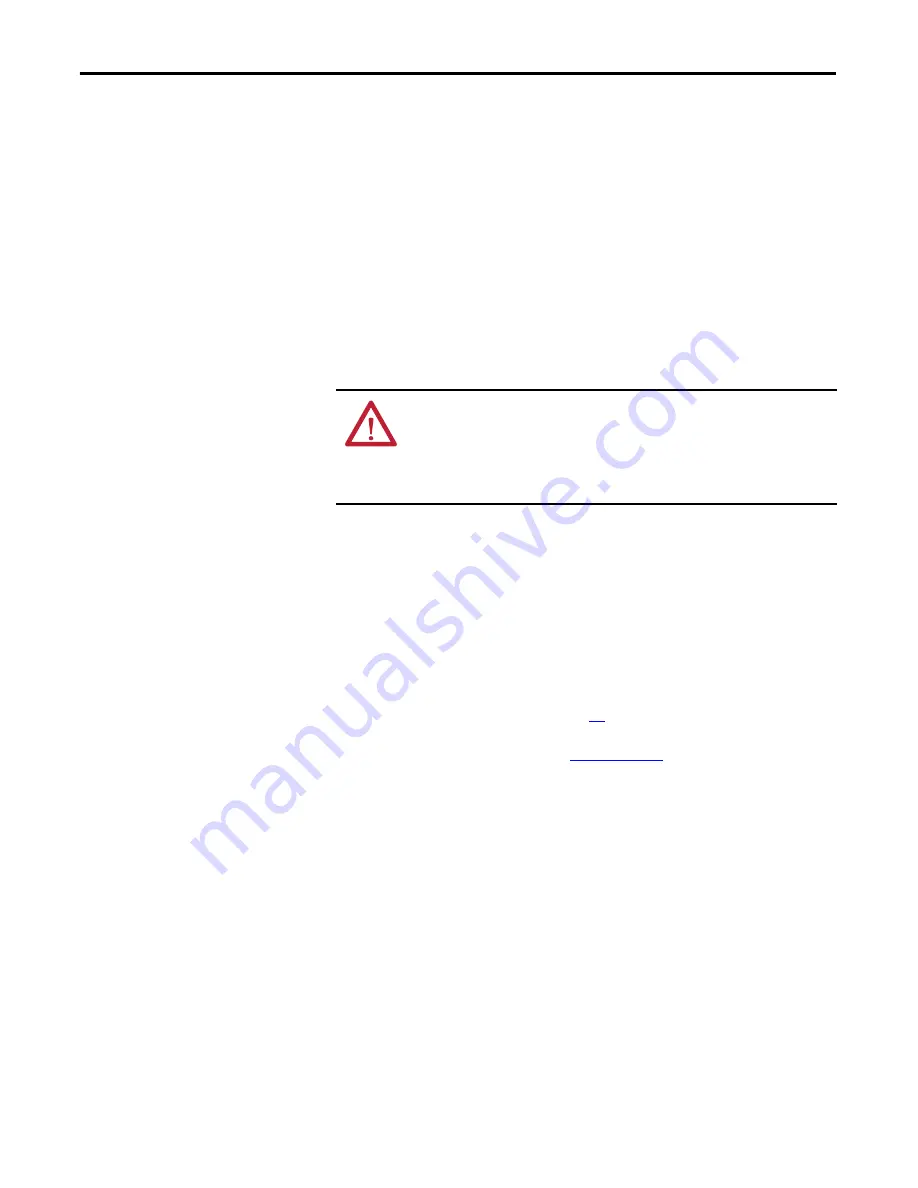
74
Rockwell Automation Publication 2099-UM001D-EN-P - December 2012
Chapter 4
Connect the Kinetix 7000 Drive System
General Wire Guidelines
Observe all applicable safety and national and local regulations when selecting
the appropriate wire size for your system. Due to the drive overload capacity of
150% of the continuous current rating, the conductors for the transformer
primary and secondary must be sized (at a minimum) for 125…160% of the
maximum continuous input current for the motor selected. The motor
conductors must also be rated for a minimum of 125…160% of the full load
motor continuous current. If less than 150% overload is required the torque limit
parameters must be set in the drive accordingly. The distance between the drive
and motor may affect the size of the conductors used. To protect against
interference, use shielded wire in motor and control circuits. A shielded cable is
required for all feedback signal wires.
Routing the Power and Signal Cables
Be aware that when you route power and signal wiring on a machine or system,
radiated noise from nearby relays, transformers, and other electronic drives can be
induced into motor or encoder feedback signals, input/output communications,
or other sensitive low voltage signals. This can cause system faults and
communication problems.
See Minimizing Electrical Noise on page
for examples of routing high and low
voltage cables in wireways, and to the System Design for Control of Electrical
Noise Reference Manual, publication
, for more information.
ATTENTION:
To avoid a possible shock hazard caused by induced voltages,
ground unused wires in the conduit at both ends.
For the same reason, if a drive sharing a conduit is being serviced or installed,
disable all drives using this conduit. This removes the possible shock hazard from
cross-coupled drive motor leads.