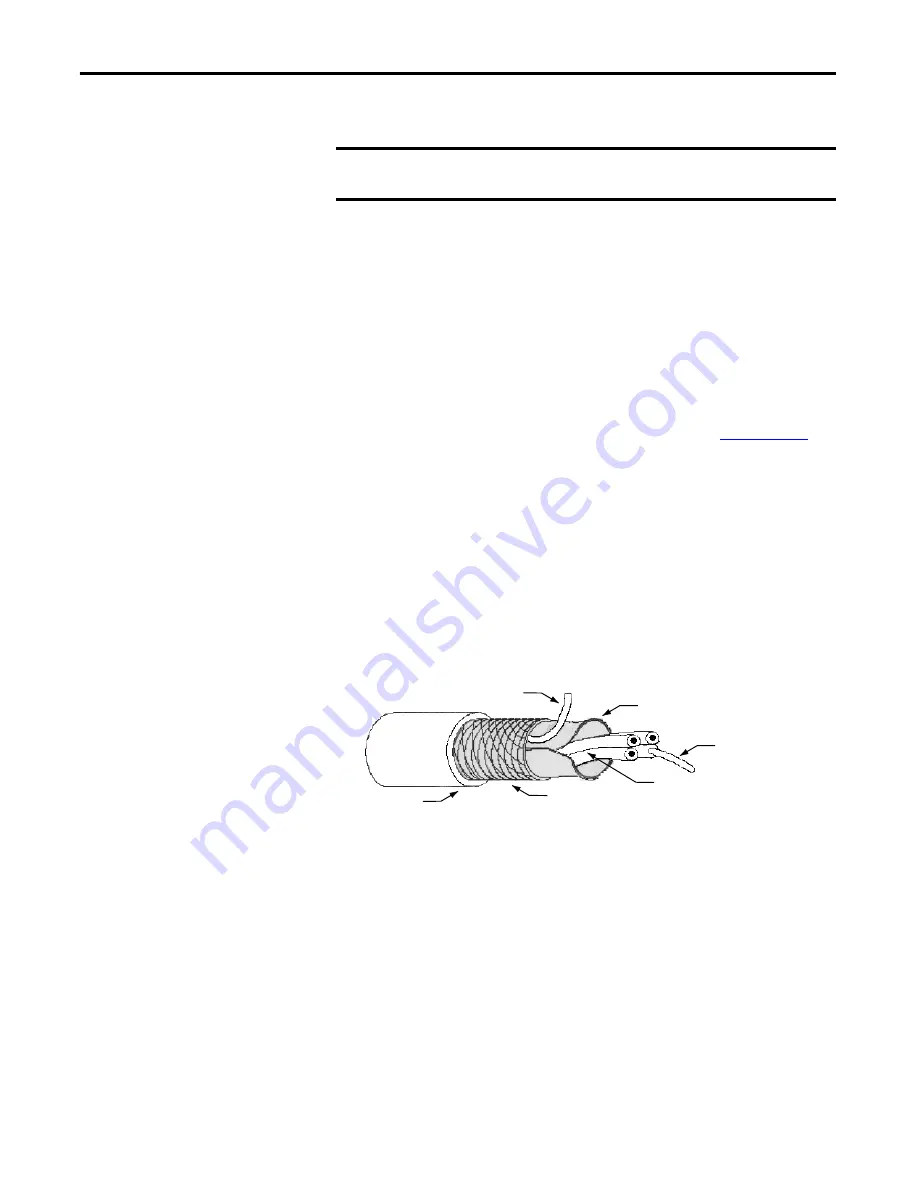
72
Rockwell Automation Publication 2099-UM001D-EN-P - December 2012
Chapter 4
Connect the Kinetix 7000 Drive System
Building Your Own Motor Cables
•
Connect the cable shield to the connector shells on both ends of the cable
with a complete 360° connection. If separate power wires are used in a
customer-supplied power cable, the shield may alternatively be connected
to a ground terminal.
•
Use a twisted pair cable whenever possible. Twist differential signals with
each other and twist single-ended signals with the appropriate ground
return.
•
Discrete power cables require 360° shielding. Connect the shield to a
ground terminal.
See the Kinetix Motion Control Selection Guide, publication
low-profile connector kit, drive-end (mating) connector kit, and motor-end
connector kit catalog numbers.
Shielded Motor Cable
The use of a four-wire type Variable Frequency Drive (VFD), 600 volt, UL listed
cable is strongly recommended for all motor currents at or below 130 Amperes.
The illustration below illustrates the type of cable required.
Figure 43 - Type of Cable Required for Kinetix 7000 Drive Interconnects
Required Cable Types
You should always use shielded motor cable. The shield must connect to the drive
chassis (PE) connection and the motor frame. Make the connection at both ends
to minimize the external magnetic field. If you use cable trays or large conduits to
distribute the motor leads for multiple drives, use shielded cable to reduce noise
from the motor leads.
IMPORTANT
Factory-made cables are designed to minimize EMI and are recommended
over hand-built cables to optimize system performance.
Stranded Drain Wire
Foil Shield
Oversized Insulation
Cable Jacket
Stranded Tinned Copper
Conductors
Tinned Copper Braid
with 85% Coverage