safety gear and extreme caution. Contact
Alta Motors for further instructions.
Make sure that the run/stop switch is set to the “stop”
position before separating connectors or starting
disassembly. When the EV drive system is partially
disassembled, do not attempt to connect to AC or a
charger, and do not attempt to operate the vehicle.
It may be necessary to turn on the vehicle’s 12V
system to assist with diagnosis; be careful of loose
connections or metal parts that could cause a short
circuit and damage components.
The HV battery pack is always energized and should
not be opened for any reason. If the pack appears
physically damaged or the outer surface is breached,
contact Alta Motors immediately for handling
instructions. Please be able to provide images of the
damage in question.
Authorized Alta Motors service personnel are
authorized to disconnect the orange HV connectors
and the 3 motor lead ring terminal connections
inside the inverter. They are not authorized to make
or break any other HV electrical connections or to
open any other HV drive system components.
Before re-connecting HV drive system components,
inspect both ends of each HV connector for signs of
heat damage, bent terminals, or damaged plating,
dirt, grease, water, or any other debris. Compressed
air and isopropyl alcohol may be used to clean
connectors; allow them to dry completely before
reconnecting. If terminal plating is damaged or signs
of heat damage are present, leave the connector
unmated, and contact Alta Motors.
Whenever servicing electrical control system
components on the Redshift, wear a ground strap
on your wrist, and connect it to a ground on the
bike. Failure to do so could result in static electricity
discharge damage to the components.