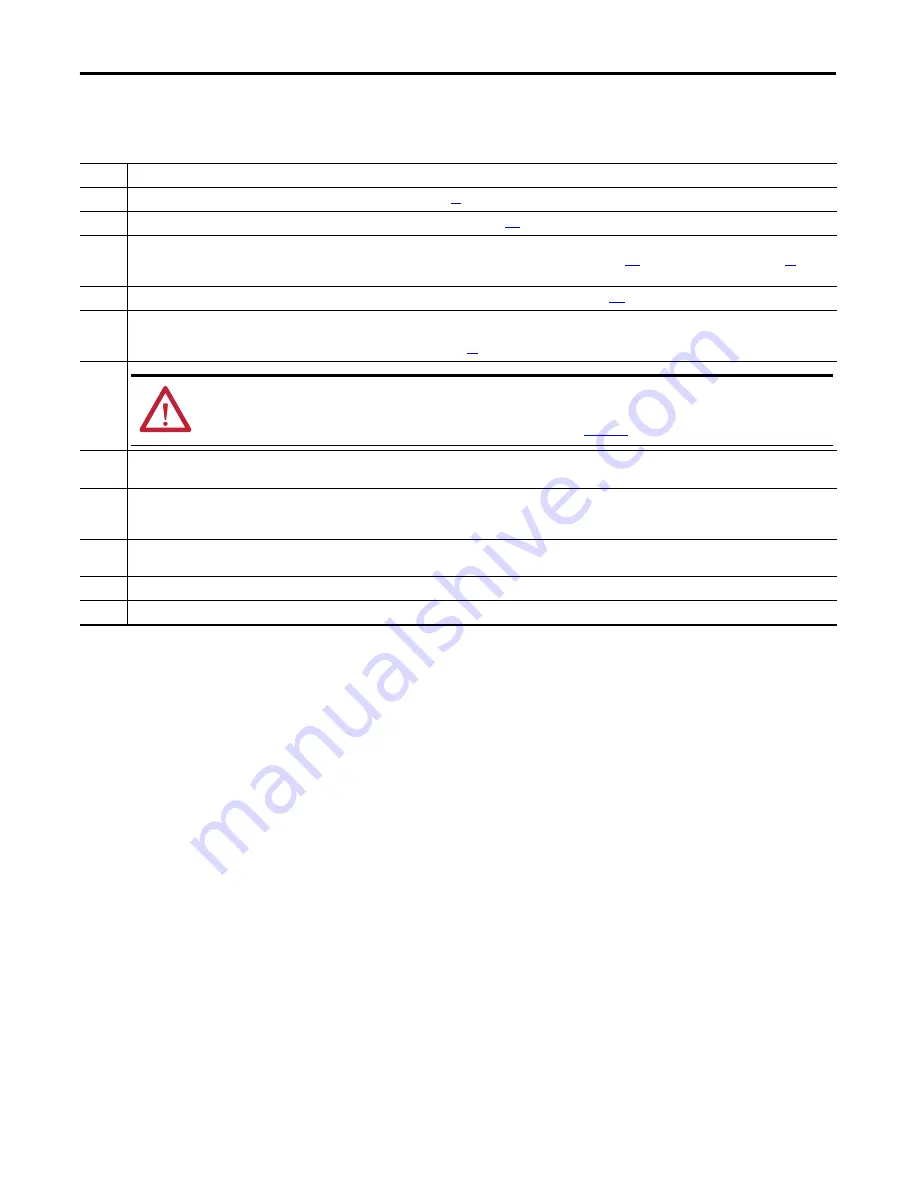
162
Rockwell Automation Publication 2099-UM001D-EN-P - December 2012
Appendix B
Interconnect Diagrams
Interconnect Diagram Notes
The notes below apply to the Kinetix 7000 drive wiring examples on the
following pages.
Note
Information
1
For power wiring specifications, refer to Power Wiring Requirements on page
.
2
For input fuse and circuit breaker sizes, refer to Circuit Breaker/Fuse Specifications on page
and 148.
3
Place AC (EMC) line filters as close to the drive as possible and do not route very dirty wires in wireway. If routing in wireway is unavoidable, use shielded cable with shields
grounded to the drive chassis and filter case. For line filter specifications, refer to the AC Line Filter Specifications on page
. See Establish Noise Zones on page
for wire
routing guidelines.
4
Contactor coil (M1) needs integrated surge suppressors for AC coil operation. Refer to the Contactor Ratings on page
for more information.
5
The default configuration for the ground jumper is for grounded power at the customer site. Ungrounded, impedance grounded, high resistive grounded, B phase
grounded, or common DC bus power distribution system sites must disconnect the protective MOVs and Common Mode Capacitors to guard against unstable operation
and/or drive damage. Refer to Determine the Input Power Configuration on page
6
7
Use of an external 24V DC control power supply is recommended for energizing the main control board. This allows the SERCOS ring to remain active when main power is
removed. The main control board is powered from the DC bus during drive operation and can be used in this manner, if necessary.
8
The General Purpose Relay outputs on the Kinetix 7000 drive are configured as follows: GPR1+ and GRP1- have noise suppression circuitry and should be used for the
motor brake, if used. The default setting for GPR2+ and GPR2- is DROK or Drive_OK. The GPR2 contacts close when external 24V DC control power is applied to the Control
Power terminals and there are no shutdown faults.
9
External AC input power for the cooling fan is required only for 2099-BM09-S, 2099-BM10-S, 2099-BM11-S, and 2099-BM12-S drives. The cooling fans on 2099-BM06-S,
2099-BM07-S, and 2099-BM08-S drives are powered internally.
10
Dual 8720MC-RPS
xxx
units use a ribbon cable to connect the master unit to the slave unit control. The ribbon cable is included with the slave unit.
11
Contact for use with a safety circuit or other system requirement.
ATTENTION:
Implementation of safety circuits and risk assessment is the responsibility of the machine builder. Please
reference international standards EN 1050 and EN 954 estimation and safety performance categories. For more
information, refer to Understanding the Machinery Directive, publication
.