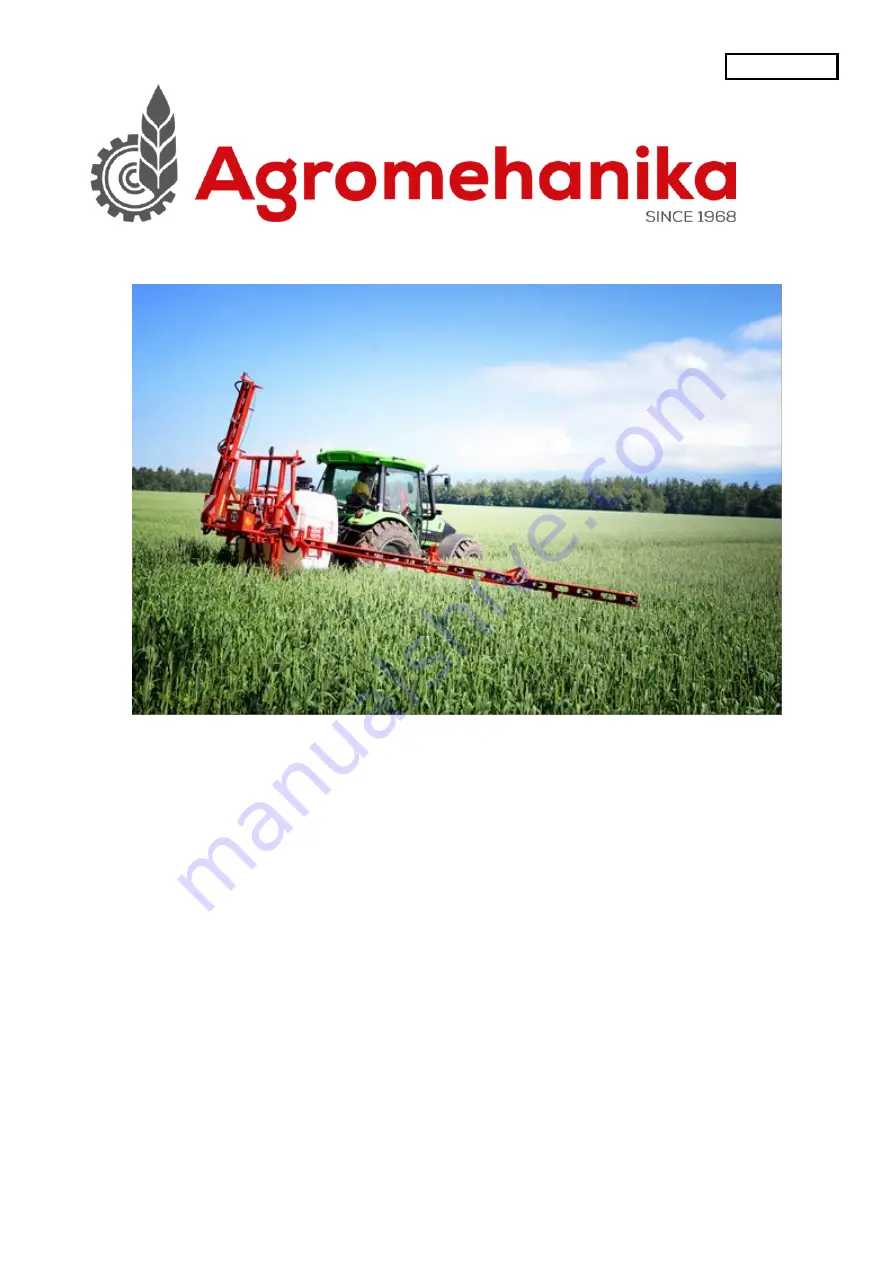
TRACTOR MOUNTED SPRAYERS
AGS 400 EN
AGS 600 EN
AGS 800 EN
AGS 1000 EN
AGS 1200 EN
AND SPRAY BOOMS
10-12-15 MRX, 12 MY, 12 MY-H, 12-15 HLX
INSTRUCTIONS FOR USE
AGROMEHANIKA reserves the right to design modifications or product changes, without any liabilities to inform the
customer before and after each change.
Rev. 12/2018